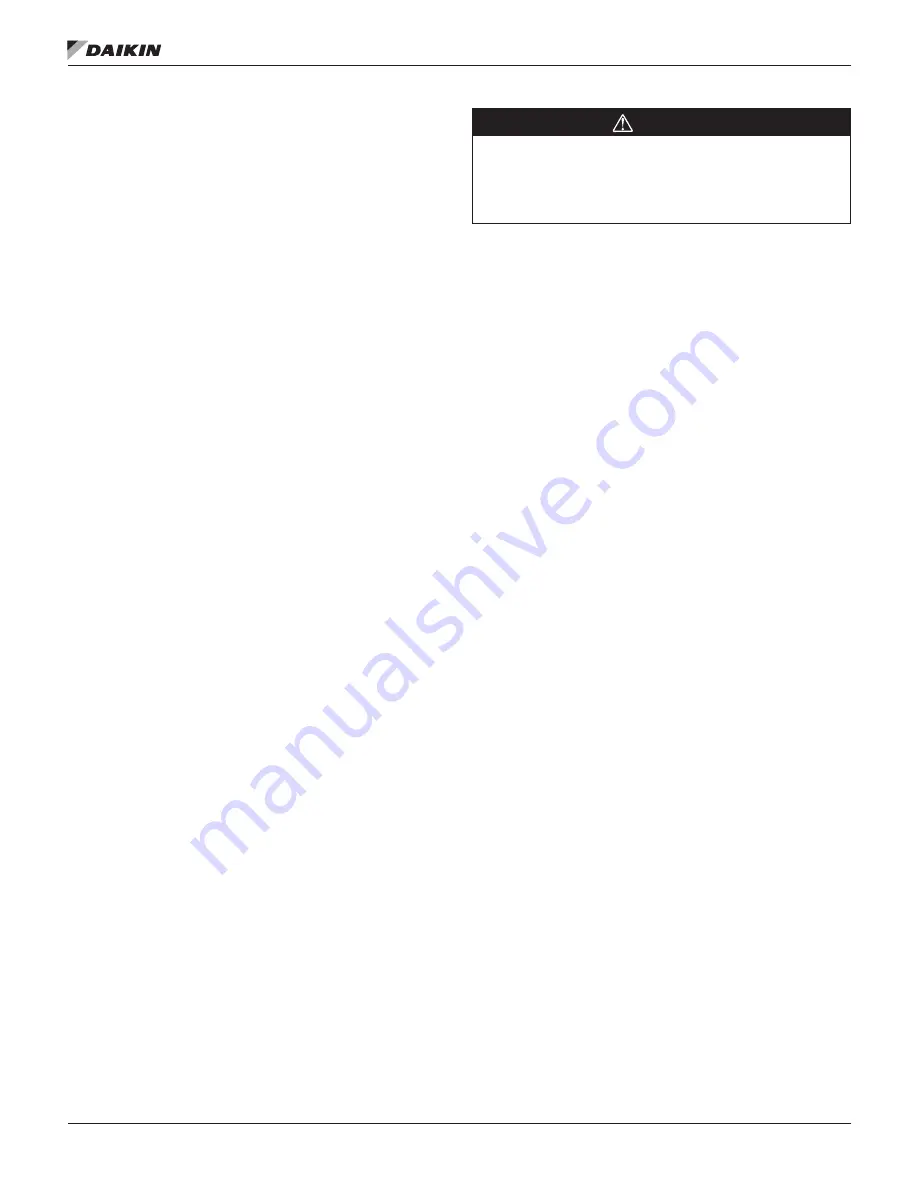
Unit(s) Surrounded by Solid Walls:
1 .
If there are walls on one or two adjacent sides of the unit,
the walls may be any height. If there are walls on more
than two adjacent sides of the unit, the walls should not
be higher than the unit.
2 .
The distance between the unit and the wall should be at
least 96" (2438 mm) on all sides of the unit.
3 .
The distance between any two units within the walls
should be at least 120" (3048 mm).
Do not locate outside air intakes near sources of contaminated air.
If the unit is installed where windy conditions are common,
install wind screens around the unit, maintaining the
clearances specified (see
). This is particularly
important to maintain adequate head pressure control when
mechanical cooling is required at low outdoor air temperatures.
Overhead Clearance
1 .
Unit(s) surrounded by screens or solid walls must have
no overhead obstructions over any part of the unit. For
heat pump models overhead obstructions could allow the
formation of dangerous ice cycles.
2 .
The area above the condenser must be unobstructed in
all installations to allow vertical air discharge.
3 .
The following restrictions must be observed for overhead
obstructions above the air handler section:
a .
There must be no overhead obstructions above the
furnace flue, or within 9" (229 mm) of the flue box.
b .
Overhead obstructions must be no less than 96"
(2438 mm) above the top of the unit.
c. There must be no overhead obstructions in the areas
above the outside air and exhaust dampers that are
farther than 24" (610 mm) from the side of the unit.
Roof Curb Assembly and Installation
Locate the roof curb and unit on a portion of the roof that can
support the weight of the unit. The unit must be supported to
prevent bending or twisting of the machine.
If building construction allows sound and vibration into
the occupied space, locate the unit over a non-critical
area . It is the responsibility of the system designer to
make adequate provisions for noise and vibration in the
occupied space .
Install the curb and unit level to allow the condensate drain to
flow properly and allow service access doors to open and close
without binding.
The gasketed top surface of the curb seals against the unit
when it is set on the curb. These flanges must not support
the total weight of the duct work. See
for details on duct connections. It is critical that
the condensate drain side of the unit be no higher than the
opposite side .
Assembly Instructions
Assembly of a typical roof curb is shown in
.
1 .
Set curbing parts A thru G per dimensions shown over
roof opening or on a level surface. Note location of
supply air opening. Check alignment of all mating screw
holes.
2 .
Screw curbing parts together using fasteners provided.
Leave all screws loose until curb is checked to be
square .
3 .
Square entire curbing assembly and securely tighten all
screws.
4 .
Position curb assembly over roof openings. Curb must
be level within .25 inches from side to side and 1.50
inches over its length. Check that top surface of curb is
flat with no bowing or sagging.
5 .
Weld curb assembly in place. Caulk all seams watertight.
Remove backing from .25 x 1.50 wide gasket and apply
to surfaces shown by crosshatching.
6 .
Check that electrical connections are coordinated.
WARNING
Mold can cause personal injury .
Some materials such
as gypsum wall board can promote mold growth when
damp. Such materials must be protected from moisture
that can enter units during maintenance or normal
operation .
M
eChanICal
I
nsTallaTIon
www.DaikinApplied.com
5
IM 1125-6 • REBEL ROOFTOPS
DOT-ITB-21-8041-AC
FPID: 437300-3-7B-01