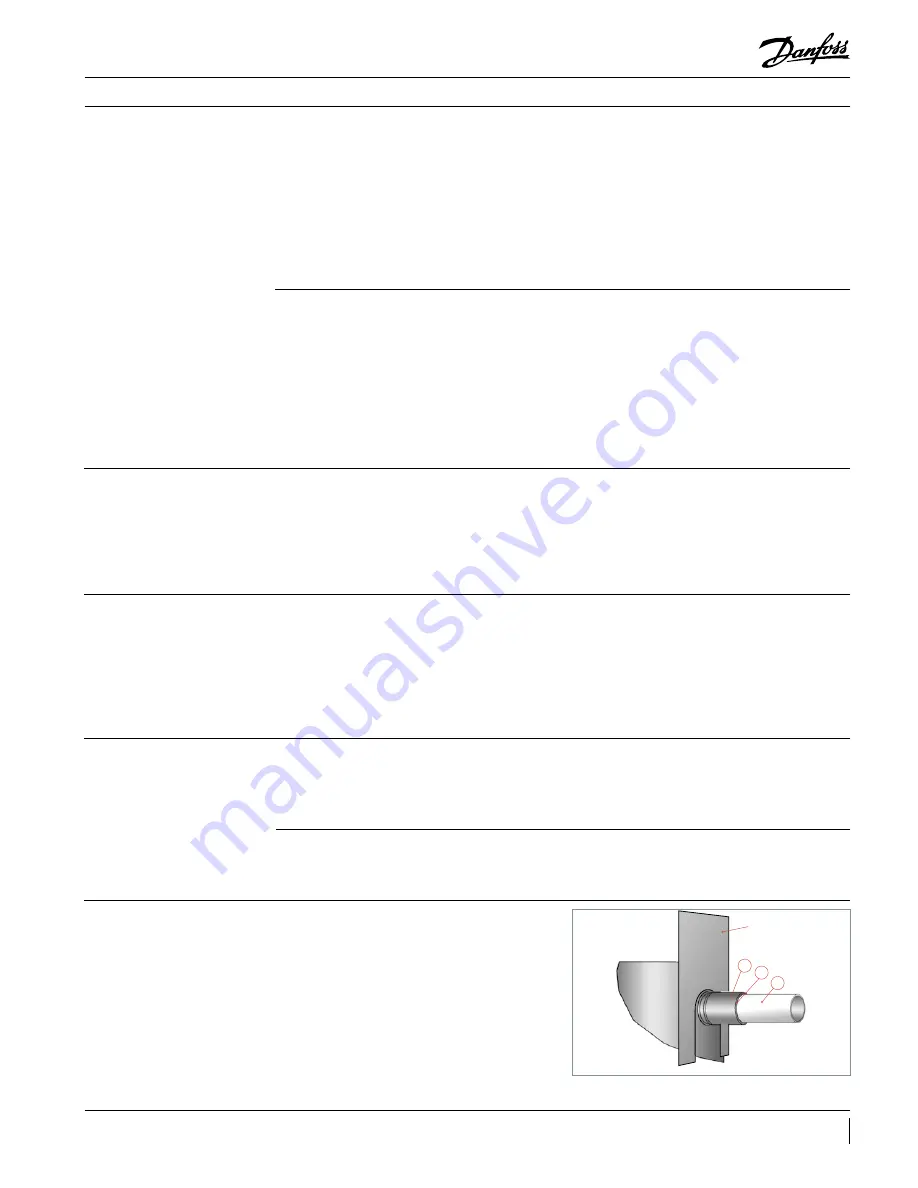
Application guidelines
59
FRCC.PC.023.A7.22
Single compressors
Installation
Tubing
Filter driers
Copper to copper connections
Dissimilar metals connections
Compressor connection
Brazing and soldering
Only use clean and dehydrated refrigeration
grade copper tubing. Tube-cutting must be
carried out so as not to deform the tubing
roundness and to ensure that no foreign debris
remains within the tubing. Only refrigerant grade
fittings should be used and these must be of
both a design and size to allow for a minimum
pressure drop through the completed assembly.
Follow the brazing instructions bellow. Never drill
holes into parts of the pipe-work where filings
and particles can not be removed.
For new installations with VZH compressors with
polyolester oil, Danfoss recommends using the
Danfoss DML 100% molecular sieve, solid core
filter drier. Molecular sieve filter driers with loose
beads from third party suppliers shall be avoided.
For servicing of existing installations where acid
formation is present the Danfoss DCL solid core
filter driers containing activated alumina are
recommended.
The drier is to be oversized rather than
undersized. When selecting a drier, always take
into account its capacity (water content capacity),
the system refrigeration capacity and the system
refrigerant charge.
When brazing copper-to-copper connections,
the use of copper/phosphorus brazing alloy
containing 5% silver or more with a melting
temperature of below 800°C is recommended. No
flux is required during brazing.
When manipulating dissimilar metals such as
copper and brass or steel, the use of silver solder
and anti-oxidant flux is necessary.
When brazing the compressor fittings, do not
overheat the compressor shell, which could
severely damage certain internal components
due to excessive heating. Use of a heat shield
and/or a heat-absorbent compound is highly
recommended. Due to the relatively sizable
tubing and fitting diameters a double-tipped
torch using acetylene is recommended for
brazing operation on VZH compressors.
B
C
A
heat shield
The use of highly hygroscopic polyolester oil
in R410A compressors requires that the oil be
exposed to the atmosphere as little as possible.
System contamination is one of main factors
affecting equipment reliability and compressor
service life. It is important therefore to take
system cleanliness into account when assembling
a refrigeration system. During the manufacturing
process, circuit contamination may be caused by:
• Brazing and welding oxides,
• Filings and particles from the removal of burrs in
pipe-work,
• Brazing flux,
• Moisture and air.
Consequently, when building equipment
and assemblies, the precautions listed in the
following paragraphs must be taken.
System cleanliness
The refrigerant compression system, regardless
of the type of compressor used, will only
provide high efficiency and good reliability,
along with a long operating life, if the system
contains solely the refrigerant and oil it was
designed for. Any other substances within the
system will not improve performance and, in
most cases, will be highly detrimental to system
operations. The presence of non-condensable
substances and system contaminants such as
metal shavings, solder and flux, have a negative
impact on compressor service life. Many of these
contaminants are small enough to pass through a
mesh screen and can cause considerable damage
within a bearing assembly.