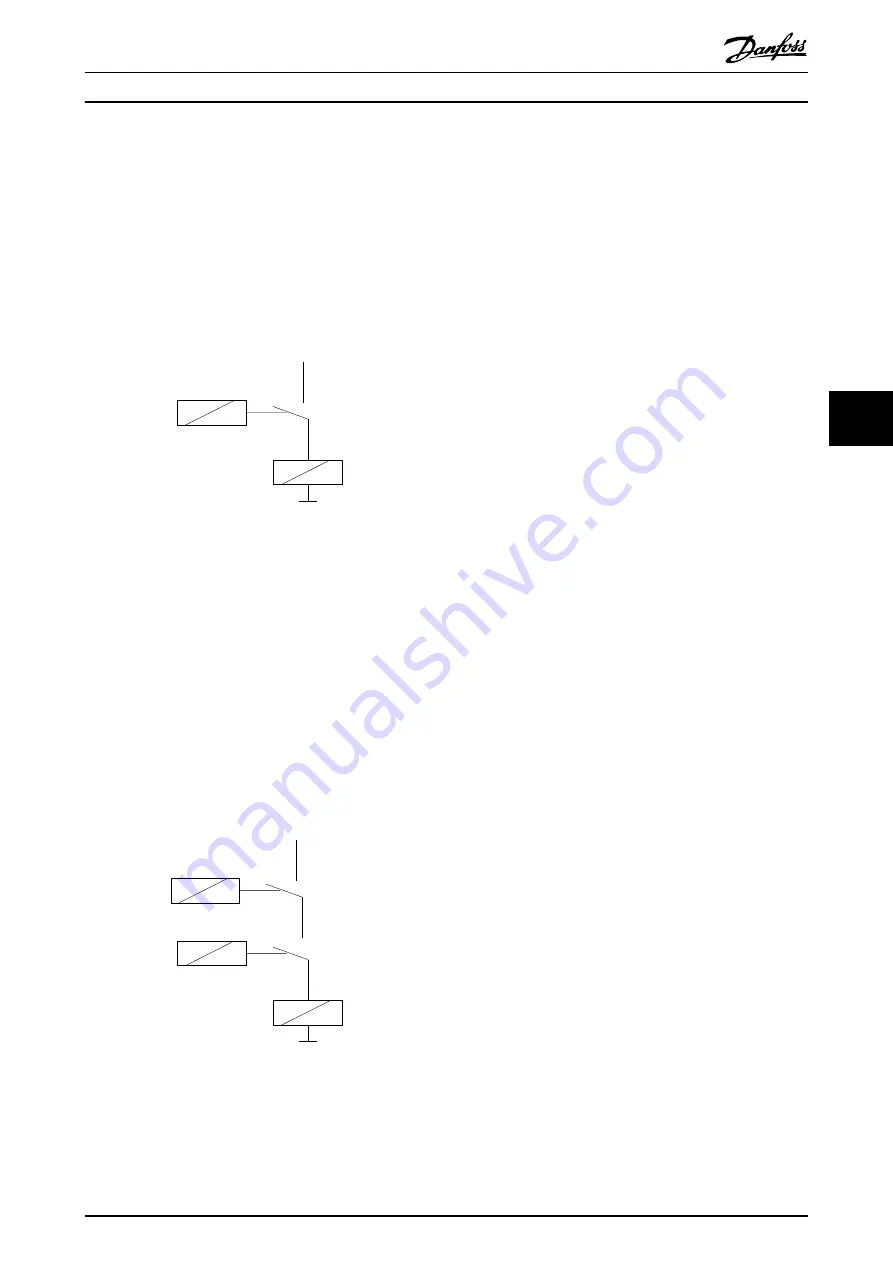
Parameter 19-12 Hold delay
Especially used for applications where a sequence of fast
positioning is followed by a longer standstill time. It
defines the time period in which the brake is not activated,
even though the application is at standstill. This spares the
brakes for wear for rapid positioning.
Parameter 19-13 Brake wear limit
Monitors the wear of the brake. It defines the numbers of
user units the motor can move while the brake is closed.
130BB998.10
MCO351
controlled
Mech. brake
+
Illustration 6.3 MCO Controlled Brake
Using both FC 300 and MCO brake control
For extra safety both MCO and FC 300 can be used for
mechanical brake control. The FC 300 only has influence
during start-up. In normal conditions, after the time in
parameter
19-11
, the current activating the FC brake
control should be reached. If the MCO loses control over
the motor and the controller cannot magnetise the motor,
the brake cannot open. Without FC brake control, the
brake opens shortly and closes again because of
position
error
. It is important to optimise the time in parameter
19-11 Brake Delay
according to the maximum allowed
position error.
130BB999.10
FC300
controlled
MCO351
controlled
+
Relay 1
Relay 2
Illustration 6.4 MCO and FC 300 Controlled Brake
6.4 Hardware End Limit
The hardware end limit switch is an emergency switch for
the application.
Inputs:
•
X57/2: Positive hardware limit switch input
•
X57/3: Negative hardware limit switch input
Must be kept high to start/run the application.
6.5 Software Limits
The software limits are placed just in front of the hardware
limit switches with a distance to the hardware limit
switches, which allows for the motor to be stopped with
the shortest allowable ramp before the HW limit switch is
activated.
Parameters:
•
33-41: Negative Software Limit
•
33-42: Positive Software Limit
•
33-43: Negative Software Limit Active
•
33-44: Positive Software Limit Active
Either both or no software limits must be active. Activating
only one border is not valid. The motor must be
repowered after activating or deactivating software limits.
6.6 Index Positioning
Positions with individual ramps, velocity, and positioning
type can be predefined in the VLT
®
Positioning Controller
MCO 351.
•
64 positions when using fieldbus option.
•
32 positions when using digital I/O and FC 302.
•
16 positions when using digital I/O and FC 301.
Parameters used for definition of index positioning:
•
19-23: Reference Index No.
•
19-24: Index Target Position (UU)
•
19-25: Index Ramp Up Time (ms)
•
19-26: Index Ramp Down Time (ms)
•
19-27: Index Maximum Velocity (RPM, on the
encoder side)
•
19-28: Index Trajectory Type (absolute, relative, or
touch probe)
•
19-29 Parameter Save
: Save parameter settings for
19-24
to
19-28
Application Examples
Operating Instructions
MG33R302
Danfoss A/S © 04/2014 All rights reserved.
43
6
6