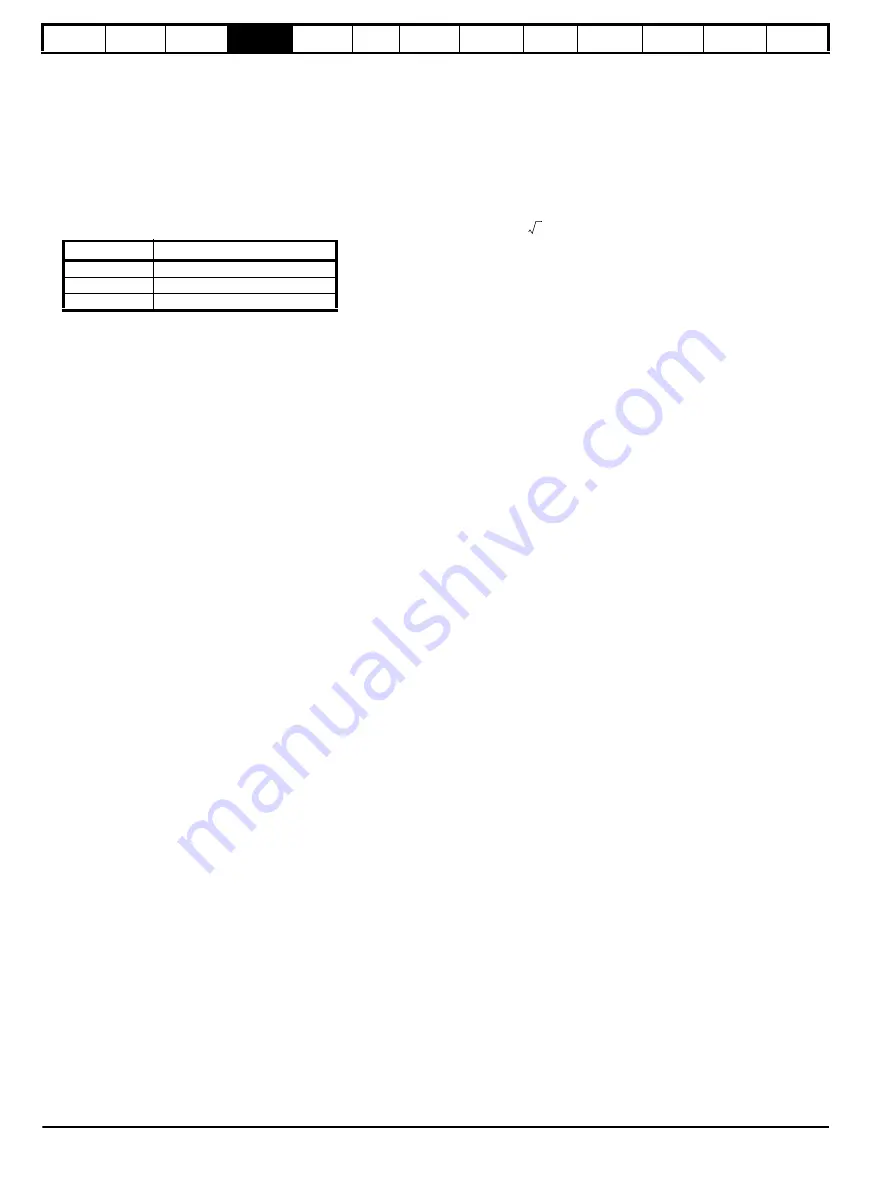
Safety
Information
Product
Information
Mechanical
Installation
Electrical
Installation
Getting
Started
Menu 0
Running
the motor
Optimisation
Macros
Advanced
Parameters
Technical
Data
Diagnostics
UL Listing
Information
40
Unidrive User Guide
www.controltechniques.com Issue Number: 9
4.2 AC supply requirements
Voltage:
UNIX20XLV
200V to 240V ±10%
UNIX40X
380V to 480V ±10%
Number of phases: 3
Minimum supply imbalance: 2% negative phase sequence (equivalent to
3% voltage imbalance between phases)
Frequency range: 48Hz to 65Hz
Maximum supply fault current:
4.2.1 IT supplies
Special considerations are required when the neutral point of the
distribution winding of the supply transformer is not directly grounded.
Before using the drive on such a supply, please contact the supplier of
the drive.
4.2.2 Installation category
Drives are suitable for use on supplies of installation category III and
lower, according to IEC60664-1. This means they may be connected
permanently to the supply at its origin in a building, but for outdoor
installation additional over-voltage suppression (transient voltage surge
suppression) must be provided to reduce category IV to category III.
4.2.3 Supplies requiring line reactors
Input line reactors reduce the risk of damage to the drive resulting from
poor phase balance or severe disturbances on the supply network.
Where line reactors are to be used, reactance values of approximately
2% are recommended. Higher values may be used if necessary, but may
result in a loss of drive output (reduced torque at high speed) because of
the voltage drop.
For all drive ratings, 2% line reactors permit drives to be used with a
supply unbalance of up to 3.5% negative phase sequence (equivalent to
5% voltage imbalance between phases).
Severe disturbances may be caused by the following factors, for
example:
•
Power factor correction equipment connected close to the drive.
•
Large DC drives having no or inadequate line reactors connected to
the supply.
•
Direct-on-line started motor(s) connected to the supply such that
when any of these motors are started, the voltage dip exceeds 20%
Such disturbances may cause excessive peak currents to flow in the
input power circuit of the drive. This may cause nuisance tripping, or in
extreme cases, failure of the drive.
Drives of low power rating may also be susceptible to disturbance when
connected to supplies with a high rated capacity.
Line reactors are particularly recommended for use with the following
drive models when one of the above factors exists, or when the supply
capacity exceeds 175kVA:
UNI1201 UNI1202 UNI1203 UNI1204
UNI1401 UNI1402 UNI1403 UNI1404
Model sizes 1205, 1405 and larger have an internal DC choke so they
do not require AC line reactors except for cases of excessive phase
unbalance or extreme supply conditions.
When required, each drive must have its own reactor(s). Three individual
reactors or a single three-phase reactor should be used.
Reactor current ratings
The current rating of the line reactors should be as follows:
Continuous current rating:
Not less than the continuous input current rating of the drive
Repetitive peak current rating:
Not less than twice the continuous input current rating of the drive
4.2.4 Input inductor calculation.
To calculate the inductance required (at Y%), use the following equation:
Where:
I
= drive rated input current (A)
L
= inductance (H)
f
= supply frequency (Hz)
V
= voltage between lines
4.3 Supplying the drive with DC / DC bus
paralleling
The drive may be supplied with DC instead of 3 phase AC. For further
information please refer to the supplier of your drive.
Connecting of the DC bus between several drives is typically used to:
1. Return energy from a drive which is being overhauled by the load to
a second motoring drive.
2. Allow the use of one braking resistor to dissipate regenerative
energy from several drives.
There are limitations to the combinations of drives which can be used in
this configuration.
For application data, contact the supplier of the drive.
4.4 Ratings
The input current is affected by the supply voltage and impedance.
4.4.1 Typical input current
The values of typical input current are given to aid calculations for power
flow and power loss.
The values of typical input current are stated for a balanced supply.
4.4.2 Maximum continuous input current
The values of maximum continuous input current are given to aid the
selection of cables and fuses. These values are stated for the worst case
condition with the unusual combination of stiff supply with bad balance.
The value stated for the maximum continuous input current would only
be seen in one of the input phases. The current in the other two phases
would be significantly lower.
The values of maximum input current are stated for a supply with a 2%
negative phase-sequence imbalance and rated at the maximum supply
fault current given in Table 4-1.
Frame size
Symmetrical fault level (kA)
1, 2, 3
5
4
10
5
18
L
Y
100
----------
V
3
-------
×
1
2
π
fl
-----------
×
=
Summary of Contents for Unidrive 1 Series
Page 208: ......