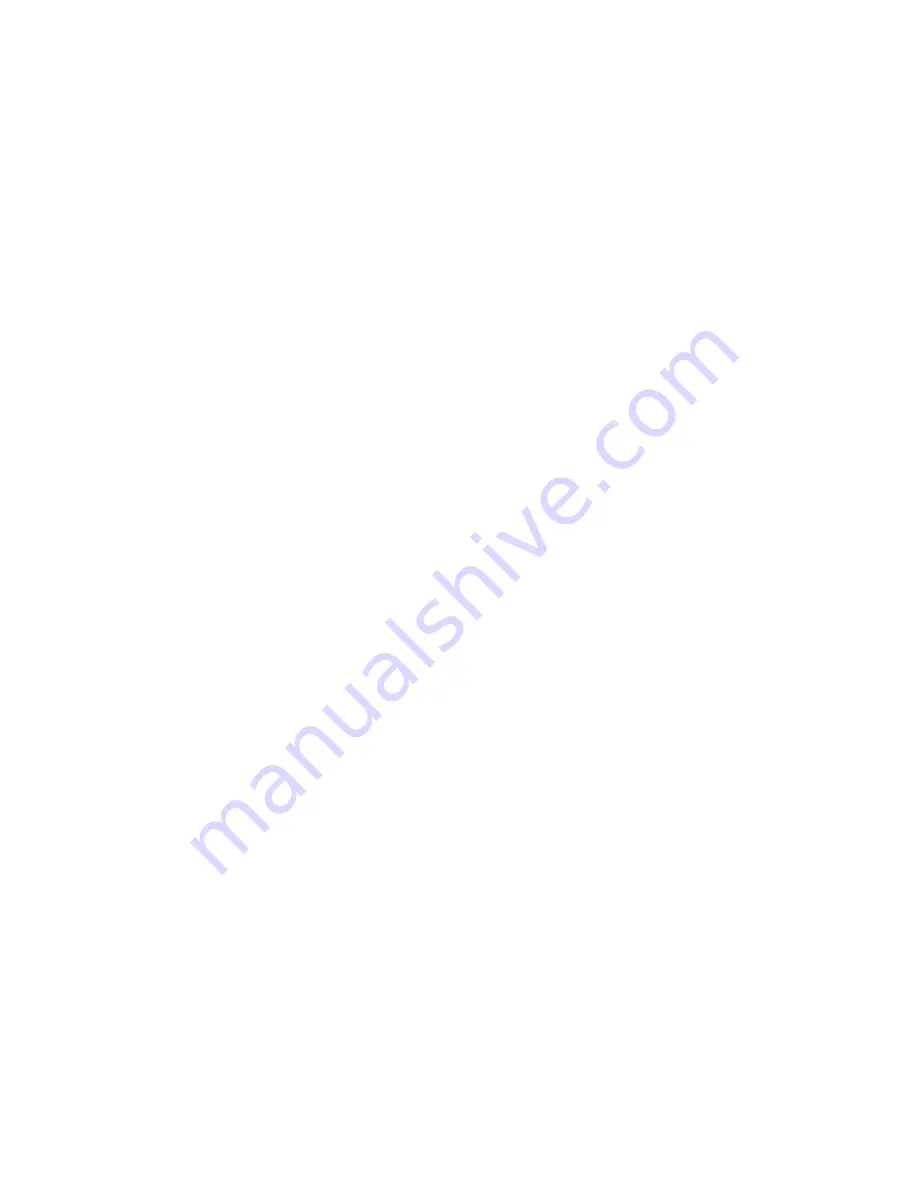
19
5.9 - Control of a boiler
NOTE: The control of the electric heating stages or of a
boiler is not authorised for slave units.
The unit can control the start-up of a boiler, if it is in heating
mode. When the boiler is operating, the unit water pump is
stopped.
The unit and a boiler cannot operate together. In this case the
boiler output is activated in the following conditions:
•
The unit is in heating mode, but a fault prevents the use of
the heat pump capacity.
•
The unit is in heating mode, but works at a very low
outdoor temperature, making the heat pump capacity
insufficient. It is possible to adjust the boiler start-up based
on the outside temperature (HCCONFIG menu).
5.10 - Master/slave assembly
Two control units can be linked to produce a master/slave
assembly. The two machines are interconnected over the CCN
bus. All parameters required for the master/slave function must
be configured through the Service configura-tion menu.
Master/slave operation requires the connection of a tempe-rature
probe at the common manifold on each machine, if the heat
exchanger leaving water temperature is controlled. It is not
required, if the entering water temperature is controlled.
The master/slave assembly can operate with constant or
variable flow. In the case of variable flow each machine must
control its own water pump and automatically shut down the
pump, if the cooling capacity is zero.
For constant flow operation the pumps for each unit are
continuously operating, if the system is operating. The master
unit can control a common pump that will be activated, when
the system is started. In this case the slave unit pump is not
used.
All control commands to the master/slave assembly (start/stop,
setpoint, heating/cooling operation, load shedding, etc.) are
handled by the unit which is configured as the master, and must
therefore only be applied to the master unit. They will be
transmitted automatically to the slave unit.
The master unit can be controlled locally, remotely or by CCN
com-mands. Therefore to start up the assembly, simply validate
the Master operating type (Master) on the master unit. If the
Master has been configured for remote control then use the
remote volt-free contacts for unit start/stop.
The slave unit must stay in CCN operating type continuously. To
stop the master/slave assembly, select Local Off on the master
unit or use the remote volt-free contacts if the unit has been
configured for remote control.
One of the functions of the master unit (depending on its
configuration) may be the designation, whether the master or
slave is to be the lead machine or the follower. The roles of
lead machine and follower will be reversed when the difference
in running hours between the two units exceeds a configurable
value, ensuring that the running times of the two units are
automatically equalised.
The changeover between lead machine and follower may take
place when the assembly is started up, or even whilst running.
The running time balancing function is not active if it has not
been configured: in this case the lead machine is always the
master unit.
The lead machine will always be started first. When the lead
machine is at its full available capacity, start-up delay
(configurable) is initialised on the follower. When this delay has
expired, and if the error on the control point is greater than
1.7°C, the follower unit is authorised to start and the pump is
activated. The follower will automatically use the master unit
active setpoint. The lead machine will be held at its full available
capacity for as long as the active capacity on the follower is not
zero. When the follower unit receives a command to stop, its
evaporator water pump is turned off with 20 seconds delay.
In the event of a communication fault between the two units,
each shall return to an autonomous operating mode until the
fault is cleared. If the master unit is halted due to an alarm, the
slave unit is authorised to start without prior conditions.
ATTENTION: For heat pumps operating in master/slave
mode and using an NRCP2 board or equipped with electric
heater stages control must be on the entering water
temperature.
5.11 - Heating module (HDC) control
61WG units are specially designed to optimise the operation of
heating installations that require hot-water production for
traditional heating and domestic hot water (DHW)
requirements.
In this case an AUX board is included in the unit control box.
The BW10 control system includes algorithms that permit
constant and automatic optimisation:
•
control of a three-way directional on/off valve based on
the heating or domestic hot water requirements
•
control of the electric heater stages can complement the
heating loop
•
hot water setpoint reset (heating application) based on the
outside air temperature
•
priority control between heating and domestic hot water
applications.
5.11.1 – Sensor
An optional outside air temperatrure sensor can be used to reset
the setpoint or determine the summer/winter mode.
Summary of Contents for BW10 020-090
Page 1: ...BW10 020 090 Control Operation instructions VMGFU102...
Page 23: ...23...
Page 24: ...VMGFU102...