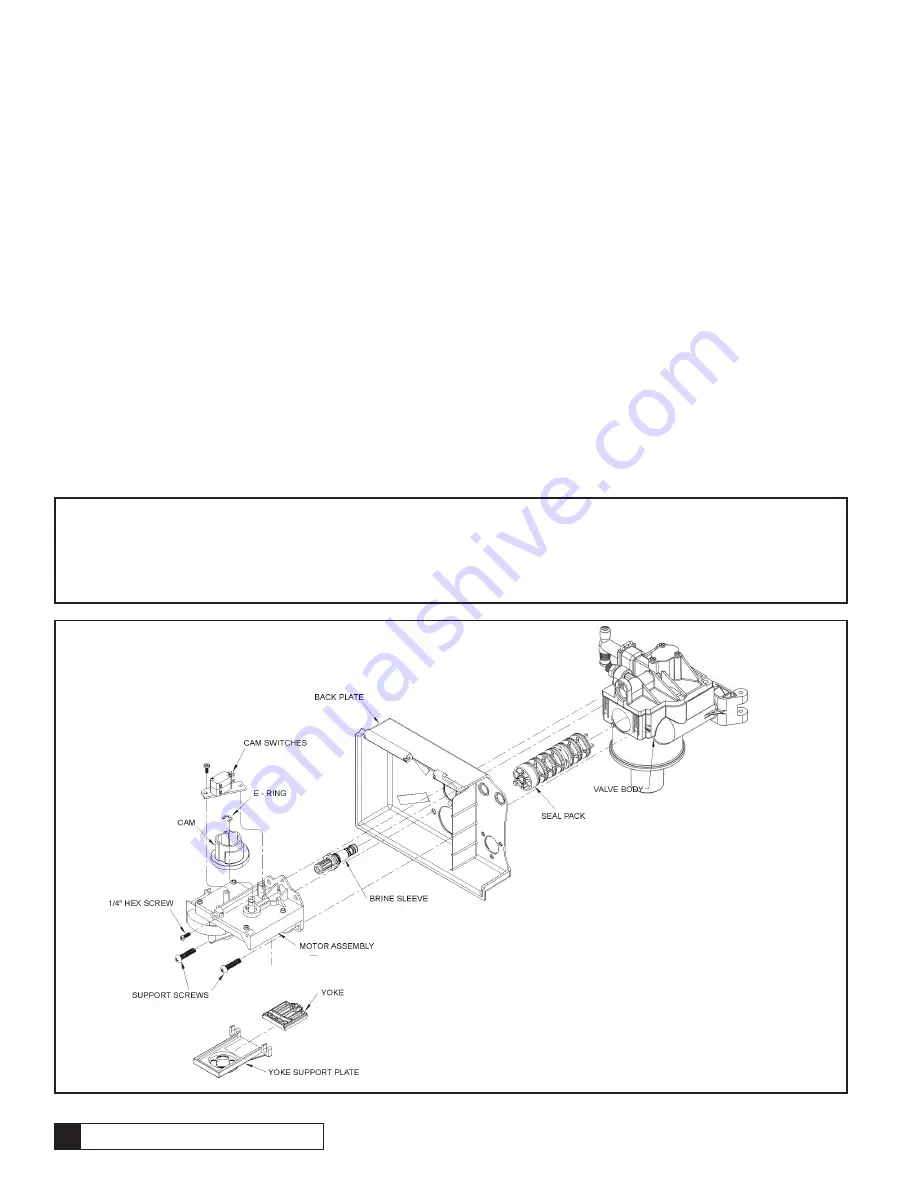
36
Culligan
®
Iron-Cleer
R
Water Filters
Drive Motor Assembly
1. Remove the drive motor cam switches by removing the one screw holding the switches to the motor.
2. Remove the E-ring holding the drive motor cam to the camshaft with a flat tip screwdriver.
3. Lift the cam off the shaft.
4. Remove the screw above the brine sleeve assembly.
5. Loosen the two screws holding the yoke support plate and the motor to the control valve.
6. Remove the yoke support plate and yoke by gently pulling them down.
7. Fully remove the two screws holding the motor to the control. The motor will pull away from the control and the backplate will
hang on the valve body.
This procedure can be followed in the reverse order to reassemble the motor to the control. When reassembling the scotch yoke,
the yoke must slide into the yoke support plate prior to pushing the assembly up into the piston end and follower. Figure 19 shows
proper assembly of the yoke into the support plate.
Note:
The seal pack may need to be repositioned in order for the follower to be inserted into the yoke, using the motor and
backplate to push the seal pack fully into the valve is helpful in aligning the yoke. Make sure that the follower is in the follower slot
on the yoke, and that the end of the piston rod is held in the end of the yoke.
Note:
When attaching the yoke support plate be certain to push up on the plate until the two mounting screws bottom in the
U-shaped channels of the support plate.
Figure 18