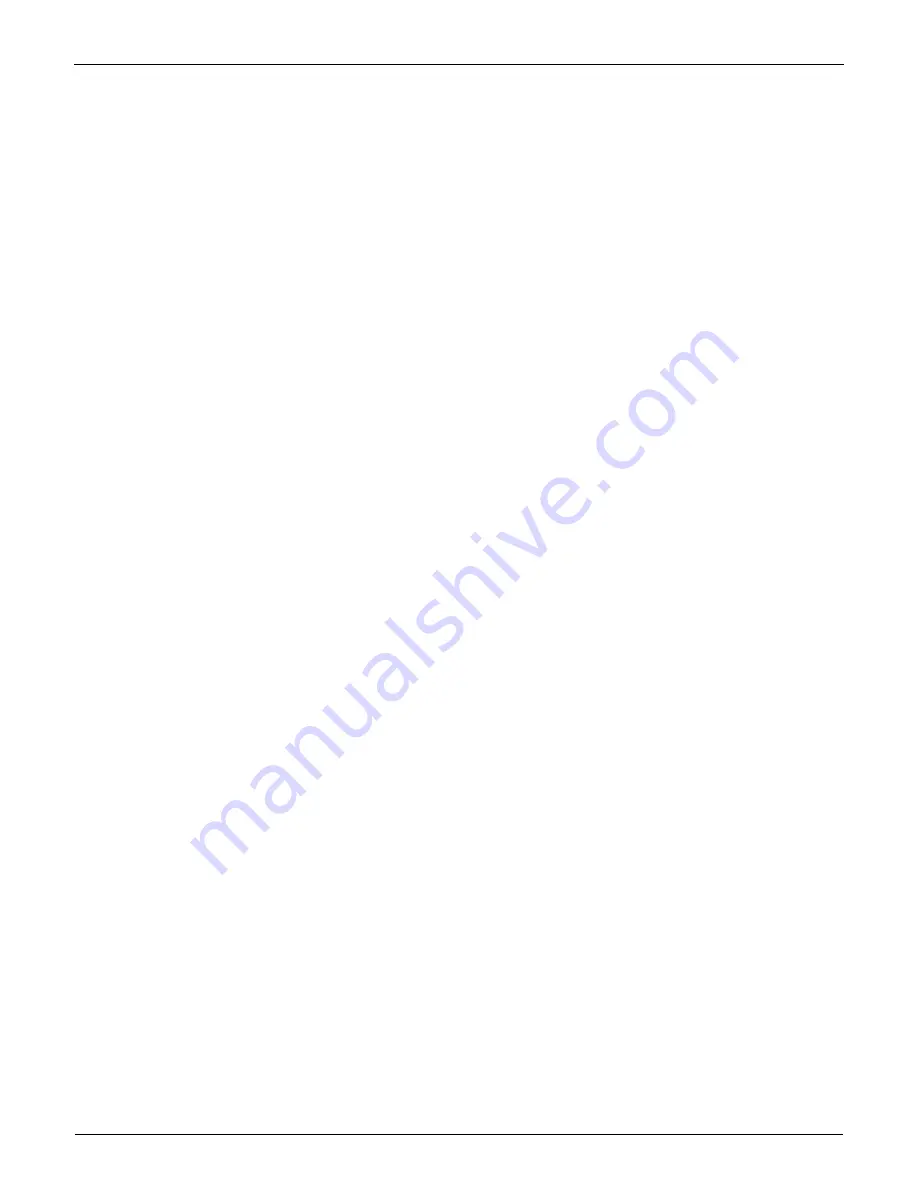
SiUS041111
4
Specifications
Part 2
Specifications
1. Specifications .............................................................................................. 5
1.1
Cooling Only................................................................................................. 5
1.2
Heat Pump ................................................................................................... 8