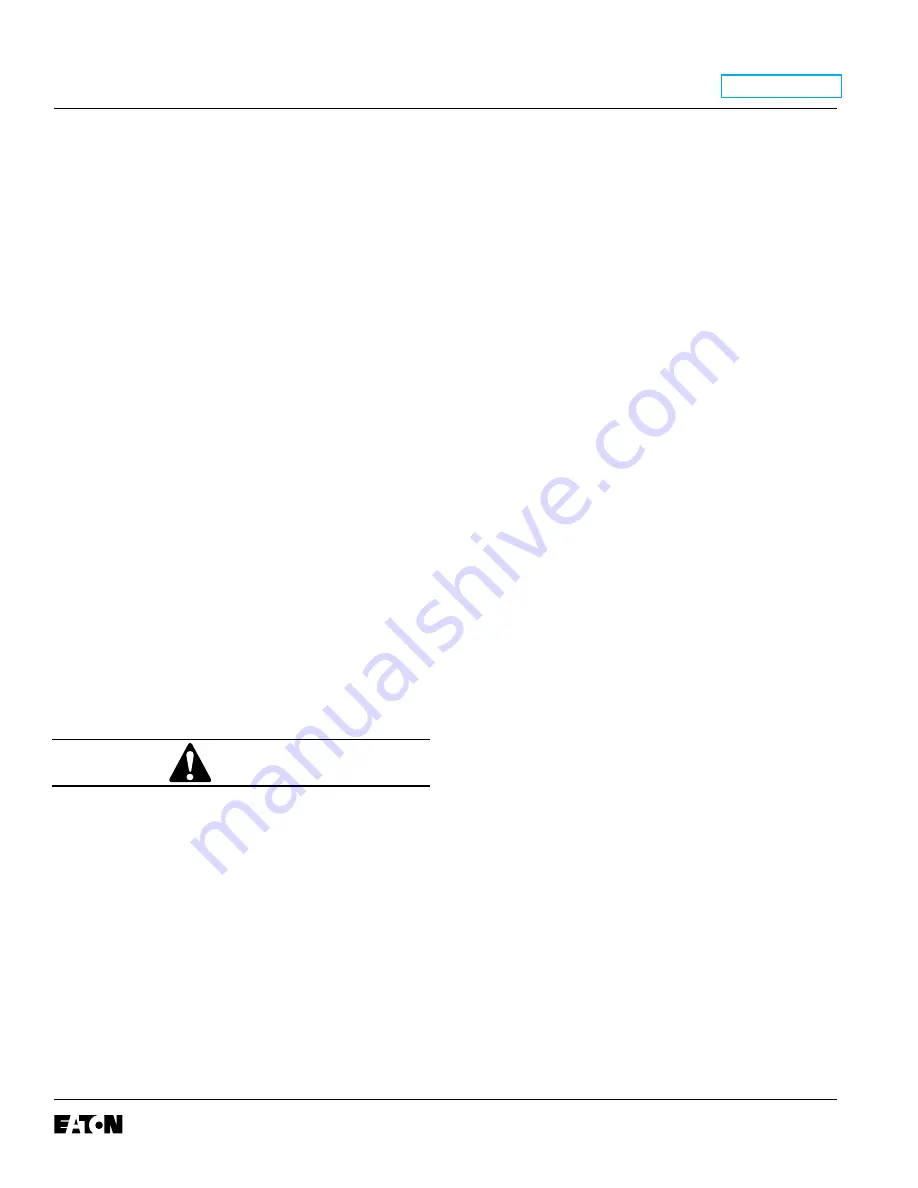
Effective October, 2000
Page 4
Step 1:
General Breaker Preparation
Before attempting to remove the Breaker from the
Cell or perform any Retrofit Operation, be sure
to read and understand the Safety Precautions
section of this manual. In addition, be sure to read
and understand the Instructions for the Application
of Digitrip RMS Retrofit Kits on Power Circuit
Breakers (Retrofit Application Data - Publication
AD 33-855-1), supplied with the Digitrip Retrofit Kit.
NOTE:
For Breakers Utilizing a Remotely
Mounted Neutral Sensor Connected to the
Breaker via Neutral CT Disconnect Only. The
rating of the Neutral CT Disconnect, originally
supplied with the Breaker, does not meet the
specifications / requirements of the Retrofit Kit.
The Neutral CT Disconnect must be removed
and scrapped. The remotely mounted fourth
Sensor must be wired into the system via
Secondary Disconnects.
If the Breaker being Retrofitted is NOT
equipped with Secondary Disconnects, the
Secondary Disconnects for both the Breaker
and the Cell, as well as all mounting brackets
and hardware, must be secured from the
original manufacturer of the Breaker BEFORE
beginning the Retrofit Process.
DO NOT ATTEMPT TO INSTALL OR PERFORM
MAINTENANCE ON EQUIPMENT WHILE IT IS
ENERGIZED. SEVERE PERSONAL INJURY OR
DEATH CAN RESULT FROM CONTACT WITH
ENERGIZED EQUIPMENT. VERIFY THAT NO
VOLTAGE IS PRESENT BEFORE PROCEEDING.
A. Trip the Breaker and remove it from the Cell.
Move the Breaker to a clean, well-lit work
bench.
NOTE: It is the responsibility of the Retrofitter
to insure that the Breaker and all original com-
ponents are in good condition. Visually inspect
all Breaker components for signs of damage or
wear. If any signs of damage or wear are
detected for components not included in the
Retrofit Kit, secure the necessary replacement
parts before beginning the Retrofit Process.
The force necessary to trip the Breaker should
not exceed three (3) lbs.
To begin the Retrofit Process, refer to the compo-
nents list at the end of this manual. Lay out the
components and hardware according to the steps
outlined. The components and hardware will be
used to complete each step in the Retrofit Process.
NOTE: For most photographs contained within
this manual, a G. E. AK-2-50 Breaker was used
as the subject. Depending on the version and
age of the Breaker being Retrofitted, some
components / views depicted in this manual
may differ from the Breaker being Retrofitted.
WARNING
www
. ElectricalPartManuals
. com