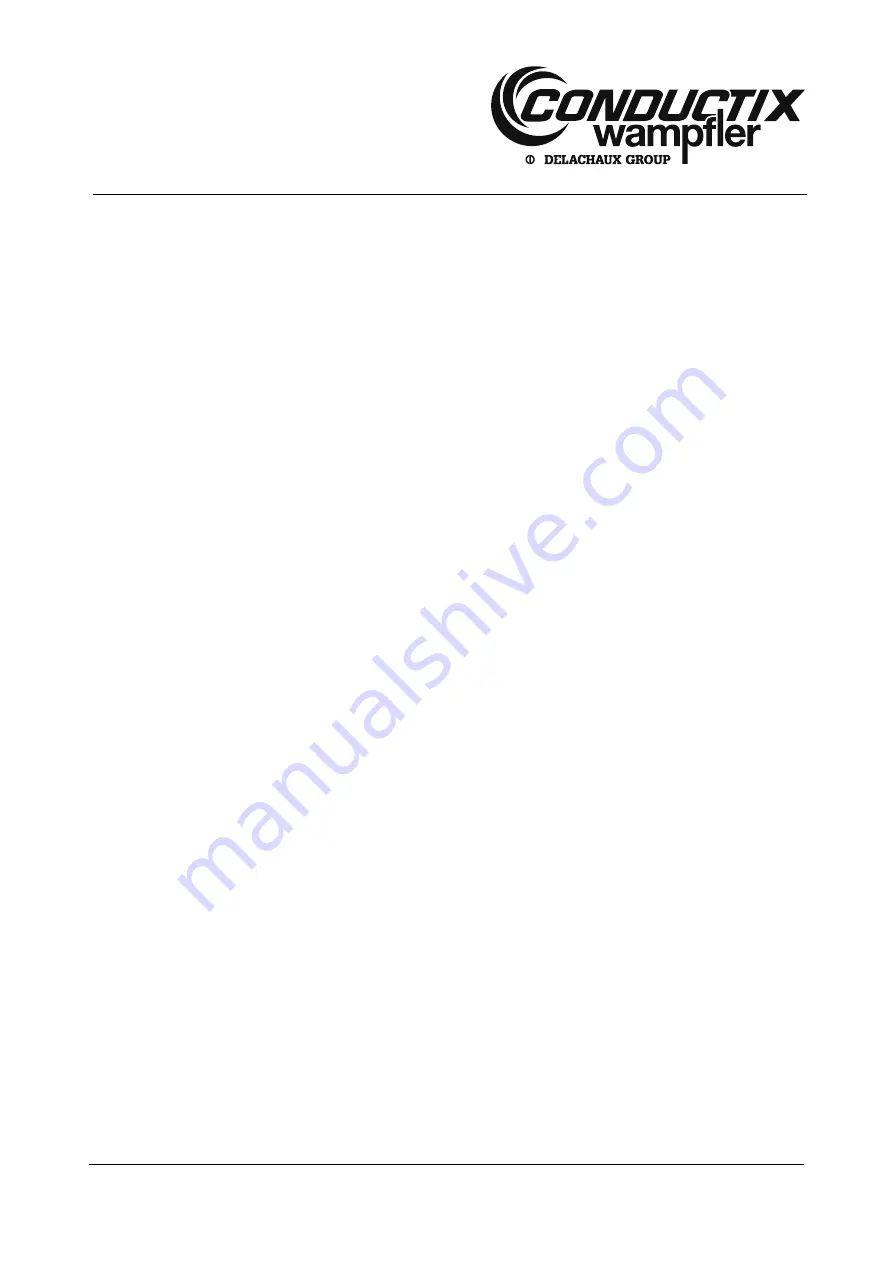
Mounting Instructions
ProfiDAT
®
Data Transmission System
Programm 0514
MAL0514-0005b-EN
www.conductix.com
translated document
page 37 of 82
6.2
Preparations
Required tools:
Open-ended spanner, SW10
Open-ended spanner, SW17
Open-ended spanner, SW24
Set of Allen keys, SW3
Allen key, SW5
Phillips screwdriver
Torque wrench
Lubricant
Hot air blower
Chop saw
Required material:
Cable ties
Shrink sleeve
Conductive paste 080021
Lubricant for stainless-steel screws, recommended: Klüber 46 MR 401 paste
Klüber Lubrication München KG
Geisenhausenerstr. 7
D-81379 Munich
Screw tightening torques:
M6 screw (SW10 open-ended spanner): 8 Nm
M10 screw (SW17 open-ended spanner): 40 Nm