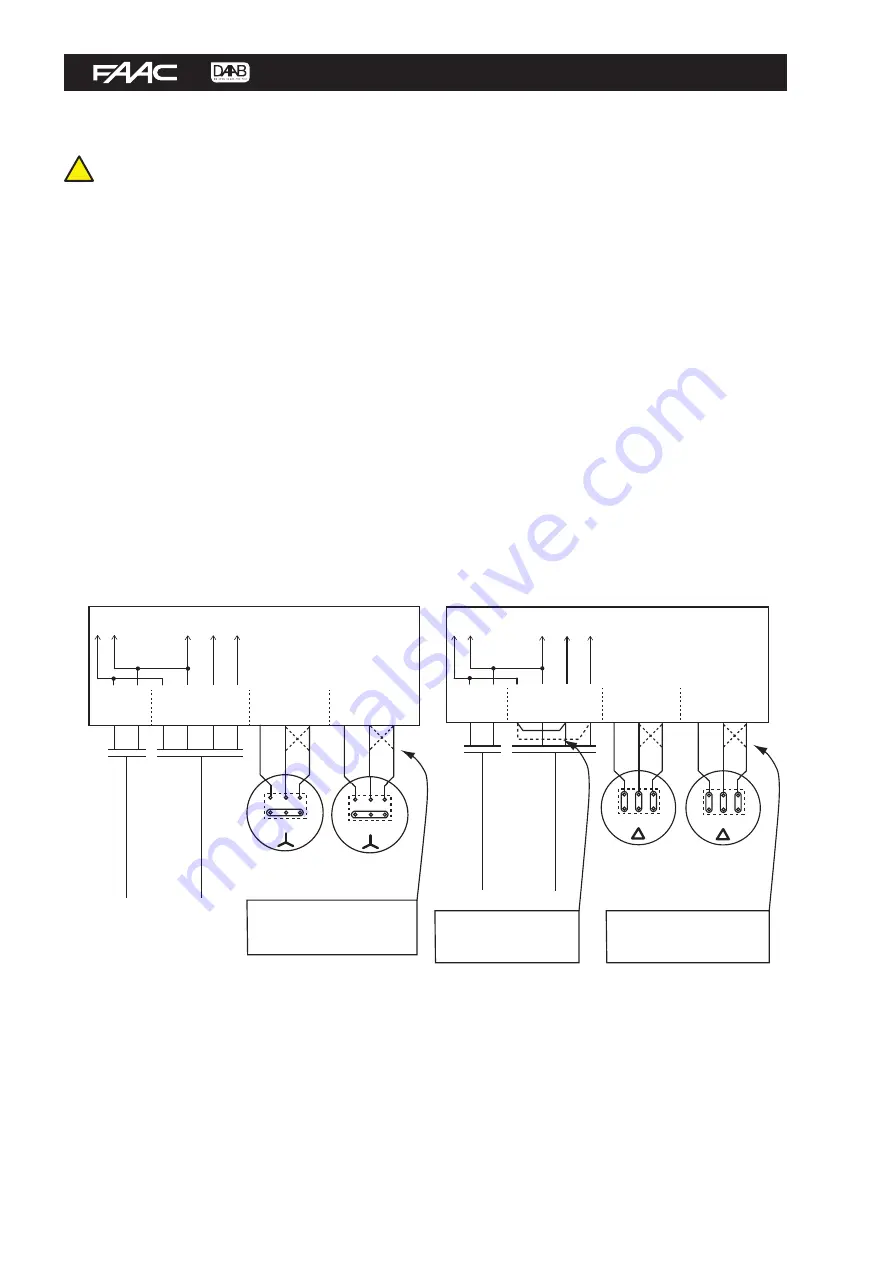
INSTRUCTION MANUAL DAAB AUTOMATIC CONTROLL UNIT EP104 4.08
12
Instruction manual edition 1 for EP104 version 4.08
Connections
• Safety
!
The electrical connections may only be made by a qualified electrician, who accepts responsibility for ensuring that the
electric connections have been carried out in accordance with the applicable standards and this instruction manual.
Always disconnect the power supply when connecting the control box.
Mechanical installation of the control unit must be carried out by persons with the necessary knowledge for the task.
• Installation
The location of the control unit must be selected with regard to the protection class of the enclosure, at least IP54. A
heating and/or cooling element should be included if necessary to maintain the operating temperature stated in the technical
specification.
The control unit must be securely fixed to a wall or a bracket intended for this purpose, using screw joints. The fixing holes
are on the rear or underside of the enclosure.
Cables into and out of the enclosure must have cable entry seals that are approved for use with the particular cable. Cables
outside the enclosure must be securely fixed to the surrounding structure. They must not hang loose and there must be no
possibility of them catching on passing objects.
• High current
The power supply must be connected via a lockable main switch, and have T10A protection.
Connect the incoming earth to the earth bar.
Check that the power supply and motor voltage are compatible.
Motors
The largest motor that can be connected is 1.5 kW (3-phase 3x400 V).
See "Commissioning" for details of how to check the direction of rotation.
Connecting motors to the EP104
Supply 3x400V with neutral
N T1 N L1 L2 L3 U1 V1 W1
U2 V2 W2
O
ut
let
230V
3x400V
+
N
Fus
e max T10A
U1
V1
W1
W2
U2
V2
U1
V1
W1
W2
U2
V2
Supply to control board
Supply motors
EP104
In/Out
Power
Motor 1
Motor 2
Switch V1 and W1 and/
or V2 and W2 if the motor
runs in the wrong direction.
3-phase motor
Y-connected
3-phase motor
Y-connected
Supply 3x230V without neutral
O
ut
let
230V
3x230V
Fus
e max T
10A
U1
V1
W1
W2
U2
V2
U1
V1
W1
W2
U2
V2
N T1 N L1 L2 L3 U1 V1 W1
U2 V2 W2
EP104
In/Out
Power
Motor 1
Motor 2
Supply to control board
Supply to motors
3-phase motor
D-connected
3-phase motor
D-connected
Change of phase
sequence if the load
guard value shows fault.
Switch V1 and W1 and/
or V2 and W2 if the motor
runs in the wrong direction.
Summary of Contents for EP104
Page 60: ......