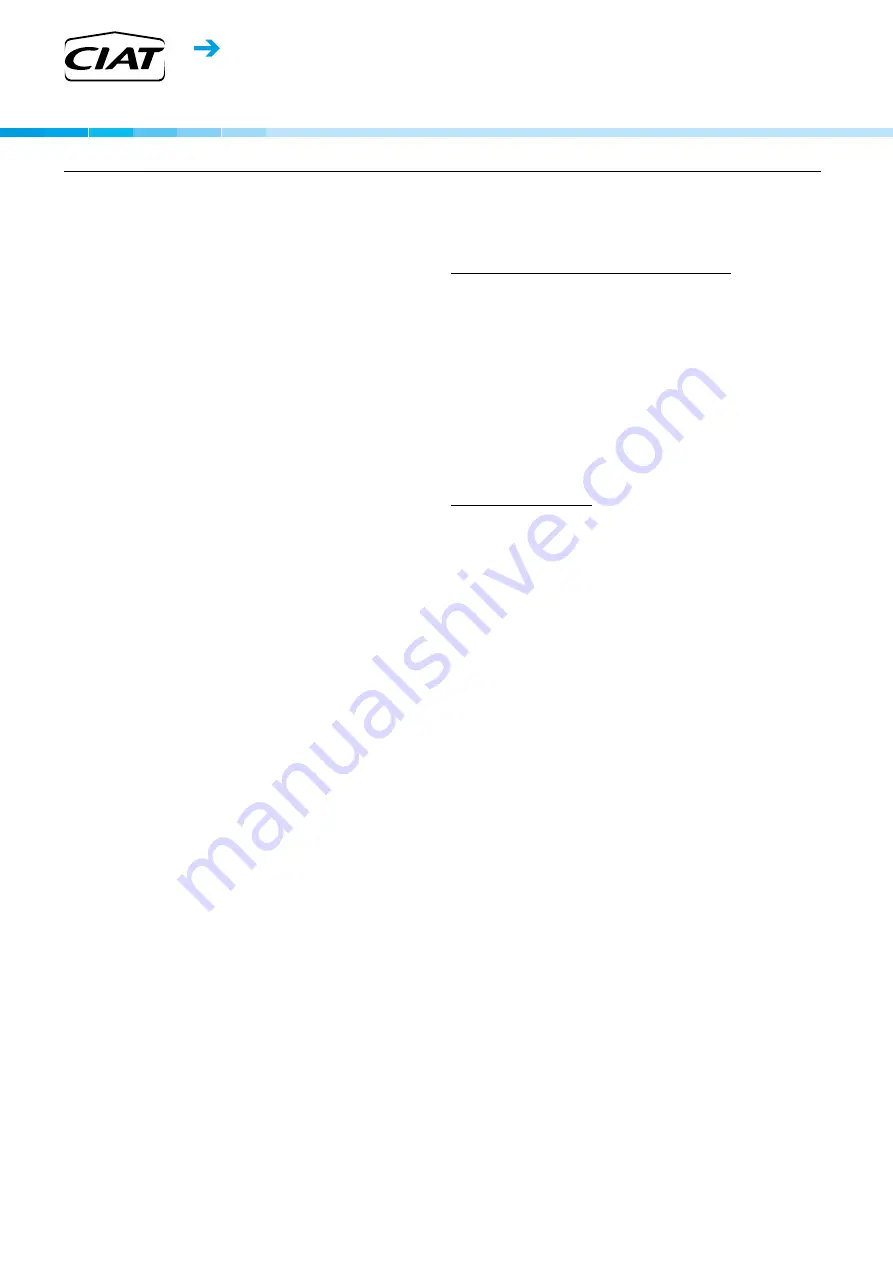
36
HEAT PUMPS - AIR CONDITIONING - REFRIGERATION - AIR HANDLING - HEAT EXCHANGE - NA 18.752 B
Water chillers
Heat pump
HYDROCIAT LW
■
General
Chilled and hot water will be produced by a
CIAT HYDROCIAT
LW-type
water-to-water unit, which is a single unit assembly
designed for indoor installation
The chiller (or heat pump) will use environmentally-friendly
R134a
refrigerant. It will include 1 or 2 independent cooling circuits and
will be equipped with 1 or 2 SCREW compressors, depending on
the model
The unit will be designed, produced and tested at a production
plant with a quality-assurance system which is certified according
to
ISO 9001, 14001 and 50001
. Performance levels will be
certified by the
EUROVENT association within the limits of the
certification programme
The machine will be covered by an EC declaration of conformity
and will comply with the following European regulations and
standards:
- Machinery Directive 2006/42/EC and EN 60-204 -1
- Electromagnetic Compatibility Directive 2014/30/EU
- EMC Immunity and Emissions EN 61800-3 "C3"
- Low Voltage Directive 2014/35/EU
- RoHS 2011/65/EU
- Pressure Equipment Directive (PED) 2014/68/EU
- Refrigeration systems and heat pumps EN 378-2.
- Regulation (EU) 2016/2281 implementing Directive 2009/125
EC with regard to ecodesign requirements
■
Performance levels
Cooling capacity (kW): ……
Total electrical power used: …… kW
Heating capacity: …….. kW
Minimum EER coefficient of performance at full load according to
the EN14511:3-2013 standard:….
Minimum SEER
12/7°C
seasonal coefficient of performance
according to Ecodesign Regulation (EU) 2016/2281 certified by
the independent association Eurovent (mandatory):….
Evaporator chilled water entering/leaving temperature: …/…°C
Pressure drops for the evaporator: ....
Secondary fluid: ....
Condenser hot water entering/leaving temperature: …/…°C
Pressure drop for the condenser: ....
Secondary fluid:
Type of refrigerant: R134a (ODP=0 / GWP=1430)
CO
2
equivalent tonne: ….
Dimensions (length x width x height): ……x…..x….. mm
Unit operating weight: …. Kg
The environmental report including the analysis of the life
cycle of the unit must be supplied by the manufacturer
The unit shall be capable of starting up with a condenser entering
water temperature of
13°C with the control option for low
condensing temperature.
The unit must be capable of starting
up with an evaporator entering water temperature of
35°C
.
The unit will be able to operate with a condenser leaving water
temperature of
63°C with the high condensing temperature
option
■
Compressors
These components are semi-hermetic double screw-type compressors
with a motor cooled by suction refrigerant gas, and protected against
overheating.
They will include the following standard components:
- 2 screws fitted on ball and roller bearings.
- The ball bearings will be designed to last for a minimum of
73,000 hours under maximum operating conditions.
- Continuous capacity control of 15% to 100% on each compressor
- Monitoring of rotation direction, absence of phase, over and
under voltage, and power supply failure
- Monitoring of maximum head pressure
- Controlled lubrication under differential pressure
requiring no oil
pump
- The oil circuit must include a filter with a filtration capacity of 5
microns with service shut-off valves to facilitate its replacement
- The oil separator must be built into the design of the condenser and
include an oil level safety switch.
-
Silencer fitted at the discharge to reduce pulses from the
discharged gas
Compressor electric motor
- large motor with
star-delta
starting to reduce the starting current of
each compressor
- motor cooled by intake gas
- integral electronic protection of the motor against thermal and
electrical overloads
●
Service valves (option)
Shut-off valves on the liquid line (evaporator inlet) and on the
compressor suction line to facilitate maintenance
●
Compressor thermal insulation (option)
Thermal insulation used to prevent the formation of condensation
on the surface of the compressor.
■
Evaporator
A single, high-performance, glandless-type evaporator with copper
tube bundle with internal and external grooves
The design includes 1 or 2 independent cooling circuits.
Two entering and leaving water temperature sensors on the
exchanger are used to regulate the 'return water' or 'leaving water'.
The heat insulation is made from shaped cellular foam,
at least
19 mm thick
.
The hydraulic unions will be
"VICTAULIC"
-type unions to ensure
quick connection between the unit and hydraulic system.
The maximum operating pressure on the water side is
10 bar (21
bar as an option)
The evaporator will be equipped with an electronic flow
controller. Paddle-type sensors or differential pressure
controllers shall not be acceptable.
Several choices of hydraulic connections will be available
on the evaporator to adapt to all possible constraints (see
options available)
●
Evaporator flexible sleeves (option)
The manufacturer will supply flexible connection sleeves to
insulate the unit and limit the transmission of vibrations to the
hydraulic network.
●
Sound level reduction (option)
The evaporator and suction pipework will be fitted with
soundproofing to reduce the noise radiated from the machine
to 3 dB
s
pecification
gUiDe
Summary of Contents for HYDROCIAT LW HE Series
Page 43: ......