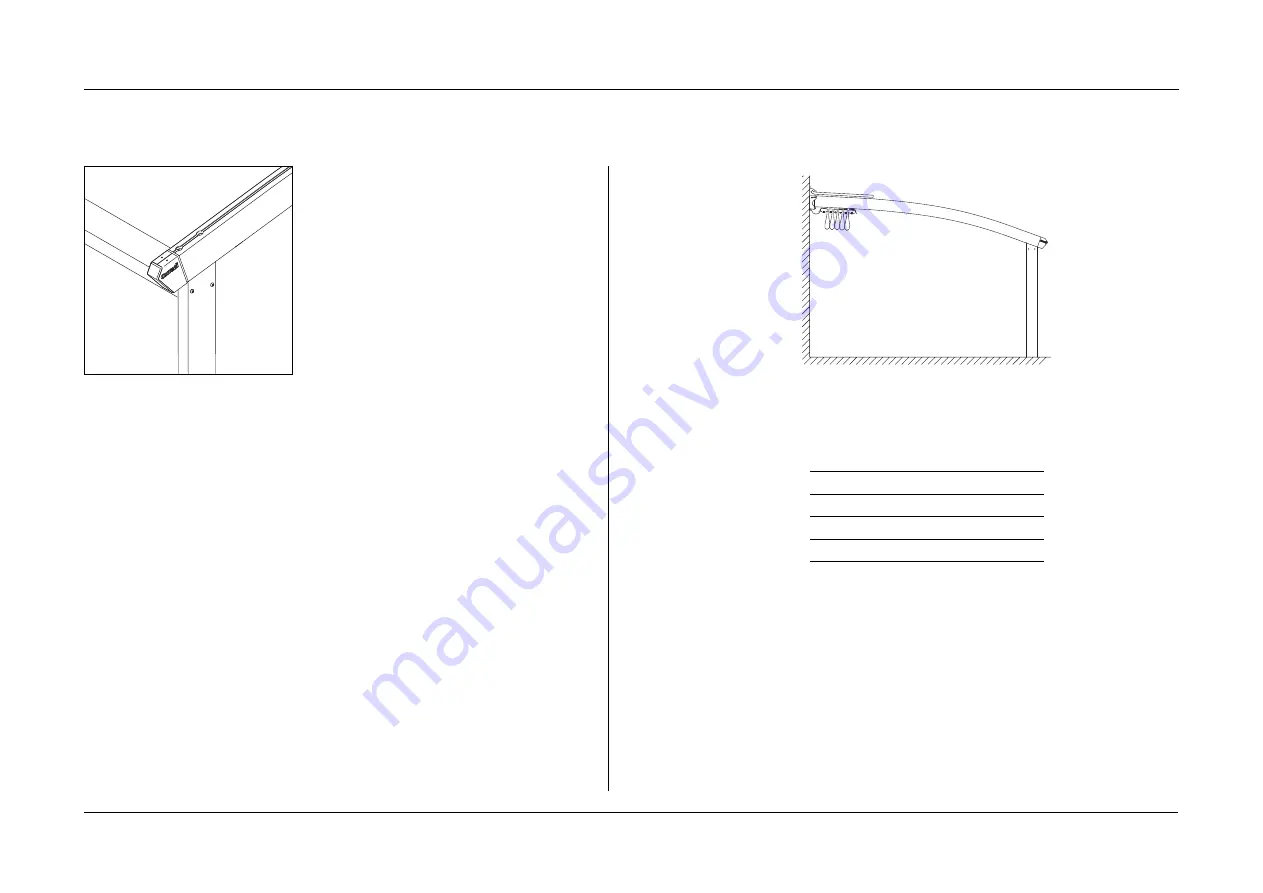
1 - 04.2014
CORRADI SpA - INSTALLATION MANUAL - pERGOTENDA®FLUX
6 di 53
pERGOTENDA® FLUX is a retractable covering
system custom made with curved runners to
protect against sun and rain (not suitable to
support snow), fixed to a supporting wall. It consists
of an aluminium structure and a stacking canvas.
Wind resistance is guaranteed up to class 6 on the
Beaufort scale.
The canvas, made from exclusive Corradi Eclissi*
fabric, available in white, grey and ivory, with
internal concealed obscuration layer and embossed
side with weft effect, is supported by intermediate
tubes (section: 4x5 cm) and terminals (section: 8x5
cm) set parallel to one another approximately every 45 cm.
It slides on runners with built-in splashguard (section 6x12 cm) on sliders with 6 misaligned
wheels with maximum capacity of 450 kg each.
The toothed drive belt inserted in each runner, with strands completely covered to
withstand salinity, is driven by a pulley and a single drive shaft to ensure even canvas
movement. The tensile strength at break of each belt is 894 kg.
The pERGOTENDA® FLUX system is operated by a motor-reducer (electric drive) with the
possibility of radio control.
Aluminium tubular structure 6x12 cm, available in colours: brown, anthracite, white, grey,
ivory in glossy or matt finish; titanium and cor10 with matt finish. Runners available in
colours: brown, anthracite, white, grey, ivory in glossy or matt finish; titanium and cor10 with
matt finish. Support tubes available in colours: white, grey, ivory in glossy or matt finish.
painted with certified Qualicoat cycle epoxy powders. AISI 304 stainless steel accessories and
10/10 aluminium protection covers matching the structure.
* See Corradi sample kit for other fabrics.
FEATURES
MAXIMUM DIMENSIONS cm
Width Projection
2 guides 500 650
3 guides 900 650
4 guides 1300 650