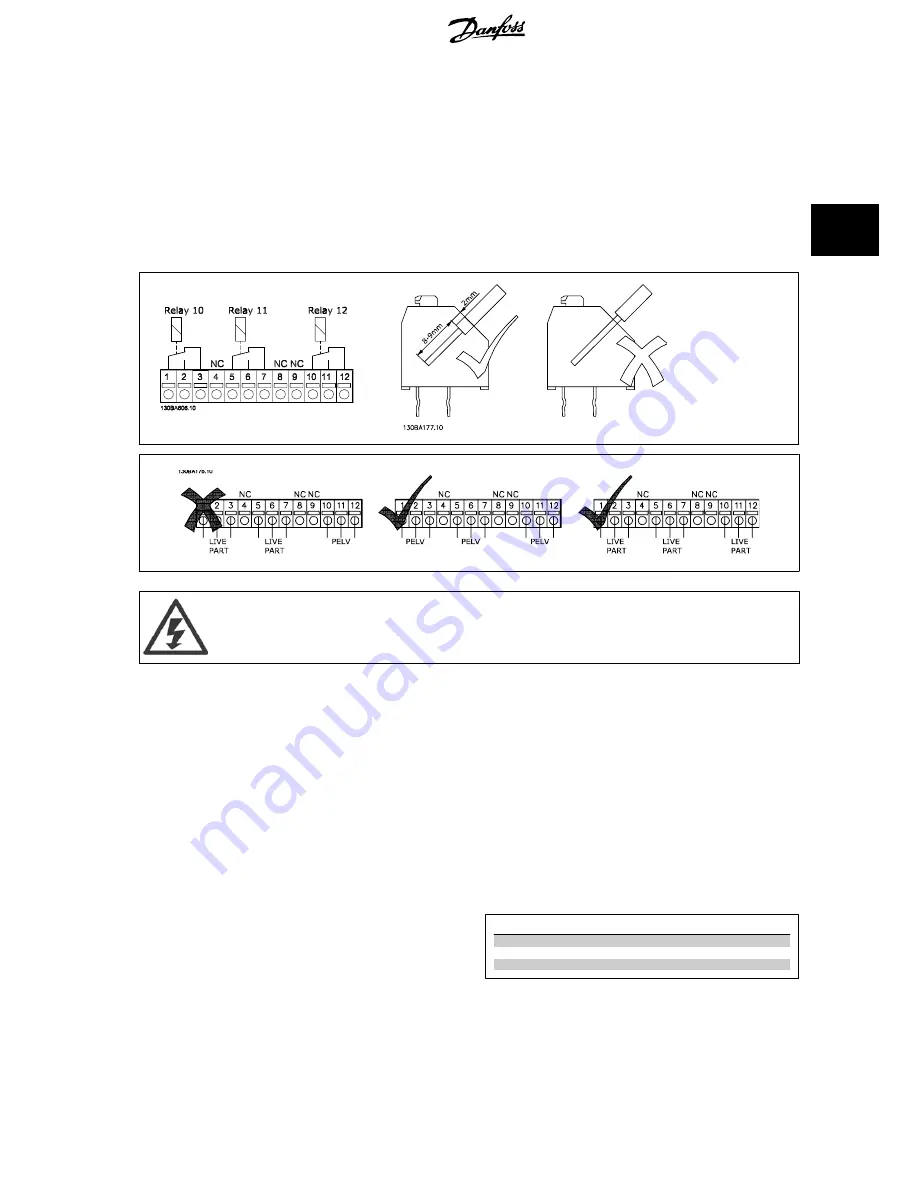
•
The power to the live part connections on relay terminals must be disconnected.
•
Remove the LCP, the terminal cover and the cradle from the FC 202.
•
Fit the MCO 101 option in slot B.
•
Connect the control cables and relief the cables by the enclosed cable strips.
•
Various systems must not be mixed.
•
Fit the extended cradle and terminal cover.
•
Replace the LCP
•
Connect power to the frequency converter.
Wiring the Terminals
Do not combine low voltage parts and PELV systems.
3.6.13 Brake Resistors
In applications where the motor is used as a brake, energy is generated in the motor and send back into the frequency converter. If the energy can not
be transported back to the motor it will increase the voltage in the converter DC-line. In applications with frequent braking and/or high inertia loads this
increase may lead to an over voltage trip in the converter and finally a shut down. Brake resistors are used to dissipate the excess energy resulting from
the regenerative braking. The resistor is selected in respect to its ohmic value, its power dissipation rate and its physical size. Danfoss offers a wide variety
of different resistors that are specially designed to our frequency converters. See the section
Control with brake function
for the dimensioning of brake
resistors. Code numbers can be found in the section
How to order
.
3.6.14 Remote Mounting Kit for LCP
The Local Control Panel can be moved to the front of a cabinet by using
the remote build in kit. The enclosure is the IP65. The fastening screws
must be tightened with a torque of max. 1 Nm.
Technical data
Enclosure:
IP 65 front
Max. cable length between and unit:
3 m
Communication std:
RS 485
VLT
®
AQUA Drive Design Guide
3 VLT AQUA Selection
MG.20.N5.02 - VLT
®
is a registered Danfoss trademark
77
3