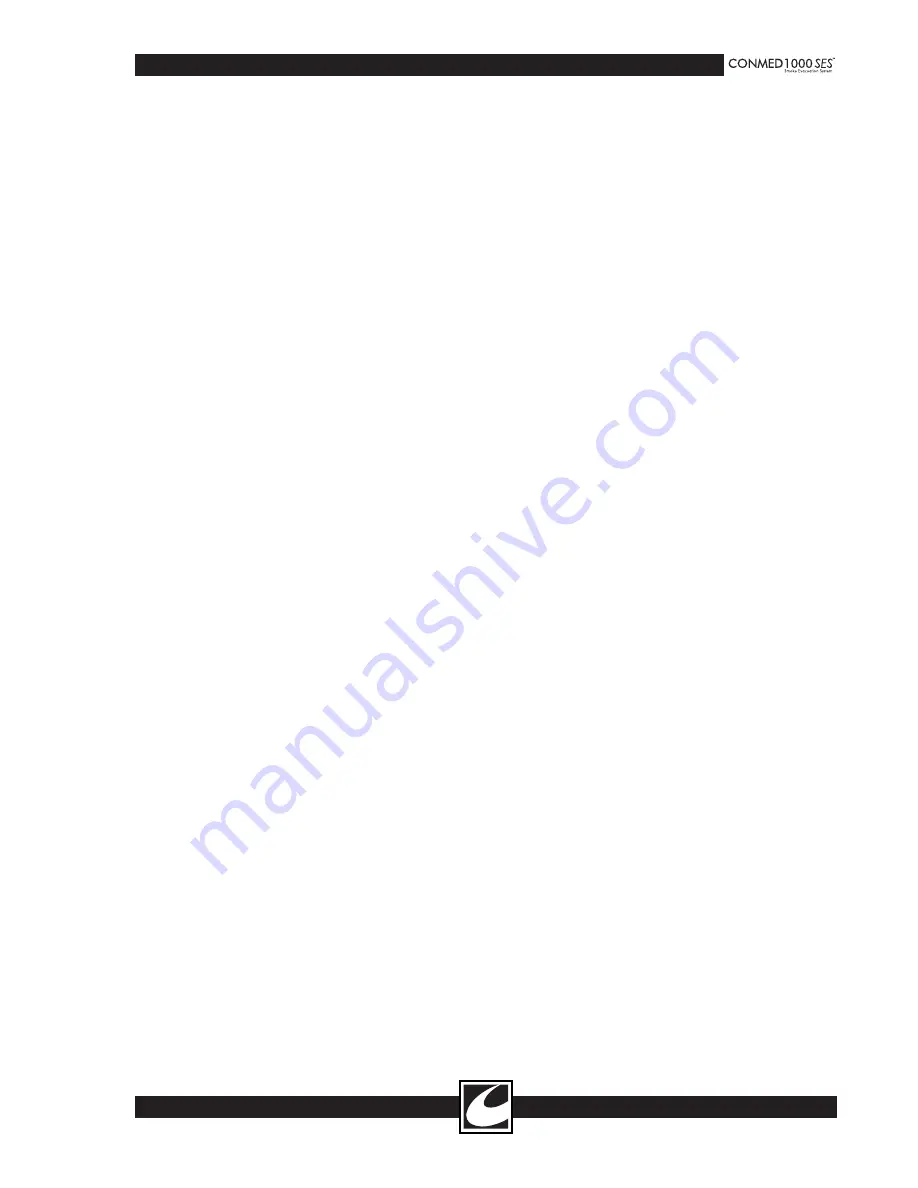
6-3
6.6 Disassembly
WARNING: Service should only be attempted
by qualified service personnel. Refer to
Section 4.0 for instructions on returning the
unit to CONMED for factory service.
Caution: This device contains components
which will be damaged by static electricity.
Proper handling by a grounded service techni-
cian is mandatory. CONMED will provide
assistance if needed in safeguard precautions
necessary to avoid any question of warranty
responsibility.
WARNING: Before performing any work on
the CONMED 1000 SES be sure the system
is turned off and the electrical plug has been
disconnected from the wall outlet.
6.6.1 Disassembly Instructions
For servicing of the CONMED 1000 SES Smoke
Evacuation System, the unit will need to be disas-
sembled. Read the instructions below before
attempting to service the system. During the dis-
assembly of the unit, refer to Figures 6, 7, and 8.
The disassembly of the CONMED 1000 SES
Smoke Evacuation System is performed as fol-
lows:
Using an Allen wrench, remove the 14 screws
that hold the cover on the system.
Remove the cover slowly, so as to not disconnect
the ground wire. Unscrew the retaining nut that
holds the ground wire in place using a wrench.
If necessary, using an Allen wrench, remove the
bolts that connect the rubber feet.
If necessary, carefully remove the insulation from
the base. If any insulation is removed it may not
be reinstalled because the adhesive may not func-
tion properly. Newer models do not have adhe-
sive and should be re-assembled per the insulation
installation instruction provided in the Insulation
Assembly diagram, Figure 7.
6.6.2 Main Housing Disassembly
Remove all insulation from the bottom of the
shell.
Remove motor/vent insulation pieces from the
back of the shell. The motor should now be
exposed.
Remove 3" thick pieces from around the round
tube assembly.
Remove the 4 bolts that hold the motor in place,
using an Allen wrench.
Using a wrench, remove the bolt from the motor
mount bracket.
Disconnect the E-Term connectors. Disconnect
the ground connector screw using a socket
wrench
Remove motor. You may at this time also remove
the motor gasket.
Remove 6 nuts from the round tube retainer ring,
using a socket wrench. Remove tube from shell
assembly.
Remove the front/top insulation.
To remove the handle, unscrew the 2 bolts, using
an Allen wrench. This will also remove the alu-
minum separator plate and the handle at the same
time.
Remove all wires from the circuit breaker, power
entry module and printed circuit board.
To remove the circuit breaker, press the tabs locat-
ed on the inside of the systems on each side of
the circuit breaker.
To remove the power entry module, press the
tabs on either side of the module. You may need a
screwdriver to accomplish this operation.
60-6852-ENG (-).qxd 2/1/99 12:40 PM Page 6-3
Summary of Contents for 1000 SES
Page 1: ...Service Manual English Version Smoke Evacuation System...
Page 14: ...4 2 This page intentionally left blank...
Page 17: ...5 3 Figure 5 System Block Diagram...
Page 18: ...5 4 This page intentionally left blank...
Page 23: ...6 5 Figure 6 Exploded View...
Page 24: ...6 6 Figure 7 Insulation Assembly...