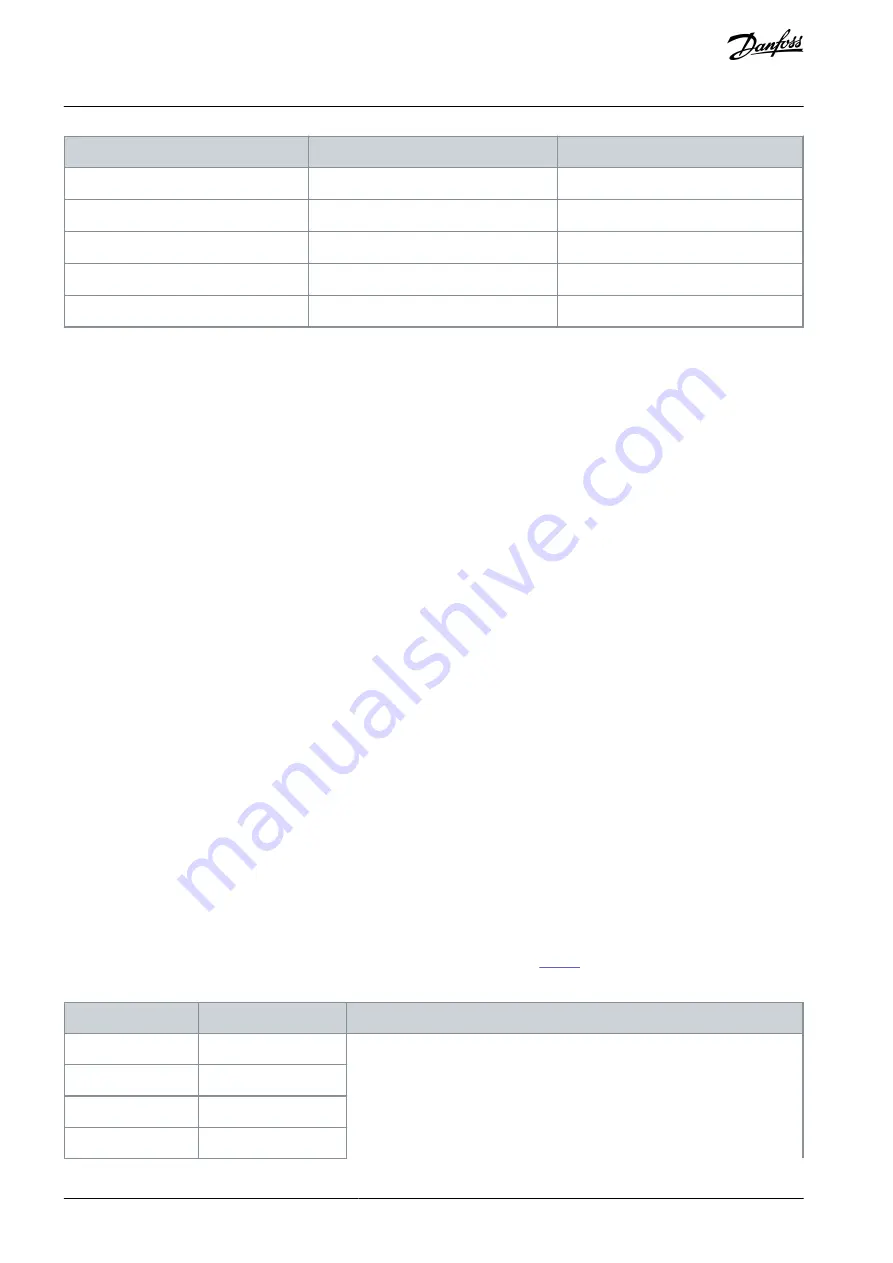
•
•
•
•
•
•
•
•
•
•
•
Input/output current rating
Conductor specification, IEC
Conductor specification, UL
≤410 A
240 mm
2
500 kcmil
≤460 A
300 mm
2
500 kcmil
≤530 A
400 mm
2
750 kcmil
≤600 A
500 mm
2
750 kcmil
≤680 A
630 mm
2
1000 kcmil
6.8 Additional Instructions for Cable Installation
For the specific wiring scheme, see the site wiring diagram. Note the following during cabling:
Only use symmetrically EMC shielded cables between the drive and other equipment (high voltage power cabinet and motor).
To avoid interference, route the control signals, communication, power source cables, and power motor separately rather than
in the same cabling slot. If separate routing is impossible, the spacing between the control, signal, communication and power
source cables, and power motor cables must be >30 cm.
If it is possible, do not put the motor cables in long parallel lines with other cables.
For the control signals, use multi-core wire with a shielding layer, wherein the shielding layer is equipotentially grounded at
both ends and is not too long.
The wires used to transmit different signals must be routed in an alternative and mutually vertical way, for example AC signal
and DC signal.
6.9 Control Wiring
6.9.1 Control Cable Selection
Control power cables
Use low-voltage cables with PVC or XLPE insulations of copper, with shield, and in single or multi-core constructions.
Cable specification for input voltage 208–600 V:
Solid type cable, 2.5–6.0 mm
2
, or 14–10 AWG.
Flexible type cable, 4.0 mm
2
, or 12 AWG.
Cable specification for input voltage 120 V:
Solid type cable, two parallel connected cables, 2.5–6.0 mm
2
, or 14–10 AWG.
Flexible type cable, two parallel connected cables, 4.0 mm
2
, or 12 AWG.
Control signal cables
Use control cables with XLPE or PVC insulation, with screening, and in multi-core constructions.
Solid type cable, 1.0–4.0 mm
2
, or 17–12 AWG.
Flexible type cable, 2.5 mm
2
, or 13 AWG.
6.9.2 Control Power Wiring
Connect L and N of the control power to terminals 1 and 7 in terminal block X12. See
.
Table 7: Connections to Terminal Block X12
Terminal
Definition
Description
1
L1
220 V AC, 1-phase, 50 Hz
230 V AC, 1-phase, 60 Hz
600 V AC, 1-phase, 50/60 Hz
2
L1
3
L2
4
L2
AQ363633621020en-000201 / 172F3117
54 | Danfoss A/S © 2021.06
Electrical Installation
VACON® 1000
Operating Guide
Summary of Contents for VACON 1000
Page 1: ...Operating Guide VACON 1000 drives danfoss com...
Page 2: ......