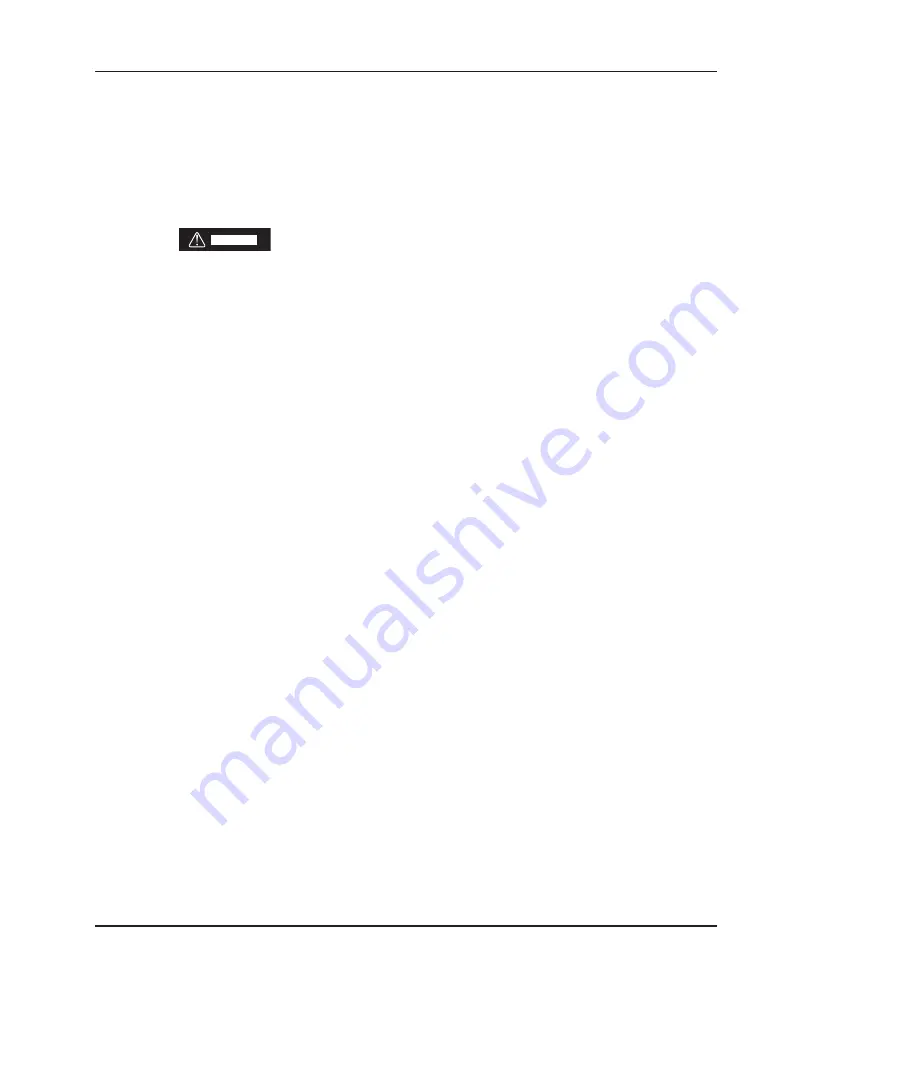
ahiba
27
AHIBA Multiprecise TC – Initial Steps
•
Setup and connect the warm water inlet supply
•
Setup and connect the cool water inlet supply
•
Connect the drain
•
Connect printer (optional)
•
Connect the external alarm lamp (optional)
•
Connect mains power
•
Switch on power
•
Application Information
WARNING
The tube from the drain outlet must be installed so that
human contact with discharging water is impossible.
(Danger of burnings) !
Summary of Contents for Ahiba Ahiba MULTIPRECISE TC
Page 1: ......
Page 3: ......
Page 6: ...ahiba 5 Safety Precautions Safety Precautions and W and Warnings arnings ...
Page 7: ......
Page 11: ......
Page 12: ...ahiba 11 Introduction T Introduction Typical ypical Applications Applications ...
Page 13: ......
Page 16: ...ahiba 15 Main Components Main Components ...
Page 17: ......
Page 25: ......
Page 26: ...ahiba 25 Installation and S Installation and Start Up tart Up ...
Page 27: ......
Page 35: ......
Page 36: ...ahiba 35 T Technical Data echnical Data ...
Page 37: ......
Page 41: ......
Page 42: ...ahiba 41 Procedure for Dosing Procedure for Dosing ...
Page 43: ......
Page 48: ...ahiba 47 Calibration Calibration ...
Page 49: ......
Page 53: ......
Page 54: ...ahiba 53 Controller Controller ...
Page 55: ......
Page 81: ......
Page 82: ...ahiba 81 Protection Protection ...
Page 83: ......
Page 85: ......
Page 86: ...ahiba 85 Maintenance Maintenance ...
Page 87: ......
Page 93: ......
Page 94: ...ahiba 93 Appendices Appendices ...
Page 95: ......