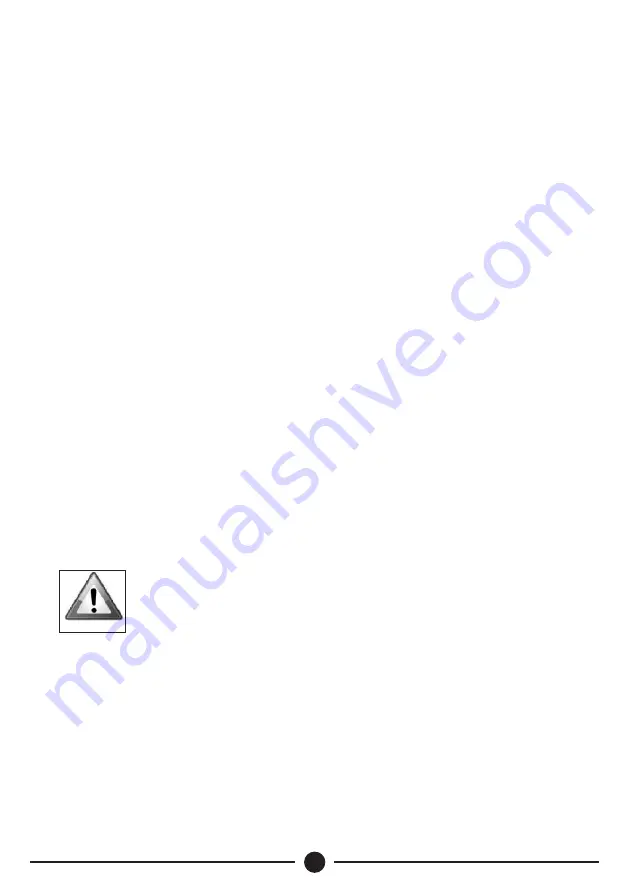
13
Operating Procedures
Ÿ
Select the appropriate welding process (welding rod, welding current and welding
speed) and ensure it does not allow more current than maximum rated of welder
during continuous welding.
Ÿ
The working hours should not exceed the rated duty cycle (60%).
Ÿ
Do not use the welding machine for metal cutting operation
Ÿ
Ensure the welding workplace is dry and well ventilated.
Ÿ
When moving the welding machine cut off the power supply and do not drag on the
floor.
Ÿ
Incase of sudden power failure during welding, stop the generator immediately.
Ÿ
During welding, do not adjust welding current. If required, stop welding and use
adjustment knob to select current.
Ÿ
When welding in wet conditions, operator must stand on the insulation board and
should not touch the welding wire. Avoid using the arm clamp to hold welding clamp
as it can cause electric shock.
Maintenance
Ÿ
After the welding operation is completed, the welding power supply should be cut
off immediately and the welding clamps and welding wires should be cleaned up
to avoid short circuit.
Ÿ
When cleaning the weld slag, wear goggles and pay attention to the head to avoid
the direction of splashing the welding slag, so as not to stab the eyes.
Ÿ
After the open operation is completed, cover the welder well for storage.
CAUTION
Load should be added according to specied parameter in
welding data guide.
Ÿ
Welders, welding tongs, welding wires and joints should be well connected with good
insulation. Ensure there is no overheating of the wiring, the wiring terminal must not be
exposed, it requires cover with insulating tape.
Ÿ
The length of the wire between the welding machine and the welding clamp should be
less than10 metres, maximum length should not exceed 20 metres. Broken or damp
wires should be replaced immediately.
Summary of Contents for DGW 200P
Page 1: ...DGW Installation Operating Manual Welding Generator...
Page 2: ......
Page 26: ......
Page 27: ......
Page 28: ...INS302H 11 22...