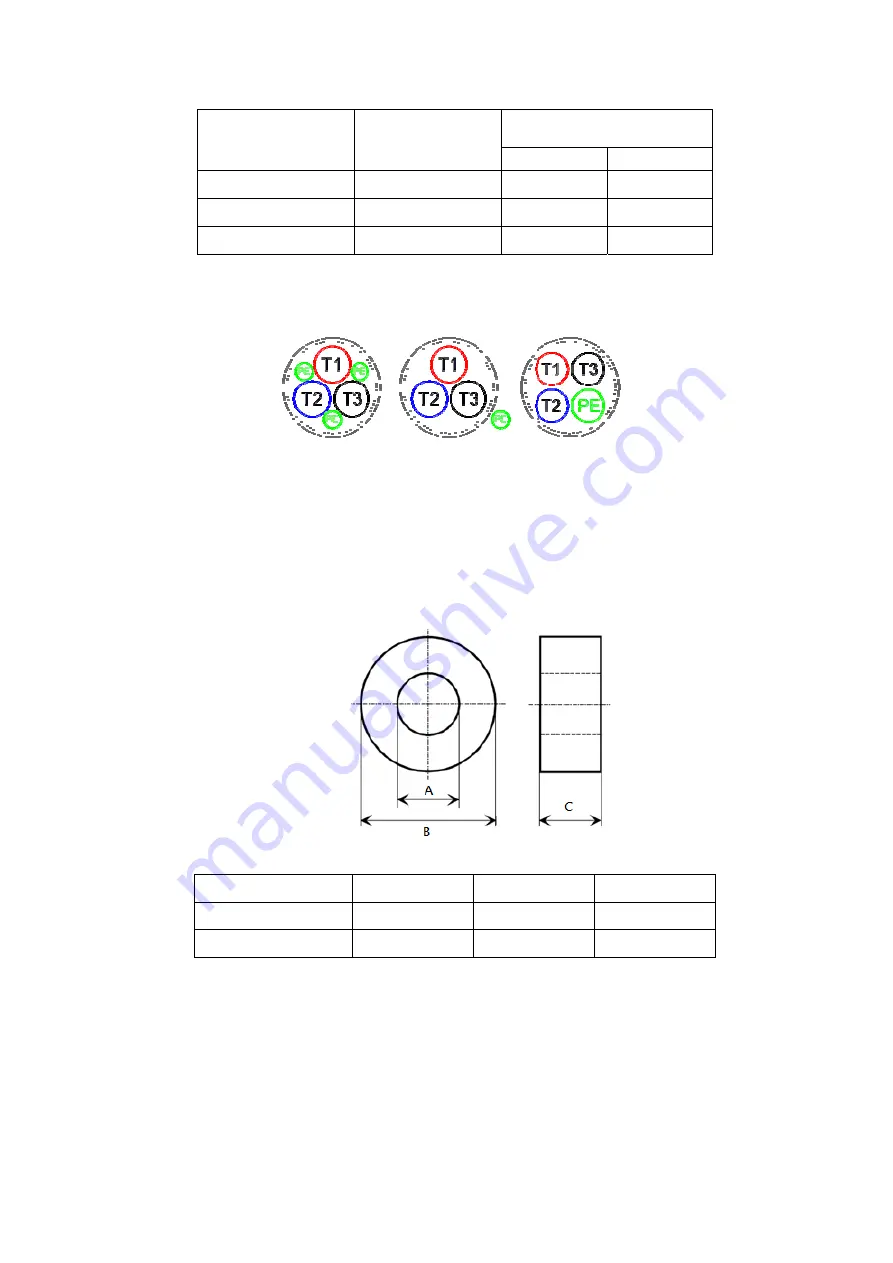
Chapter 7 Optional Accessories
MS300 (IP66 / NEMA 4X)
7-19
Recommended maximum wiring gauge when installing zero phase reactor
Model # of Zero
Phase Reactor
Max. Wire Gauge
or LUG width
Max. Wire Gauge AWG*
75°C
90°C
RF008X00A
13 mm
3 AWG
1 AWG
T600006L2040W453
11 mm
6 AWG
6 AWG
T600006L2050W565
16 mm
1 AWG
1/0 AWG
* Pass the zero phase reactor only through the power inputs (R/L1, S/L2, T/L3) or motor outputs (U/T1, V/T2, W/T3),
not the grounding PE.
Refer to the figures below for the common output wiring methods.
Zero Phase Reactor for Signal Cable
To solve interference problems between signal cables and electric devices, install a zero phase
reactor on signal cable. Install it on the signal cable which is the source of the interference to suppress
the noise for a better signal. The model names and dimensions are listed in the table below.
Unit: mm
Model
A
B
C
T60004L2016W620
10.7
17.8
8.0
T60004L2025W622
17.5
27.3
12.3
Summary of Contents for Compact Drive MS300 IP66/NEMA 4X Series
Page 3: ......
Page 10: ...Chapter 1 Introduction MS300 IP66 NEMA 4X 1 3 1 2 Model Name 1 3 Serial Number...
Page 18: ...Chapter 1 Introduction MS300 IP66 NEMA 4X 1 11 This page intentionally left blank...
Page 24: ...Chapter 2 Dimensions MS300 IP66 NEMA 4X 2 6 This page intentionally left blank...
Page 28: ...Chapter 3 Installation MS300 IP66 NEMA 4X 3 4 This page intentionally left blank...
Page 29: ...Chapter 4 Wiring MS300 IP66 NEMA 4X 4 1 Chapter 4 Wiring 4 1 System Wiring Diagram 4 2 Wiring...
Page 32: ...Chapter 4 Wiring MS300 IP66 NEMA 4X 4 4 4 2 Wiring Figure 4 2...
Page 34: ...Chapter 4 Wiring MS300 IP66 NEMA 4X 4 6 This page intentionally left blank...
Page 83: ...Chapter 7 Optional Accessories MS300 IP66 NEMA 4X 7 33 The drive with MKMX SWA...
Page 85: ...Chapter 7 Optional Accessories MS300 IP66 NEMA 4X 7 35 The drive with MKMX SWB...
Page 87: ...Chapter 7 Optional Accessories MS300 IP66 NEMA 4X 7 37 The drive with MKMX SWC...
Page 126: ...Chapter 10 Digital Keypad MS300 IP66 NEMA 4X 10 8 This page intentionally left blank...