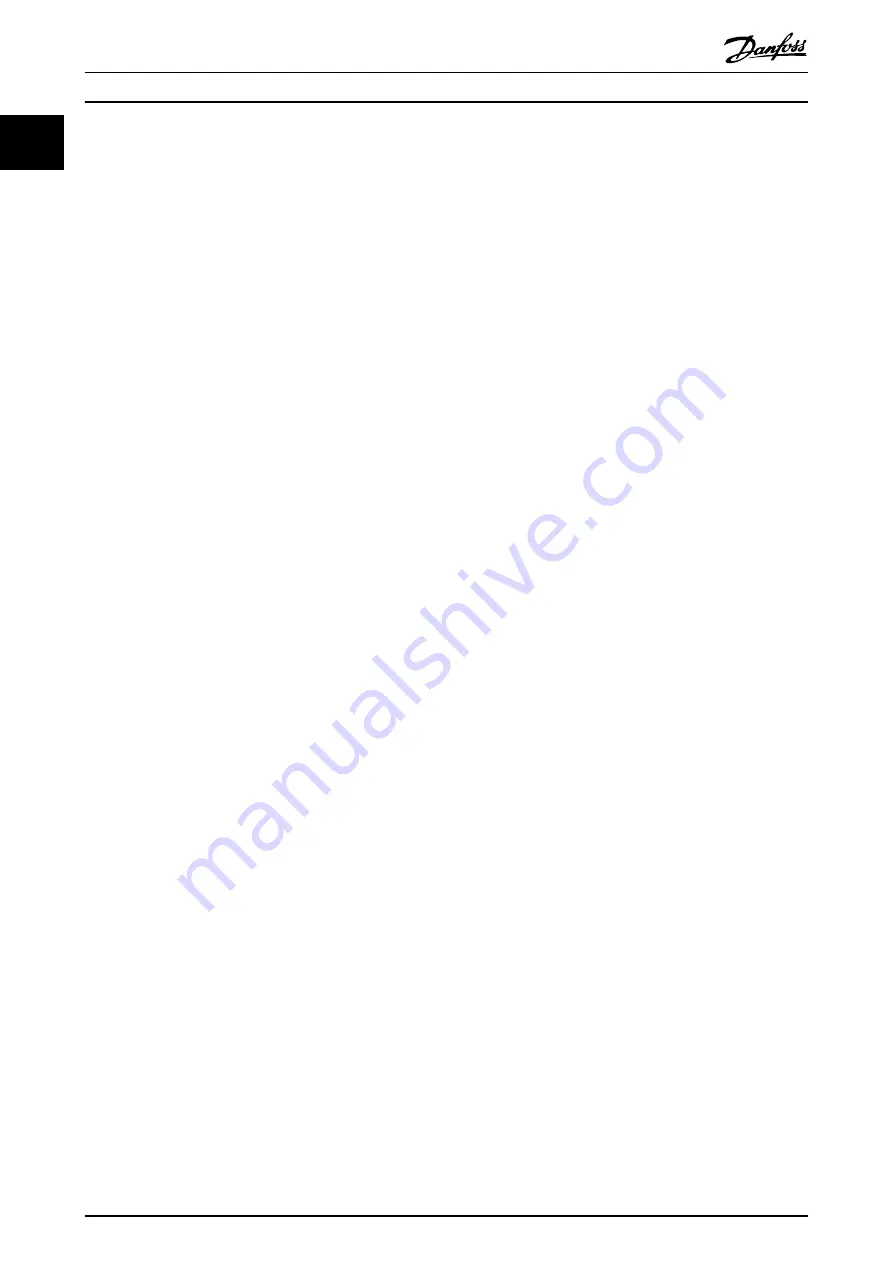
1 Introduction
1.1 Purpose of the Manual
These Operating Instructions provide information for safe
installation and commissioning of the VLT
®
Positioning
Controller MCO 351. The Operating Instructions are
intended for use by qualified personnel. Read and follow
the Operating Instructions to use the product safely and
professionally, and pay particular attention to the safety
instructions and general warnings. Keep these Operating
Instructions available with the MCO 351 at all times.
Compliance with the information in these Operating
Instructions is a prerequisite for:
•
Trouble-free operation
•
Recognition of product liability claims
Therefore, read the Operating Instructions before working
with the MCO 351.
VLT
®
is a registered trademark.
1.2 Additional Resources
Resources available to understand advanced frequency
converter and MCO functions and programming:
•
VLT
®
AutomationDrive FC 301/FC 302 Operating
Instructions
•
VLT
®
AutomationDrive FC 301/FC 302 Design
Guide
•
VLT
®
AutomationDrive FC 301/FC 302
Programming Guide
•
Motion Control Option MCO 305 Operating
Instructions
•
Motion Control Option MCO 305 Design Guide
Supplementary publications and manuals are available
from Danfoss. See
www.danfoss.com/BusinessAreas/DrivesSo-
lutions/Documentations/VLT+TeDocumentation.htm
for listings.
1.3 Overview
The VLT
®
Positioning Controller MCO 351 is for use with
the FC 300 series frequency converters. The control card
option expands the functional properties of the frequency
converter in positioning applications. It is user-friendly,
enabling the set-up of all parameters via the VLT
®
AutomationDrive Local Control Panel (LCP) or via the VLT
®
MCT 10 Set-up Software.
The module is available as an option card for field instal-
lation or as a built-in option in all VLT
®
AutomationDrives.
It is available with and without conformal coating.
As the MCO 351 is a standard product with fixed
functional properties, no additional application
programming is required.
The positioning controller can handle most positioning
applications with vertical as well as horizontal movements.
The option is suited for applications with an overall control
system, for example a PLC.
The main features are:
•
Direct positioning via fieldbus
•
Relative, absolute, and touch probe positioning
•
32 fixed positions (64 via fieldbus)
•
End limit handling (software and hardware)
•
Mechanical brake handling
•
Error handling
•
Jog speed/manual operation
•
Home function
•
Auto PID calculation
1.3.1 Software Version
Refer to parameter
19-90 Type/Version
for the software
version number.
Introduction
Operating Instructions
4
Danfoss A/S © 04/2014 All rights reserved.
MG33R302
1
1