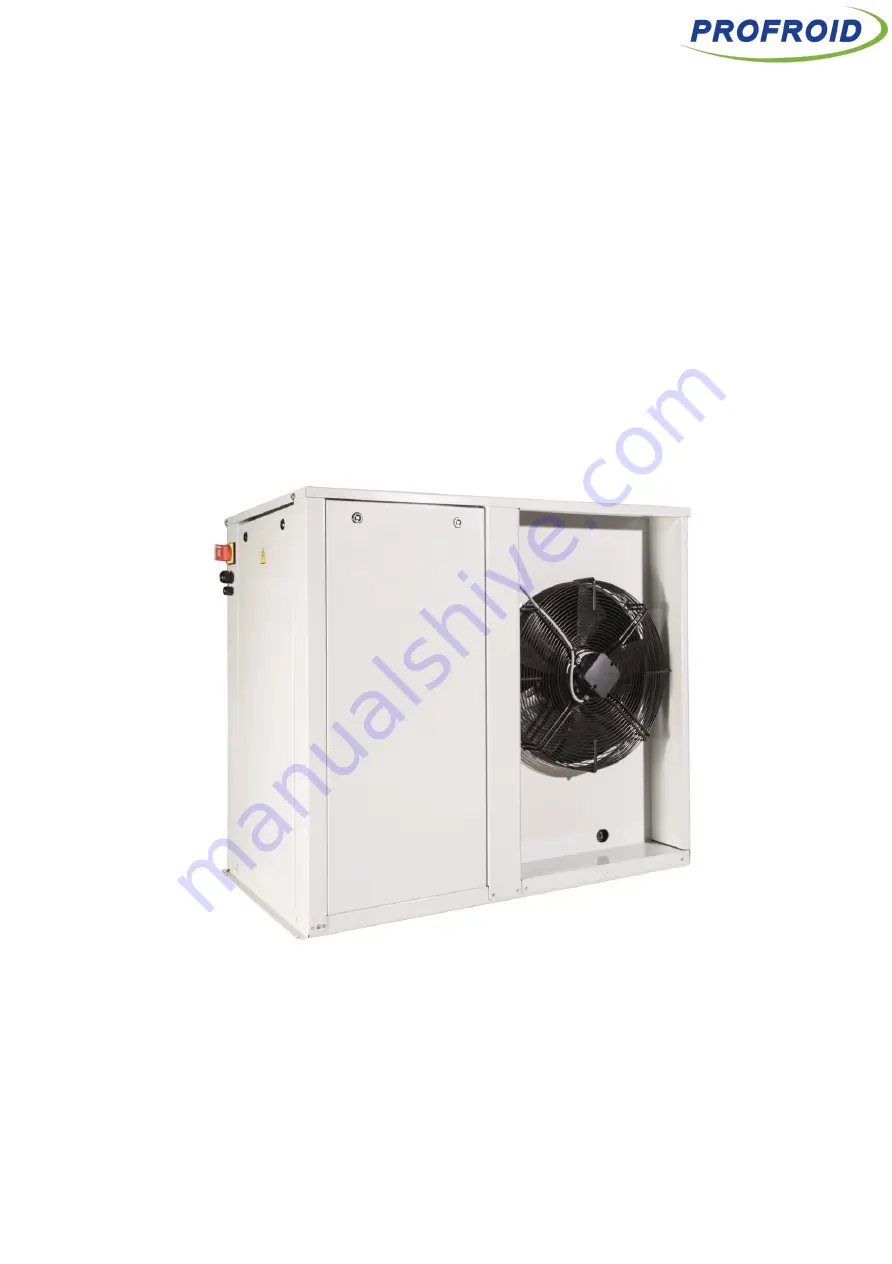
OPERATING INSTRUCTIONS
COMMISSIONING / OPERATING / MAINTENANCE
(must be given to the end user in order to complete the operating manual during the equipment service life)
QUIETCO
2
OL
/ PED fluid group : 2
These operating instructions must be read at the delivery of the equipment and prior any operation on it.
Our technical department is at your disposal for any additional information (Tel : + 33 4 42 18 05 00).
This document is a translation of the French original version which prevails in all cases.
Version 9110
Summary of Contents for QC LT
Page 24: ...REFRIGERANT CIRCUIT DIAGRAM 21 QUIETCO2OL AIR COOLED MT Version LT Version ...
Page 25: ...REFRIGERANT CIRCUIT DIAGRAM 22 QUIETCO2OL WATER COOLED VERSION MT Version LT Version ...
Page 30: ...USER INTERFACE 27 Navigation To navigate inside the menu tree use the following buttons ...
Page 36: ......
Page 43: ...APPENDIX 1 REFRIGERANT AND OIL CHARGE AIR COOLED VERSION 39 ...
Page 44: ...APPENDIX 1 REFRIGERANT AND OIL CHARGE AIR COOLED VERSION 40 ...