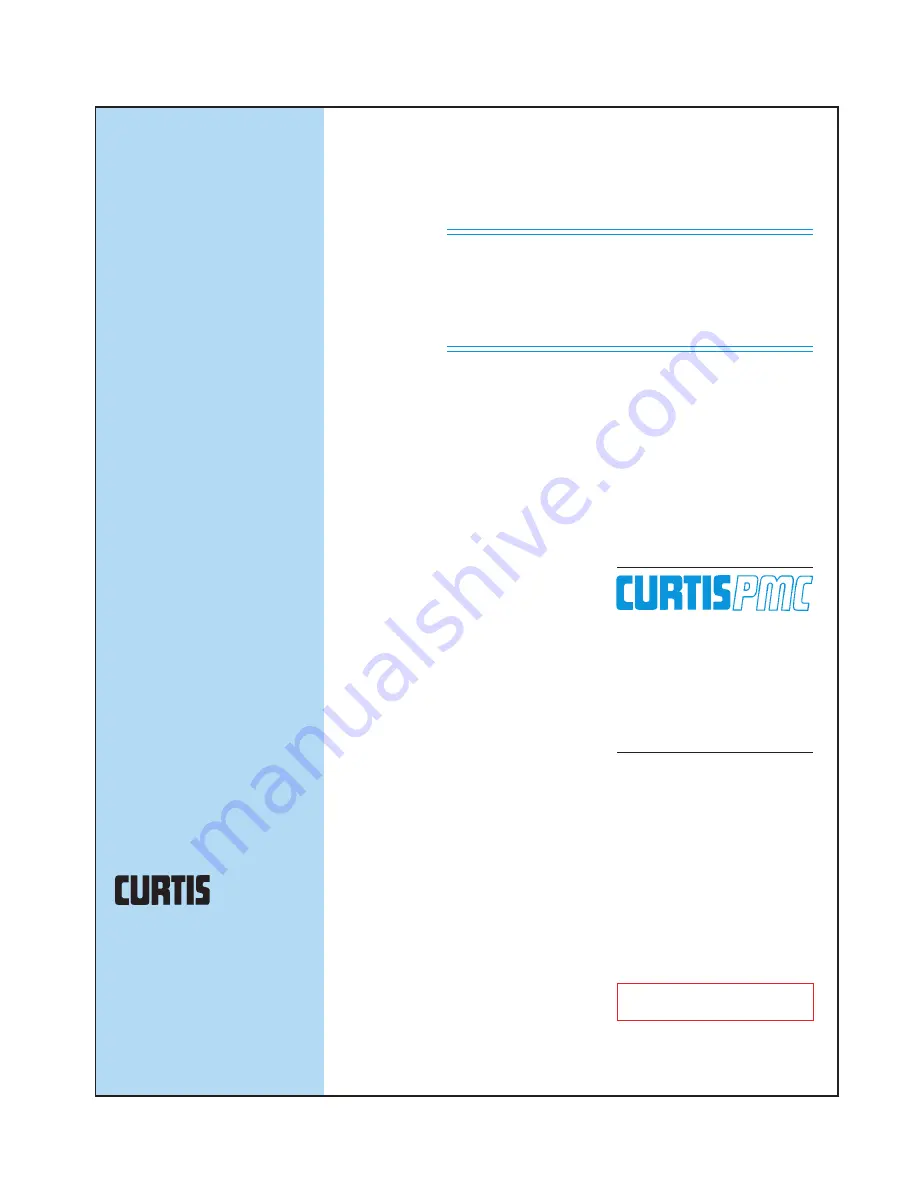
MANUAL
© 2001 CURTIS INSTRUMENTS, INC.
DESIGN OF CURTIS PMC 1200 SERIES
CONTROLLERS PROTECTED BY U.S.
PATENT NO. 4626750.
1 2 9 7
MODEL
INTEGRATED TRACTION
& HYDRAULIC SYSTEM
C O N T R O L L E R
CURTIS PMC
235 East Airway Boulevard
Livermore, California 94550 USA
Tel: 925-961-1088
Fax: 925-961-1099
www.curtisinst.com
1297 Manual, p/n 36411
Rev. A: February 2001