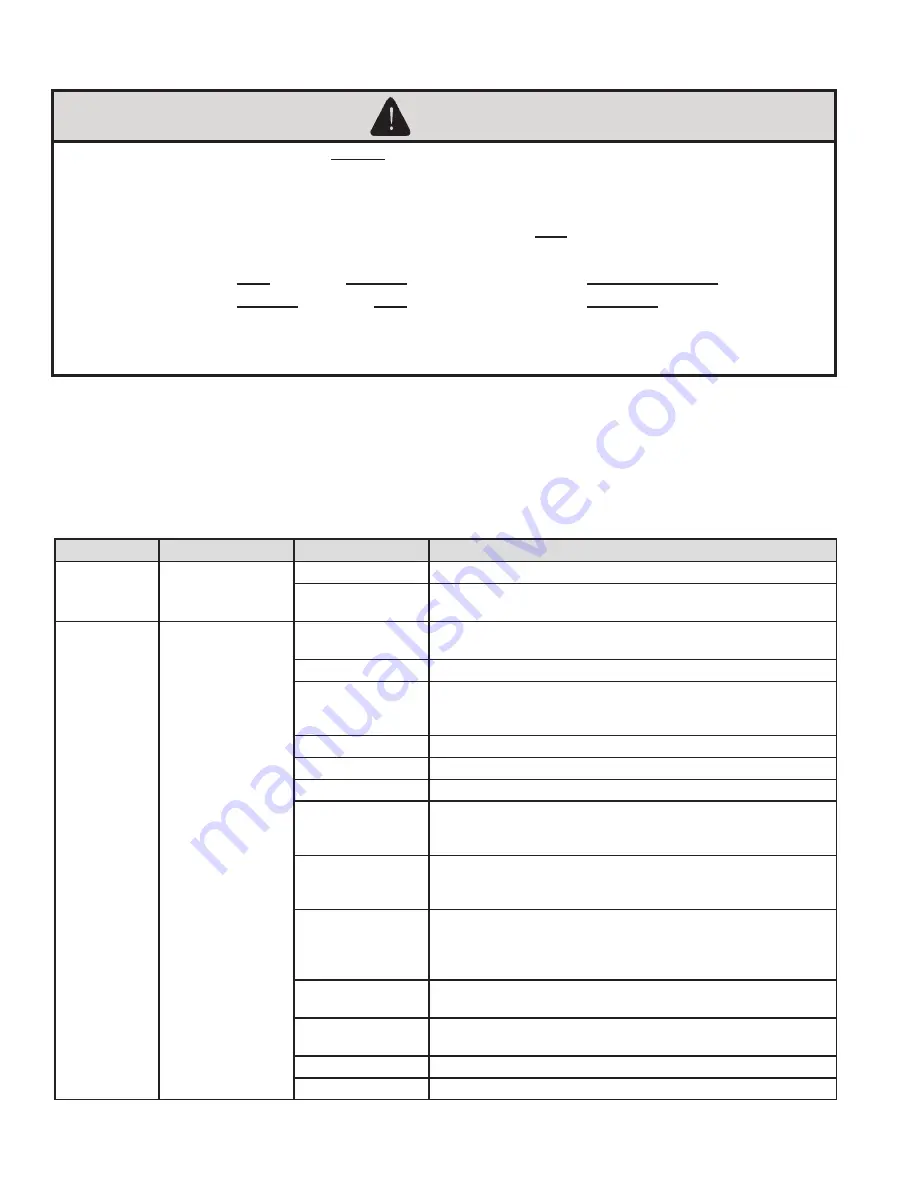
76
IX. System Start-up
(continued)
WARNING
Asphyxiation Hazard. If the throttle is very far out of adjustment on the “rich” (counter-clockwise) side,
the boiler burner may be running at 0% excess air or even with air deficiency. Operating the boiler in this
condition may cause property damage, personal injury or loss of life.
At 0% excess air the CO
2
readings will be either 11.9% CO
2
for natural gas or 13.8% CO
2
for LP gas (O
2
will
be 0%) and CO air free level will be extremely high (well over 1000
PPM
).
If the burner operates with air deficiency, the following phenomena may be observed:
% CO
2
will actually drop (% O
2
will increase) as the throttle is turned counter-clockwise
% CO
2
will actually increase (% O
2
will drop) as the throttle is turned clockwise
If the boiler appears to operate with air deficiency, shut down the boiler and follow instructions in Paragraph
U “Correcting Throttle Screws Mis-Adjustment. Then, use a combustion analyzer to verify and adjust O
2
(or
CO
2
) and CO air free to values shown in Table 35 for natural gas or Table 36 for LP gas.
V. Controls Start-up Check List
Check field wiring and control parameters per below Table 40 and Table 41. The control is factory programmed with default
parameters. Review parameters and adjust as necessary to conform to specific site requirements. From Home Screen, select
ADJUST to access below listed parameters. Login as needed to make changes. For detailed login instructions, refer to
Section X. Operation, Paragraph F “Changing Adjustable Parameters”.
Step
Wiring Location
Parameter
Description
1
120V PCB
120V Line
Is line voltage connected with overcurrent protection?
Boiler, System, and
DHW Pumps
Confirm pumps are connected. If using room air for combustion,
confirm combustion air damper is connected.
2
Low Voltage
Connections PCB
Enable/Disable
Is the space heating thermostat connected. Ensure thermostat is
a “dry”, non-powered input.
DHW Demand
Is an indirect water heater (IWH) providing a heat demand?
Auto Reset and Man
Reset External Limit
Are external limits used? If so, ensure jumper is removed and
limits properly connected. Also check that external limits are
closed and any manual reset devices are reset.
Lockout Alarm
Are alarm contacts connected?
EnviraCOM
Are any EnviraCOM devices used?
Outdoor Sensor
Is an outdoor sensor used? Refer to Steps 1 & 7 in Table 41.
Header Sensor
Is a header sensor used? A header sensor is required for the
master boiler in a multiple boiler installation. Refer to Step 8 in
Table 41 to activate this input.
DHW Sensor
For single boiler servicing indirect water heater (IWH), install
DHW Sensor at boiler-side inlet to IWH. Refer to Step 6 in Table
41 to activate this input.
Remote 4-20mA
Is a 4-20mA input required for: 1) modulation input from an
energy management system, or 2) Central Heat setpoint input
from external multiple boiler control? If yes, refer to Step 11 in
Table 41.
Boiler-to-Boiler
Are multiple boilers connected? If yes, refer to Steps 8 & 9 in
Table 41 to activate boiler-to-boiler communication.
EMS
Is the boiler connected to an energy management system? If yes,
refer to Step 10 in Table 41.
Flow Switch
Is flow switch installed in piping and plugged in?
LWCO
Is a 24V LWCO used? Check installation.
Table 40: Field Wiring Checklist
Summary of Contents for Phantom X series
Page 14: ...14 III Pre Installation and Boiler Mounting G General continued Figure 5 Boiler Stacking...
Page 47: ...47 VI Water Piping and Trim continued Figure 28 Near Boiler Piping Heating Only...
Page 71: ...71 IX System Start up continued Figure 47 Operating Instructions...
Page 122: ...122 XIII Repair Parts continued...
Page 126: ...126 XIII Repair Parts continued...
Page 129: ...129 XIII Repair Parts continued 10A 10B 10C 10D 10G...
Page 134: ...134...
Page 135: ...135...