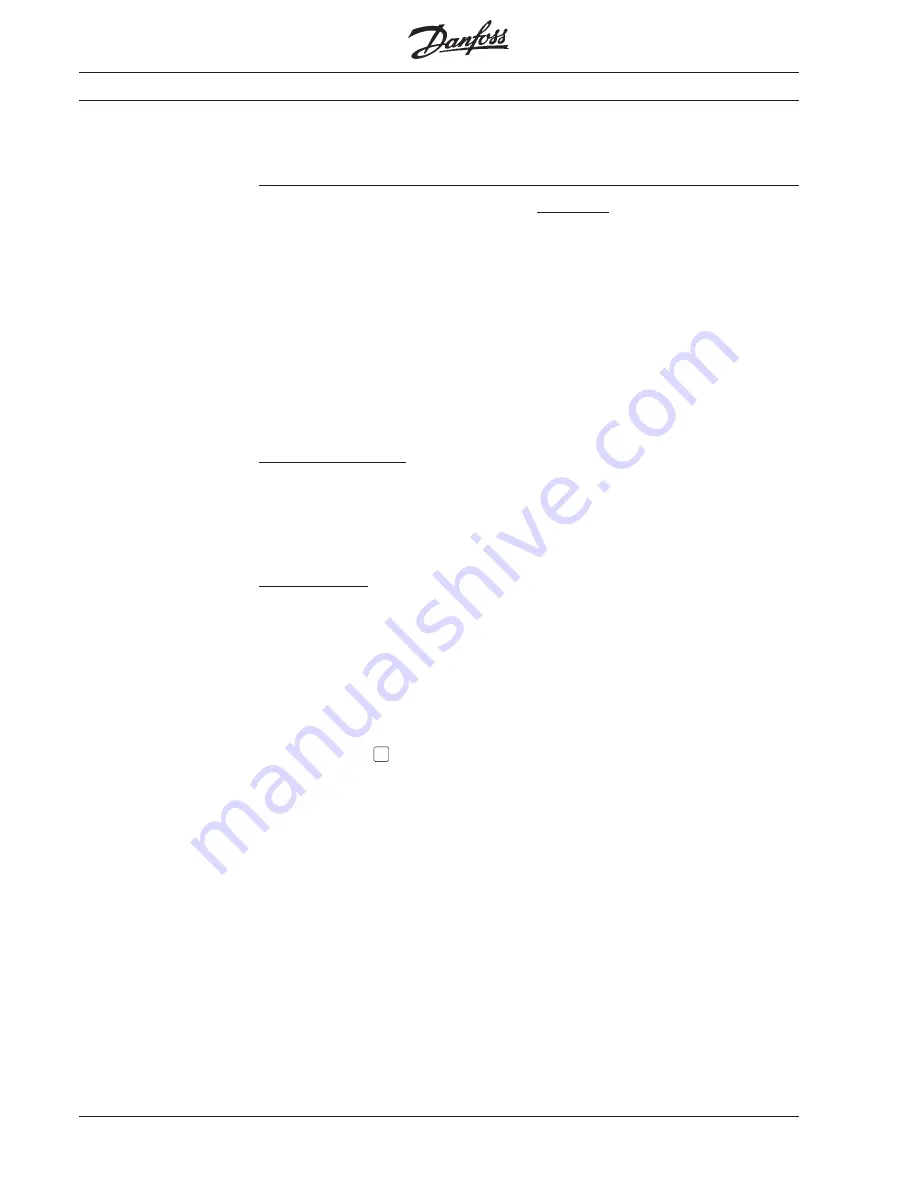
66
MG.30.A7.02 - VLT
®
is a registered Danfoss trademark
Group description
Note: The choice between the 12 different
display read-outs mentioned on page 60 is
not an element of this group.
Load and motor
Group 1..
Operation and display
Group 0..
In this group you will find parameters
concerning the display read-out, local
operation and setup handling.
This group of parameters has been re-
ser-ved for the adjustments necessary to
adapt the VLT
®
frequency converter to the
application and motor.
The preprogrammed values in parameters
100-105 are suitable for normal application
using standard asynchronous motors with
constant torque load without parallel-
coupled motors.
If quadratic torque load is applied, select
one of the VT (variable torque) modes or VT
modes with CT starting torque (high break-
away torque).
Parallel-coupled motors:
If parallel-coupled motors or any synchro-
nous type of motor are used at the output
from a VLT
®
frequency converter, constant
torque is selected without start compensa-
tion in parameter 100, and open-loop speed
control is selected in parameter 101.
Auto-optimization:
An additional tuning might improve the
torque yield or speed accuracy, if the motor
data differ from the typical values assumed
as default.
Items 1-4 in Quick setup must be carried out
first.
The adaptive tuning facility offers you an
easy way to perform that tuning. Initiate
the tuning by setting parameter 106 to
"ON" and pressing
Start
.
The VLT
®
will perform a test measurement
of vital motor data and automatically adjust
the appropriate parameters (108-113).
For optimum adjustment automatic para-
meter tuning on a cold motor is recom-
mended.
Caution:
the motor will start running without
warning.
Manual tuning is possible in parameters
109-113 for correction of default or auto-
matically tuned values.
Closed loop
If closed loop control is required the trans-
mitter, tachometer or encoder should sup-
ply one of the standard analogue signals
(e.g. 0-10 V, 0-20 mA; 4-20 mA) or a pulse
signal frequency of max. 100 Hz, 1 kHz or
10 kHz (programmable).
The full-scale value is always 100%.
The transmitter signal should be selected
to utilise the full scale range as far as
possible, but with due allowance for over-
shooting.
The pulse signal has an over-shooting
range of up to 200% for the 100 Hz and
1 kHz signals, and up to 130% for the
10 kHz signal.
To optimise dynamics and accuracy an im-
pulse frequency as close to 10 kHz as pos-
sible should be selected (at max.
motor speed).
If this is not possible, the transmitter signal
can be corrected by the feedback scaling
factor (parameter 125).
The equivalent reference signal can either
be fixed internally (digital reference) or sup-
plied via standard analogue signals or the
pulse signal (range 0-100%). It is not possi-
ble to select the same type of signal (volt-
age, current, pulses) for both the reference
and the feedback.
At start the output frequency is determined
by the frequency converter’s reference and
the feed forward factor and the min/max
frequency settings. The feed forward factor
is used to set the steady state output fre-
quency.
Feedback scaling is used if the transmitter
cannot be optimally selected for the input
signals’ scale range.
The PID regulator then adjusts the output
frequency by comparing reference and
feedback.
At stop the controller output (integrator) is
set to 0 so that a restart follows the normal
start situation.
Continued...