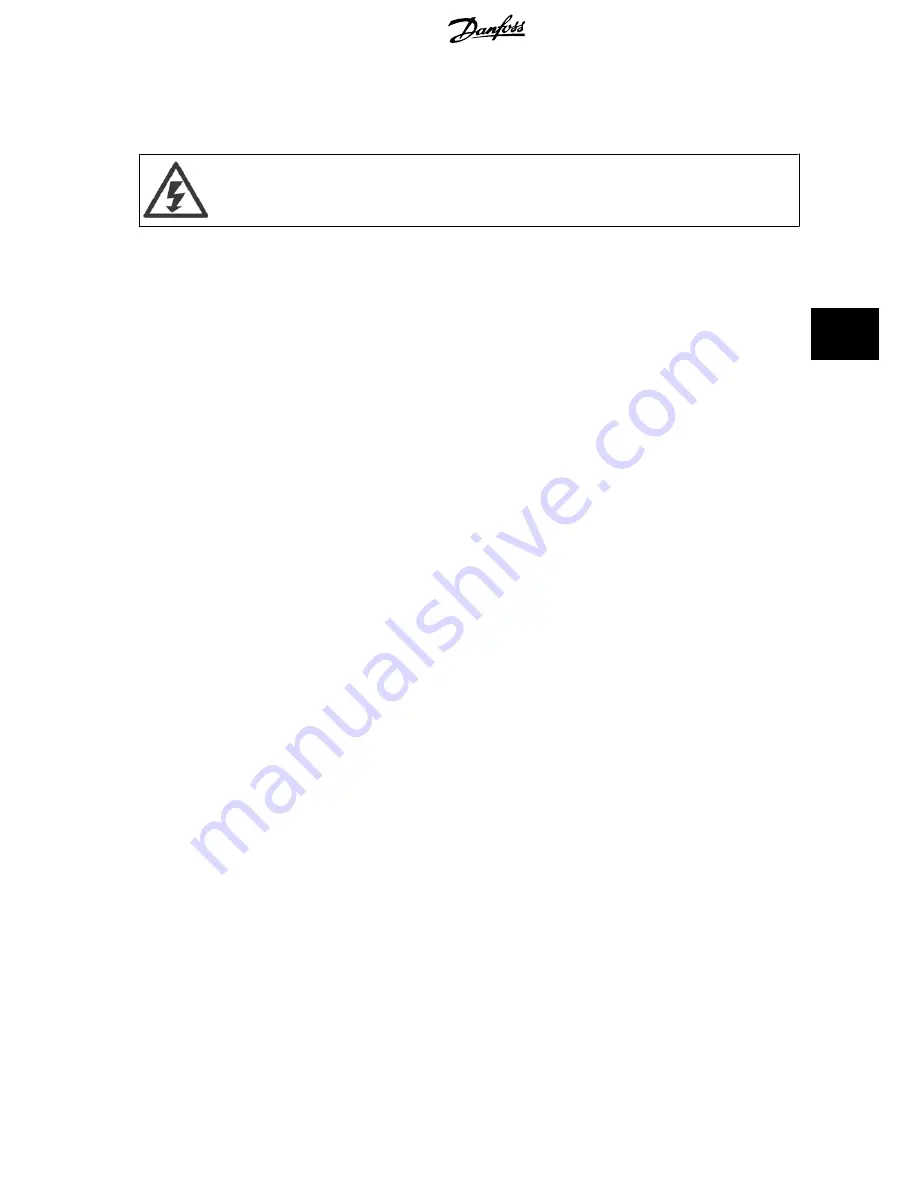
5.10.2 Safety Earth Connection
The frequency converter has a high leakage current and must be earthed appropriately for safety reasons acording to EN 50178.
The earth leakage current from the frequency converter exceeds 3.5 mA. To ensure a good mechanical connection from the earth
cable to the earth connection (terminal 95), the cable cross-section must be at least 10 mm2 or 2 rated earth wires terminated sepa-
rately.
5.11 EMC-correct Installation
5.11.1 Electrical Installation - EMC Precautions
The following is a guideline to good engineering practice when installing frequency converters. Follow these guidelines to comply with EN 61800-3
First
environment
. If the installation is in EN 61800-3
Second environment,
i.e. industrial networks, or in an installation with its own transformer, deviation
from these guidelines is allowed but not recommended. See also paragraphs
CE Labelling,
General Aspects of EMC Emission
and
EMC Test Results
.
Good engineering practice to ensure EMC-correct electrical installation:
•
Use only braided screened/armoured motor cables and braided screened/armoured control cables. The screen should provide a minimum
coverage of 80%. The screen material must be metal, not limited to but typically copper, aluminium, steel or lead. There are no special re-
quirements for the mains cable.
•
Installations using rigid metal conduits are not required to use screened cable, but the motor cable must be installed in conduit separate from
the control and mains cables. Full connection of the conduit from the drive to the motor is required. The EMC performance of flexible conduits
varies a lot and information from the manufacturer must be obtained.
•
Connect the screen/armour/conduit to earth at both ends for motor cables as well as for control cables. In some cases, it is not possible to
connect the screen in both ends. If so, connect the screen at the frequency converter. See also
Earthing of Braided Screened/Armoured Control
Cables
.
•
Avoid terminating the screen/armour with twisted ends (pigtails). It increases the high frequency impedance of the screen, which reduces its
effectiveness at high frequencies. Use low impedance cable clamps or EMC cable glands instead.
•
Avoid using unscreened/unarmoured motor or control cables inside cabinets housing the drive(s), whenever this can be avoided.
Leave the screen as close to the connectors as possible.
The illustration shows an example of an EMC-correct electrical installation of an IP 20 frequency converter. The frequency converter is fitted in an
installation cabinet with an output contactor and connected to a PLC, which is installed in a separate cabinet. Other ways of doing the installation may
have just as good an EMC performance, provided the above guide lines to engineering practice are followed.
If the installation is not carried out according to the guideline and if unscreened cables and control wires are used, some emission requirements are not
complied with, although the immunity requirements are fulfilled. See the paragraph
EMC test results
.
VLT
®
AQUA Drive Design Guide
5 How to Install
MG.20.N5.02 - VLT
®
is a registered Danfoss trademark
155
5