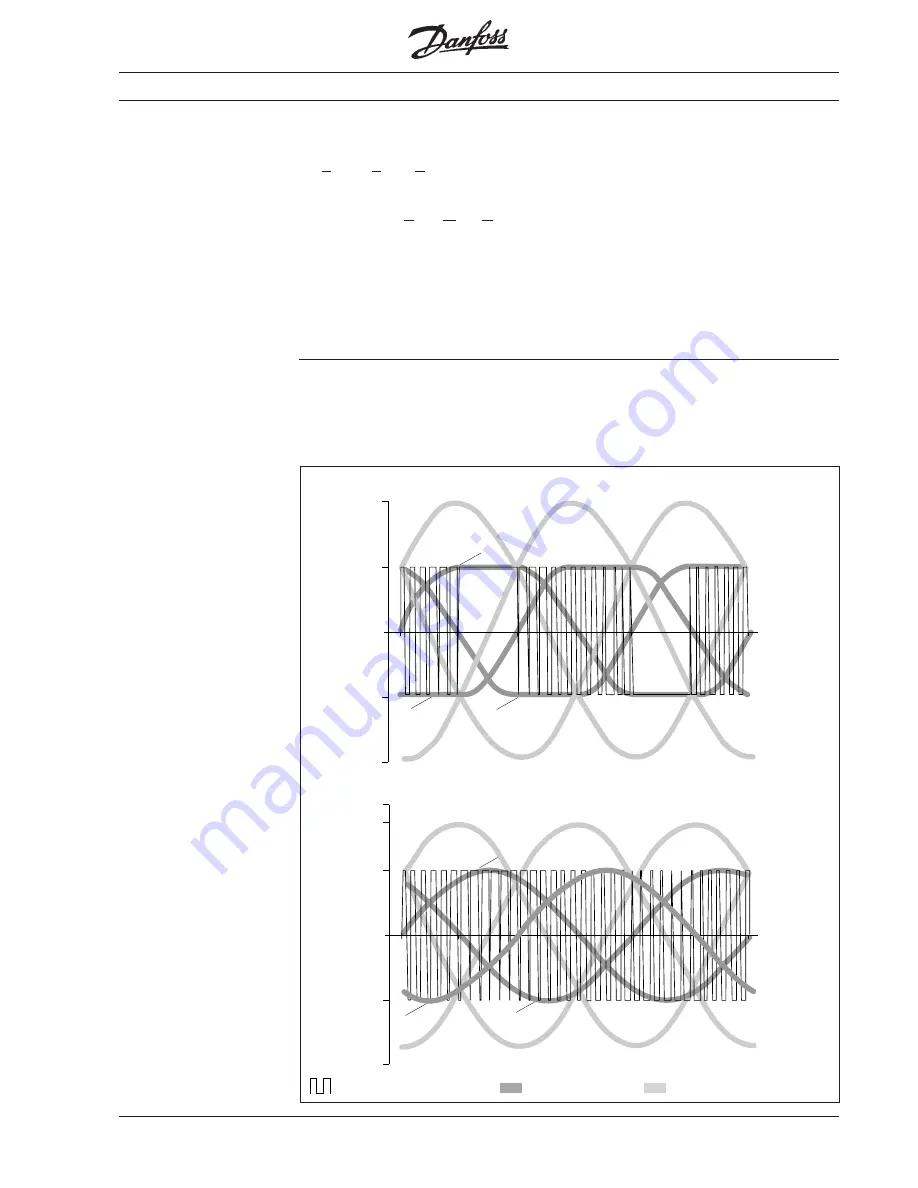
9
MG.30.A7.02 - VLT
®
is a registered Danfoss trademark
The features are obtained through a
special switching pattern: the switching
intervals are very short, which means high
switching frequency, and the six semi-
conductors of the inverter section are
alternately held inactive, in pairs, through-
out a 60
°
sine period. The current wave
form of the motor current closely resembles
that obtained on mains operation. The
switching pause in 60
°
of the sine period
also means that full-rated motor voltage
can be obtained – and inverter switching
losses are reduced by about one third.
The figures below show the switching
pattern and the maximum motor voltage in
relation to the mains voltage according to
the VVC principle and the traditional PWM
principle, respectively.
The full-rated motor voltage and the
perfect current wave form mean that the
Danfoss
VLT
®
3000 Series allows full mo-
tor performance without any derating –
just like running the motor on the mains.
Technology
VLT
®
3000 Series frequency converters
use an inverter control system known as
the Voltage Vector Control (VVC)
developed by Danfoss.
The VVC principle is superior to the
traditional PWM (Pulse Width Modulation)
principle used in most modern frequency
converters in the following ways:
•
Full-rated motor voltage at rated motor
frequency
•
Near perfect resemblance to the
sinusoidal mains supply
•
Extremely low switching losses, resulting
in high converter efficiency
U
V
W
U
W
V
0,50
0,00
1,00
-0,50
-1.00
0
60
120
180
300
360
240
U-V
U-W
W-U
0,50
0,00
1,00
-0,50
-1.00
0
60
120
180
300
360
240
0,866
U-V
V-W
W-U
Motor voltage and switching pattern with the traditional PWM principle
Motor voltage and simplified switching pattern with the Danfoss VVC principle
Switching pattern for phase U
Single-phase voltage
Phase-phase voltage for motor