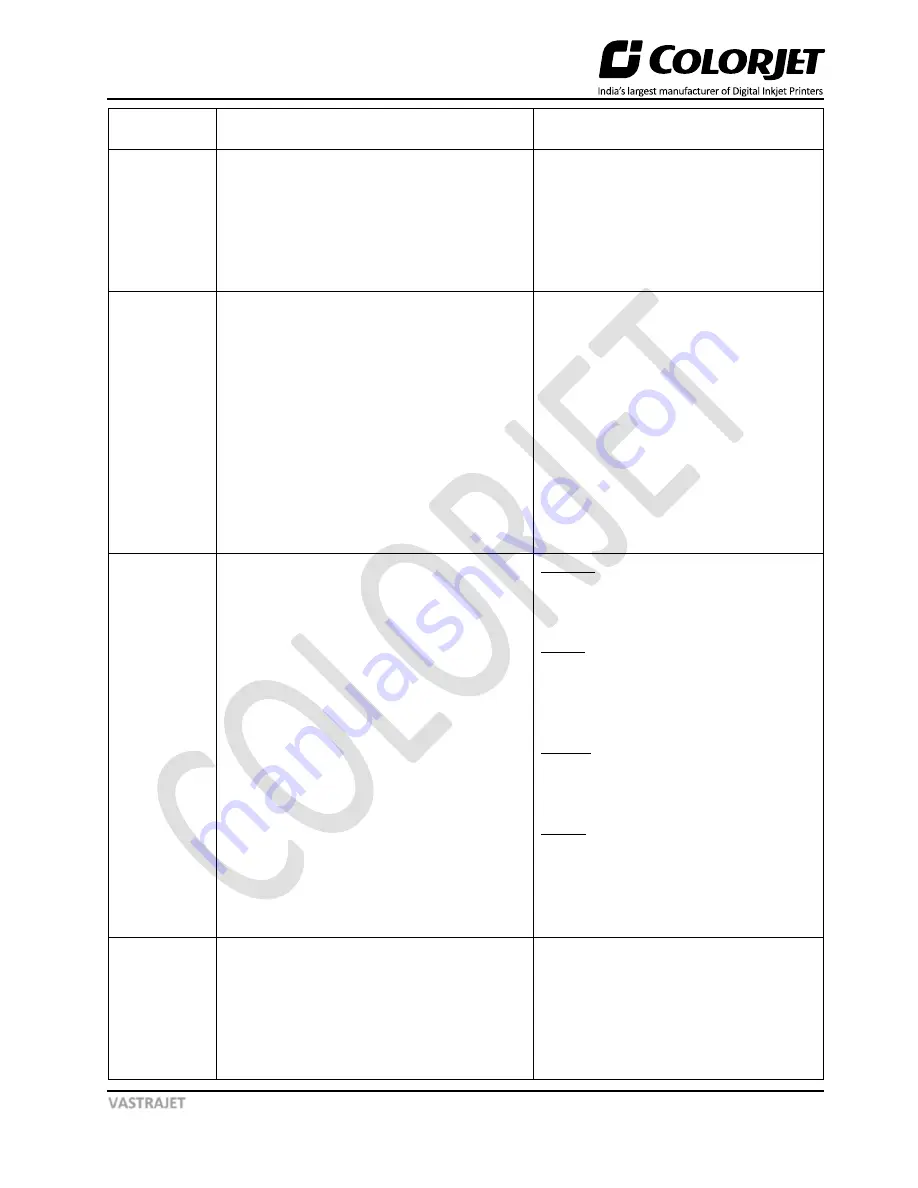
Page | 60
VASTRAJET
b)
Align the pulley with respect to
Belt
Conveyor
Belt Not
Working
1.
No signal to Conveyor Belt
2.
Displayed error code in Servo driver
3.
Conveyor Belt Coupling is loose
Case 1:
Loose connection in Servo Driver,
Relay, Main Board, & PLC.
Case 2:
Check error code in the
Error
Code Handling
section and take an action
to resolve the error.
Case 3:
Tighten the Conveyor Belt
Coupling.
Washing Tub
Not Engaging
Properly
1.
Sensor position is disturbed
2.
Actuator not working
3.
Washing tub fuse blown
4.
No output from
transformer/rectifier
5.
PLC connection is loose or faulty
6.
Relay or relay connection is faulty
Case 1:
Correct the sensor position by
moving the tub up or down.
Case 2:
Check 24 VDC near the actuator
connector and also check the loose
connection, if any.
Case 3:
Check actuator fuse and replace
it, if required.
Case 4
: Check the transformer output
(must be at 24 VAC) and rectifier output
(must be at 24 VDC).
Case 5:
Check PLC connection.
Case 6:
Check input and output power at
relay and relay connection.
Heater Not
Working
1.
Inlet power not connected or MCB
trip
2.
Heater coil/thermistor/thermo-stat
circuit is open
3.
24 V Input is not getting supply to SSR
4.
Improper settings in PID or faulty
Case 1:
Check the Inlet power in
connector near heater. Check for any
fault in circuit and ON the MCB after
correcting the fault.
Case 2:
Perform the following actions:
1.
Check the continuity/resistance
between
heater
wire
and
thermistor
2.
Replace the defective part, if any
Case 3:
Check 24VDC Voltage at SSR
when PID shows replay ON. And at same
time check 220VAC In Out terminal and
replace SSR, if required.
Case 4:
Perform the following actions as
per the requirements:
a)
Correct the PID settings, if
required.
b)
Check continuity in out terminal
and replace it, if required.
Lines In Print
1.
Nozzle blocked in heads (check
nozzle test)
2.
Incorrect feed step (calibration
required)
Case 1:
Perform Test Print to check the
blockage in nozzles. (Refer to
Issuing the
TEST PRINT Command
section).
Case 2:
Perform the step calibration and
correct the step value. (Refer to
Feed
Calibration
section).