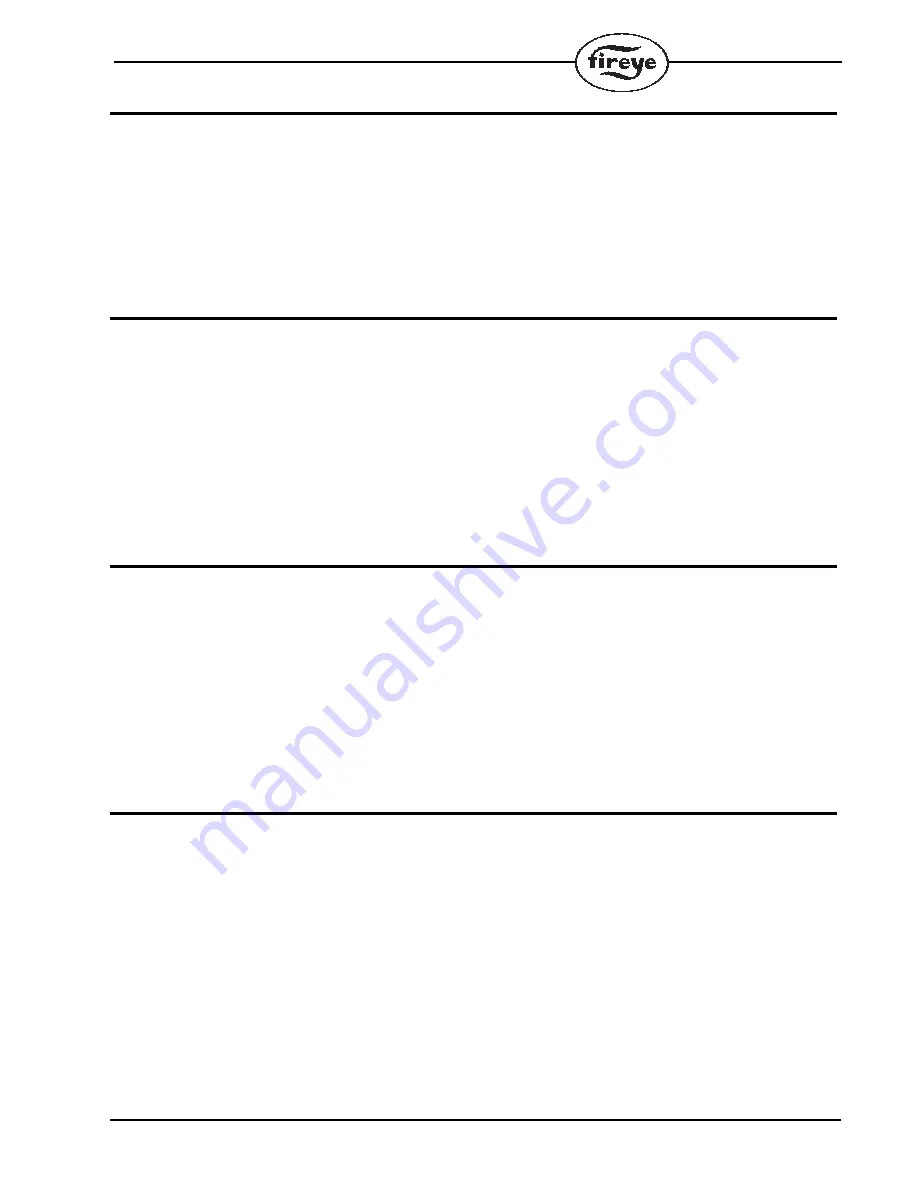
47
COMMUNICATIONS
When interfacing Fireye controls to a communication system, be it an E500, PLC or other micropro-
cessor based device, ferrite cores should also be utilized. Proper twisted shielded pair cable must be
utilized. In a multi-drop system, the shields should be tied together within a cabinet and not to any
ground point. The shield at the source end of the cable of the multi-drop connection can then be ter-
minated to ground. Source end is defined as the originating end of the communication system
Care must be taken not to route communication cables in close proximity to any starter motor con-
tactors located in the control panel or across any high voltage ignition wires. Refer to Fireye bulletin
E-8002 for proper installation.
SCANNERS
The armored cable supplied with the Ultra-Violet and Infrared scanners should be connected to
equipment by means of a good mechanical connection such as a conduit fitting. It may be necessary
to utilize heat insulator (P/N 35-69) to isolate the sensing end of the scanner from boiler ground.
Care must be taken not to route the scanner cable across the high voltage ignition cable. The high
energy ignition cable should be checked periodically for cracking, connections and aging.
In applications using flame rod units and the MERT amplifier, it may be beneficial to route a sepa-
rate return wire from the S1 terminal to the flame rod assembly. This will minimize the effects of
transient currents flowing into the MicroM.
In all cases, scanner wires should be routed in separate conduit and not joined with any high voltage
AC or ignition cables.
MAINTENANCE
Periodically, the spark electrode should be inspected for proper gapping and cracked ceramics. At
ignition time, the high energy from the ignition transformer will attempt to conduct to the point of
least resistance and with an improper spark gap, where the conduction takes place will no longer be
controlled.
The VA rating of the control transformer must be sized to handle the inrush currents of the pilot sole-
noid and ignition transformer at PTFI and then the inrush currents of the main fuel valve assembly at
MTFI time.
Inspect neatness of wiring in junction boxes and cabinets. It is best to have connections short and
direct and also not having wires bunched up and tied off. Also, connections should be periodically
inspected for tightness and corrosion.
INSTALLATION - UV SCANNERS
Where possible, obtain the burner manufacturer’s instructions for mounting the scanner. This infor-
mation is available for most standard burners. The scanner mounting should comply with the follow-
ing general instructions:
1.
Position the UV1A, UV2 scanner within 30 inches of the flame to be monitored; the 45UV5
within 72 inches, closer if possible.
2.
Select a scanner location that will remain within the ambient temperature limits of the UV Scan-
ner. If cooling is required, use an insulating coupling (Fireye P/N 35-69 for UV1A, UV2 Scan-
ners, P/N 35-127-1 for 45UV5) to reduce conducted heat.
3.
The UVlA, UV2, 45UV5 Scanners are designed to seal off the sight pipe up to 1 PSI pressure.
Higher furnace pressures should be sealed off. To seal off positive furnace pressure up to 100
PSI for UV1A, UV2 Scanners, install a quartz window coupling (#60-1257) For 45UV5 Scan-
ners, use #60-1199 coupling. Add cooling air to reduce the scanner sight pipe temperature.
4.
Install the scanner on a standard NPT pipe (UV1A: 1/2", UV2: 3/8", 45UV5: 1") whose position
is rigidly fixed. If the scanner mounting pipe sights through the refractory, do not extend it more
Summary of Contents for MOISTURE Link G2 DP
Page 1: ...Operation Manual 2019 MODELS MSF DP DPSL DPXSL DPX4T DPX8T DPX12T DPX16GT Grain Dryer Controls...
Page 2: ......
Page 4: ...2...
Page 7: ...GENERAL INSTRUCTIONS 3 5...
Page 153: ...151...
Page 154: ...152...
Page 166: ...164...
Page 190: ...188...
Page 200: ...198...
Page 201: ...199...
Page 202: ...200...
Page 203: ...201...
Page 204: ...202...
Page 205: ...203...
Page 206: ...204...
Page 207: ...205...
Page 208: ...206...
Page 209: ...207...
Page 210: ...208...
Page 211: ...209...
Page 212: ...210...
Page 213: ...211...
Page 214: ...212...
Page 215: ...213...
Page 216: ...214...
Page 217: ...215...
Page 218: ...216...
Page 219: ...217...
Page 220: ...218...
Page 221: ...219...
Page 222: ...220...
Page 223: ...221...
Page 224: ...222...
Page 225: ...223...
Page 226: ...224...
Page 227: ...225...
Page 228: ...226...
Page 229: ...227...
Page 242: ...240...
Page 243: ...241...
Page 244: ...242...
Page 245: ...243...
Page 301: ...56 FIGURE 19 Red jumper wire Red wire...
Page 302: ...57...
Page 310: ...2011 Service Manual Rev A 282...
Page 311: ...2011 Service Manual Rev A 283...
Page 312: ...2011 Service Manual Rev A 284...
Page 313: ...2011 Service Manual Rev A 285...
Page 314: ...2011 Service Manual Rev A 286...
Page 315: ...2011 Service Manual Rev A 287...
Page 316: ...2011 Service Manual Rev A 288...
Page 317: ...2011 Service Manual Rev A 289...
Page 318: ...2011 Service Manual Rev A 290...
Page 319: ...2011 Service Manual Rev A 291...
Page 320: ...2011 Service Manual Rev A 292...
Page 321: ...2011 Service Manual Rev A 293...
Page 322: ...2011 Service Manual Rev A 294...