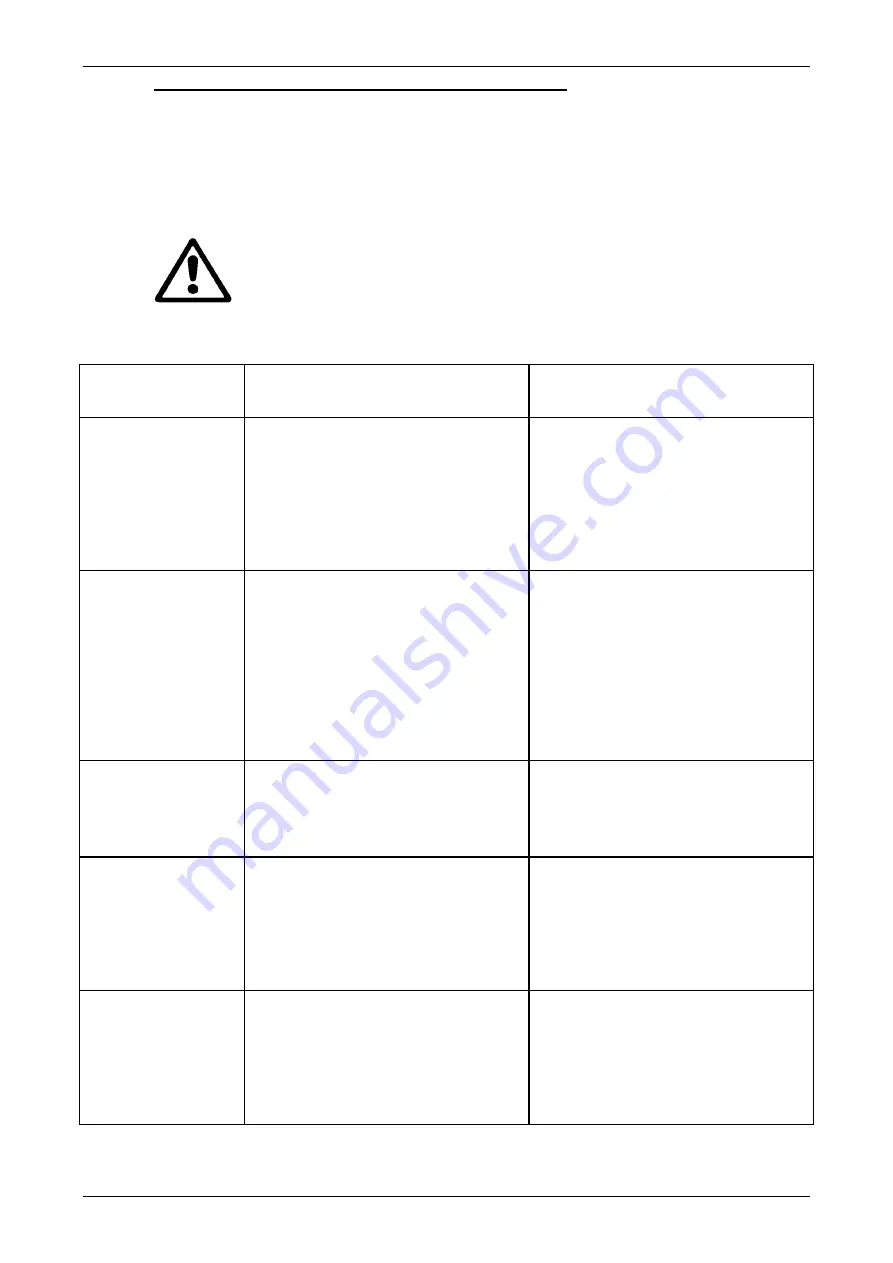
ENGLISH
28
Procedure for greasing the IP55 version (MEC 160-180):
in pumps produced with degree of
motor protection IP55 and in which the bearings greasing system is provided, the grease discharge
hole is closed by a brass cap M10x1 situated at an angle of 90° to the grease nipple. Unscrew and
remove the cap M10x1, apply grease to the grease nipple using a suitable grease pump, continuing
until clean grease comes out of the discharge hole. Switch on the pump and let it run for about an
hour so as to bring the bearing(s) to running heat and thus enable the excess grease to flow out.
Screw the cap M1x1 back in place.
13.
MODIFICATIONS AND SPARE PARTS
Any modification not authorized beforehand relieves the manufacturer of all
responsibility.
All the spare parts used in repairs must be original ones and the
accessories must be approved by the manufacturer so as to be able to guarantee
maximum safety of the machines and systems in which they may be fitted.
14. TROUBLESHOOTING
FAULT
CHECK (possible cause)
REMEDY
1. The motor does not
start and makes no
noise
A. Check the protection fuses.
B. Check the electric connections.
C. Check that the motor is live.
D.
The motor protector may have tripped
due to exceeding the maximum
temperature limit (single-phase
version).
A. If they are burnt-out, change them.
⇒
If the fault is repeated immediately
this means that the motor is short
circuiting.
D.
Wait for automatic reset of the motor
protector once the temperature has
fallen below the maximum limit
.
2. The motor does not
start but makes
noise.
A.
Ensure that the mains voltage
corresponds to the voltage on the data
plate.
B. Check that the connections have been
made correctly.
C. Check that all the phases are present
on the terminal board.
D.
The shaft is blocked. Look for
possible obstructions in the pump or
motor.
B. Correct any errors.
C. If not, restore the missing phase.
D. Remove any obstructions.
3. The motor turns
with difficulty.
A. Check the supply voltage which may
be insufficient.
B. Check whether any moving parts are
scraping against fixed parts.
C. Check the state of the bearings.
B. Eliminate the cause of the scraping.
C. Change any worn bearings.
4. The
(external)
motor protection
trips immediately
after starting.
A. Check that all the phases are present
on the terminal board.
B. Look for possible open or dirty
contacts in the protection.
C. Look for possible faulty insulation of
the motor, checking the phase
resistance and insulation to earth.
A. If not, restore the missing phase.
B. Change or clean the component
concerned.
C. Change the motor casing with the
stator or reset any cables discharging
to earth.
5. The
motor
protection trips too
frequently.
A.
Ensure that the environment
temperature is not too high.
B.
Check the calibration of the
protection.
C. Check the motor rotation speed.
D. Check the state of the bearings.
A. Provide suitable ventilation in the
environment where the pump is
installed.
B. Calibrate at a current value suitable
for the motor absorption at full load.
C. Consult the motor data plate.
D. Change any worn bearings.
Summary of Contents for KV 10/2
Page 2: ......
Page 101: ...96 ...
Page 102: ...97 ...
Page 103: ...98 ...
Page 104: ...99 ...
Page 107: ...102 KV 6 7 M KV 10 4 M KV 10 5 M KV 3 7 T KV 3 10 T KV 6 7 T KV 10 4 T KV 10 5 T ...
Page 108: ...103 KV 32 2 T KV 32 3 T KV 32 4 T KV 32 5 T KV 32 6 T KV 32 7 T KV 32 8 T ...
Page 109: ...104 KV 40 2 T KV 40 3 T KV 40 4 T KV 40 5 T KV 40 6 T KV 40 7 T KV 40 8 T ...
Page 110: ...105 KV 50 2 T KV 50 3 T KV 50 4 T KV 50 5 T KV 50 6 T KV 50 7 T KV 50 8 T KV 50 9 T ...
Page 114: ...109 05 07 cod 0013 550 05 ...