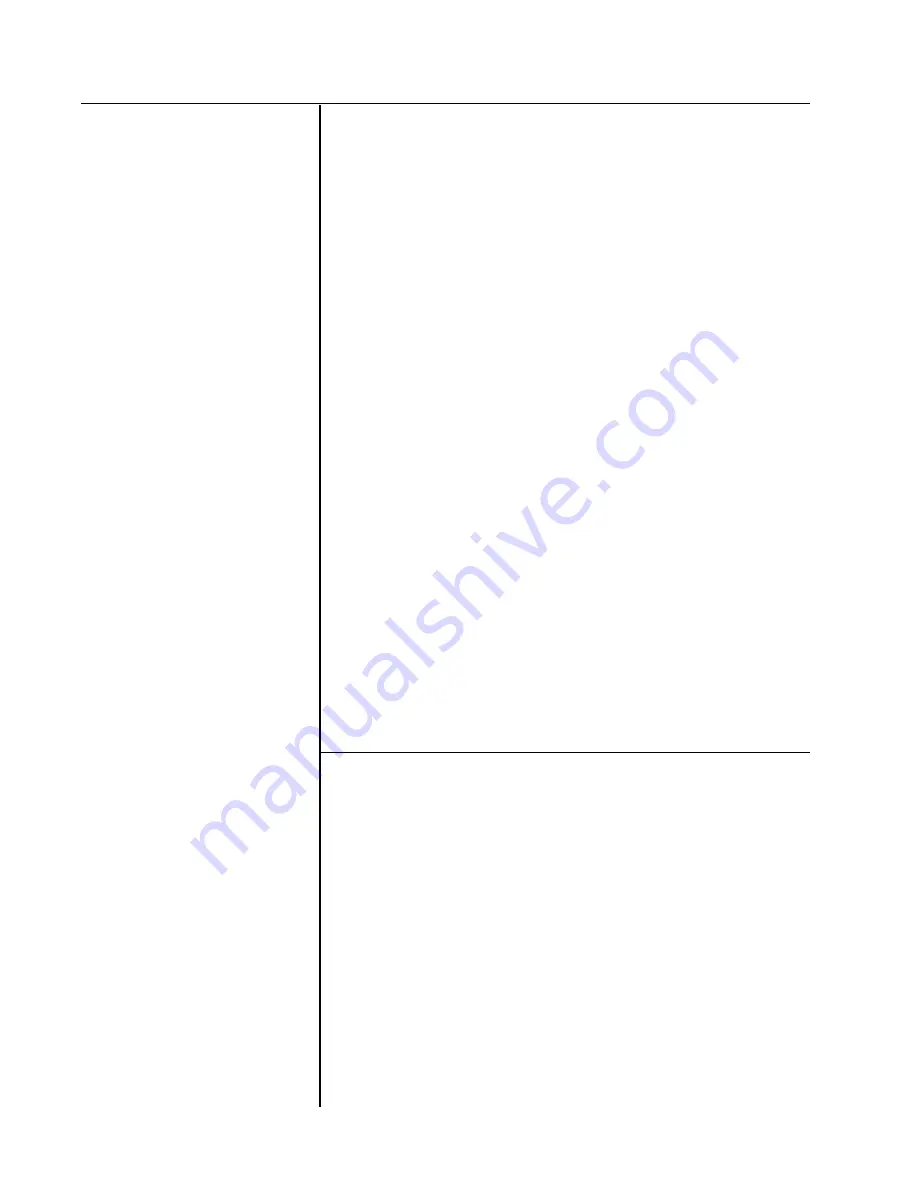
Page 17
Steam Piping Installation
1. Set and anchor dryer in position.
Machine should be level to
assure proper steam circulation.
2. To prevent condensate draining from headers to dryer, piping
should have a minimum 12 (305 mm) above respective
header.
Do not make steam connection to header with a
horizontal or downwardly facing tee or elbow.
3. Whenever possible, horizontal runs of steam lines must drain,
by gravity, to respective steam header. Water pockets, or an
improperly drained steam header will provide wet steam,
causing improper operation of dryer. If pockets or improper
drainage cannot be eliminated, install a bypass trap to drain
condensate from the low point in the steam supply header to
the return.
4. In both steam supply and steam return line, it is recommended
that each have a 3/4 (20 mm) union and 3/4 (20 mm) globe
valve. This will enable you to disconnect the steam
connections and service the dryer while your plant is in
operation.
5. Before connecting trap and check valve to dryer, open globe
valve in steam supply line and allow steam to flow through
dryer to flush out any dirt and scale from dryer. This will
assure proper operation of trap when connected.
6. After flushing system, install bucket trap (with built-in
strainer) and check valve. For successful operation of dryer,
install trap 18" (458 mm) below coil and as near to the dryer
as possible. Inspect trap carefully for inlet and outlet
markings and install according to trap manufacturers
instructions. If steam is gravity returned to boiler, omit trap
but install check valve in return line near dryer.
7. Install union and globe valve in return line and make final
pipe connections to return header.
1. Trap each dryer individually. Always keep the trap clean and
in good working condition.
2. When dryer is on the end of a line of equipment, extend
header at least 4 feet (2 m) beyond dryer. Install globe valve,
union, check valve and bypass trap at end of line. If gravity
returned to boiler, omit trap.
3.
Insulate steam supply and return line for safety of
operator and safety while servicing dryer.
4. Keep dryer in good working condition. Repair or replace any
worn or defective parts.
INSTALLATION
INSTRUCTIONS
PIPING
RECOMMENDATIONS
Summary of Contents for HD125
Page 9: ...Page 9 125 lb General Dimensions Illustration...
Page 10: ...Page 10 125 lb Steam Heated Dryer Dimensions Illustration...
Page 14: ...Page 14 Gas Loop Piping and Gas Supply Piping System Illustrations...
Page 18: ...Page 18 Steam Piping Installation Illustration...
Page 20: ...Page 20 Dryer Installation with Multiple Exhaust Illustration...
Page 27: ...Page 27 Two Timer Models Figures 1 2 and 3 Illustrations...
Page 35: ...Page 35 DIRECTSPARK IGNITIONOPERATION FLOW CHART...
Page 37: ...Page 37 Burner Air Inlet Adjustment with Illustration BURNERAIRINLET ADJUSTMENT...
Page 38: ...Page 38 Basket Alignment for 125 lb Dryers Illustrations...
Page 66: ...Page 66...