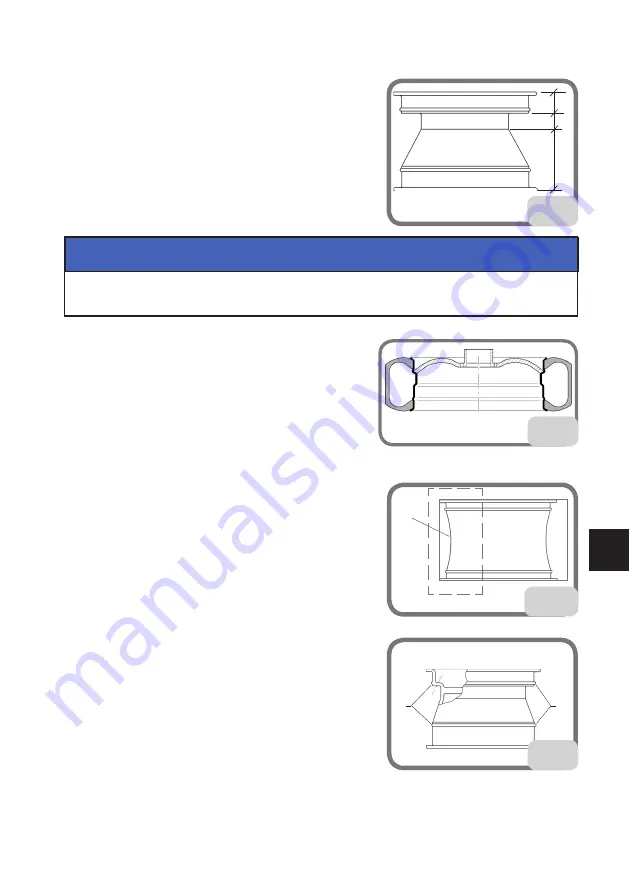
Artiglio Master 28
Operator’s manual
117
EN
6.3. DECIDING FROM WHICH SIDE OF THE WHEEL THE TYRE
MUST BE REMOVED
See Fig.28. Identify the position of channel A on the
rims. Identify the greater width B and the smaller width
C. The tyre must be mounted and demounted with
the wheel on the turntable with the smallest width
side C facing upwards.
See the paragraph “TABLE FOR USING CENTRING AND CLAMPING ACCESSORIES
ACCORDING TO RIM TYPE” in this manual.
CAUTION
When working with “easily deformable” rims (i.e. a
central hole with thin, projecting edges - see Fig. 28A)
we recommend using the universal flange for closed
rims (see the section “TABLE FOR USING CENTRING
AND CLAMPING ACCESSORIES ACCORDING TO
RIM TYPE” in this manual).
SPECIAL WHEELS
Wheels with alloy rims:
some wheels with alloy rims
have a minimum A rim channel or do not have any
channel -
Fig. 28B
. These rims are not approved by
DOT standards (Department of Transportation). The
DOT initials certify that tyres comply with the safety
standards adopted by the United States and Canada
(these wheels cannot be sold in these markets).
High performance wheels (asymmetric curvature) -
Fig. 28C
some European wheels have rims with very
pronounced curvature C, except in the area of the
valve hole A where the curvature is less pronounced
B. On these wheels the bead must first be broken in
correspondence of the valve hole, on both the top
and bottom sides.
A
B
C
28
28A
A
28B
A
B
C
28C
Summary of Contents for Artiglio Master 28
Page 2: ......
Page 15: ...Artiglio Master 28 Operator s manual 97 EN 21 20 18 16 19 16 9 4 17 14 6 15 7 2 1 5...
Page 16: ...98 Artiglio Master 28 Operator s manual 10 8 7 13 22 11 12 3 15...
Page 68: ...150 Artiglio Master 28 Operator s manual M13 M14 M11 M7 M2 M9 A M16 STANDARD RIM...
Page 69: ...Artiglio Master 28 Operator s manual 151 EN RIM WITH EMBEDDED HOLE M6 M5 M11 M7 M9 B...
Page 70: ...152 Artiglio Master 28 Operator s manual REVERSE RIM C M11...
Page 71: ...Artiglio Master 28 Operator s manual 153 EN D M10 M2 M15 M9 RIM FOR VANS...
Page 72: ...154 Artiglio Master 28 Operator s manual E RIM WITHOUT CENTRAL HOLE...
Page 73: ...Artiglio Master 28 Operator s manual 155 EN F RIM WITH CENTRAL HOLE...
Page 76: ...158 Artiglio Master 28 Operator s manual...
Page 77: ...Artiglio Master 28 Operator s manual 159 EN...
Page 78: ...160 Artiglio Master 28 Operator s manual...
Page 79: ...Artiglio Master 28 Operator s manual 161 EN...
Page 80: ...162 Artiglio Master 28 Operator s manual...
Page 82: ...164 Artiglio Master 28 Operator s manual...