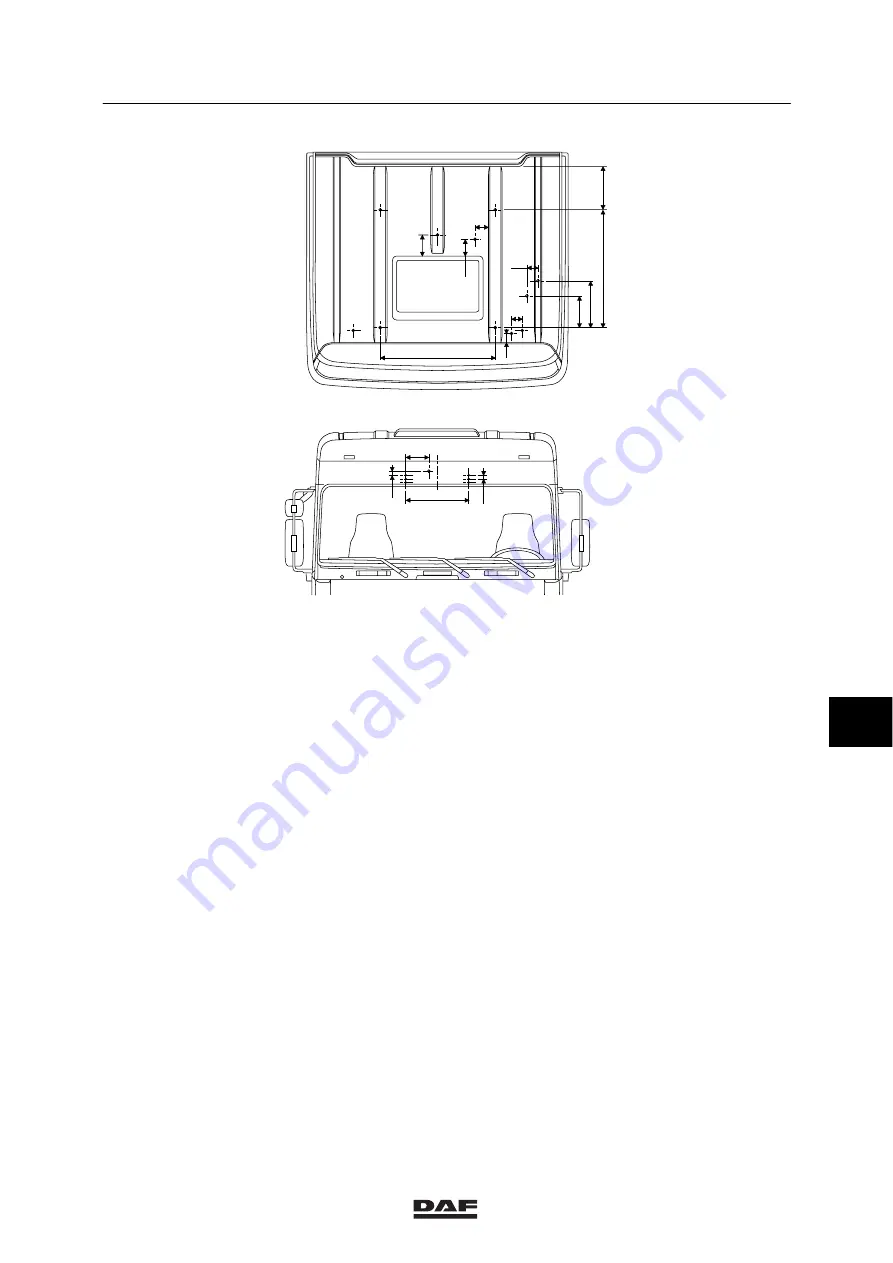
1
95
XF
series
Inspection and adjustment
ACCESSORIES
2-3
448
90
40
32,5
593
1120
430
105
100
140
160
200
1110
220
600
A
G
H
A
A
E
D
B F
C
C
A
K100475
XH CAB
Legend
A.
Roof spoiler
B.
Cable duct for rotating light
*
C.
Hose duct for air horn
*
D.
Cable duct for satellite aerial
E.
Mounting position for mobile phone aerial
F.
Radio aerial (standard)
G.
Cable duct for CB aerial
H.
Cable duct for roof spotlights
*
*
Reverse for RHD models
8
ᓻ
0209
Summary of Contents for 95XF
Page 2: ......
Page 4: ...1 TECHNICAL DATA Contents 95XF series 2 ᓻ 200345 0 ...
Page 22: ...1 TECHNICAL DATA Internal and external cab components 95XF series 1 18 0 ᓻ 200345 ...
Page 26: ...1 TECHNICAL DATA Cab suspension 95XF series 2 4 0 ᓻ 200345 ...
Page 28: ...1 TECHNICAL DATA Cab tilting gear 95XF series 3 2 0 ᓻ 200345 ...
Page 30: ...1 TECHNICAL DATA Seats 95XF series 4 2 0 ᓻ 200345 ...
Page 32: ...1 TECHNICAL DATA Accessories 95XF series 5 2 0 ᓻ 200345 ...
Page 34: ...1 DIAGNOSTICS Contents 95XF series 2 1 ᓻ 0209 ...
Page 36: ...1 DIAGNOSTICS Cab heating 95XF series 1 2 1 ᓻ 0209 ...
Page 40: ...1 DIAGNOSTICS Cab suspension 95XF series 2 4 1 ᓻ 0209 ...
Page 44: ...1 INTERNAL CAB COMPONENTS Contents 95XF series 2 2 ᓻ 0209 ...
Page 46: ...1 INTERNAL CAB COMPONENTS Safety instructions 95XF series 1 2 2 ᓻ 0209 ...
Page 90: ...1 INTERNAL CAB COMPONENTS Removal and installation 95XF series 4 34 2 ᓻ 0209 ...
Page 92: ...1 CAB HEATING Contents 95XF series 2 3 ᓻ 0209 ...
Page 94: ...1 CAB HEATING Safety instructions 95XF series 1 2 3 ᓻ 0209 ...
Page 112: ...1 CAB HEATING Removal and installation 95XF series 4 14 3 ᓻ 0209 ...
Page 114: ...1 EXTERNAL CAB COMPONENTS Contents 95XF series 2 ᓻ 200345 4 ...
Page 116: ...1 EXTERNAL CAB COMPONENTS Safety instructions 95XF series 1 2 4 ᓻ 200345 ...
Page 120: ...1 EXTERNAL CAB COMPONENTS General 95XF series 2 4 4 ᓻ 200345 ...
Page 178: ...1 EXTERNAL CAB COMPONENTS Removal and installation 95XF series 4 52 4 ᓻ 200345 ...
Page 180: ...1 CAB SUSPENSION Contents 95XF series 2 5 ᓻ 0209 ...
Page 210: ...1 CAB SUSPENSION Removal and installation 95XF series 4 18 5 ᓻ 0209 ...
Page 212: ...1 CAB TILTING MECHANISM Contents 95XF series 2 6 ᓻ 0209 ...
Page 220: ...1 CAB TILTING MECHANISM General 95XF series 2 6 6 ᓻ 0209 ...
Page 224: ...1 CAB TILTING MECHANISM Inspection and adjustment 95XF series 3 4 6 ᓻ 0209 ...
Page 234: ...1 CAB TILTING MECHANISM Removal and installation 95XF series 4 10 6 ᓻ 0209 ...
Page 244: ...1 SEATS Contents 95XF series 2 7 ᓻ 0209 ...
Page 246: ...1 SEATS Safety instructions 95XF series 1 2 7 ᓻ 0209 ...
Page 258: ...1 SEATS General 95XF series 2 12 7 ᓻ 0209 ...
Page 260: ...1 SEATS Inspection and adjustment 95XF series 3 2 7 ᓻ 0209 ...
Page 288: ...1 ACCESSORIES Contents 95XF series 2 8 ᓻ 0209 ...
Page 290: ...1 ACCESSORIES Safety instructions 95XF series 1 2 8 ᓻ 0209 ...
Page 294: ...1 ACCESSORIES Inspection and adjustment 95XF series 2 4 8 ᓻ 0209 ...
Page 302: ...1 ACCESSORIES Removal and installation 95XF series 3 8 8 ᓻ 0209 ...
Page 304: ...1 PREWAX TREATMENT Contents 95XF series 2 10 ᓻ 0209 ...
Page 306: ...1 PREWAX TREATMENT Safety instructions 95XF series 1 2 10 ᓻ 0209 ...