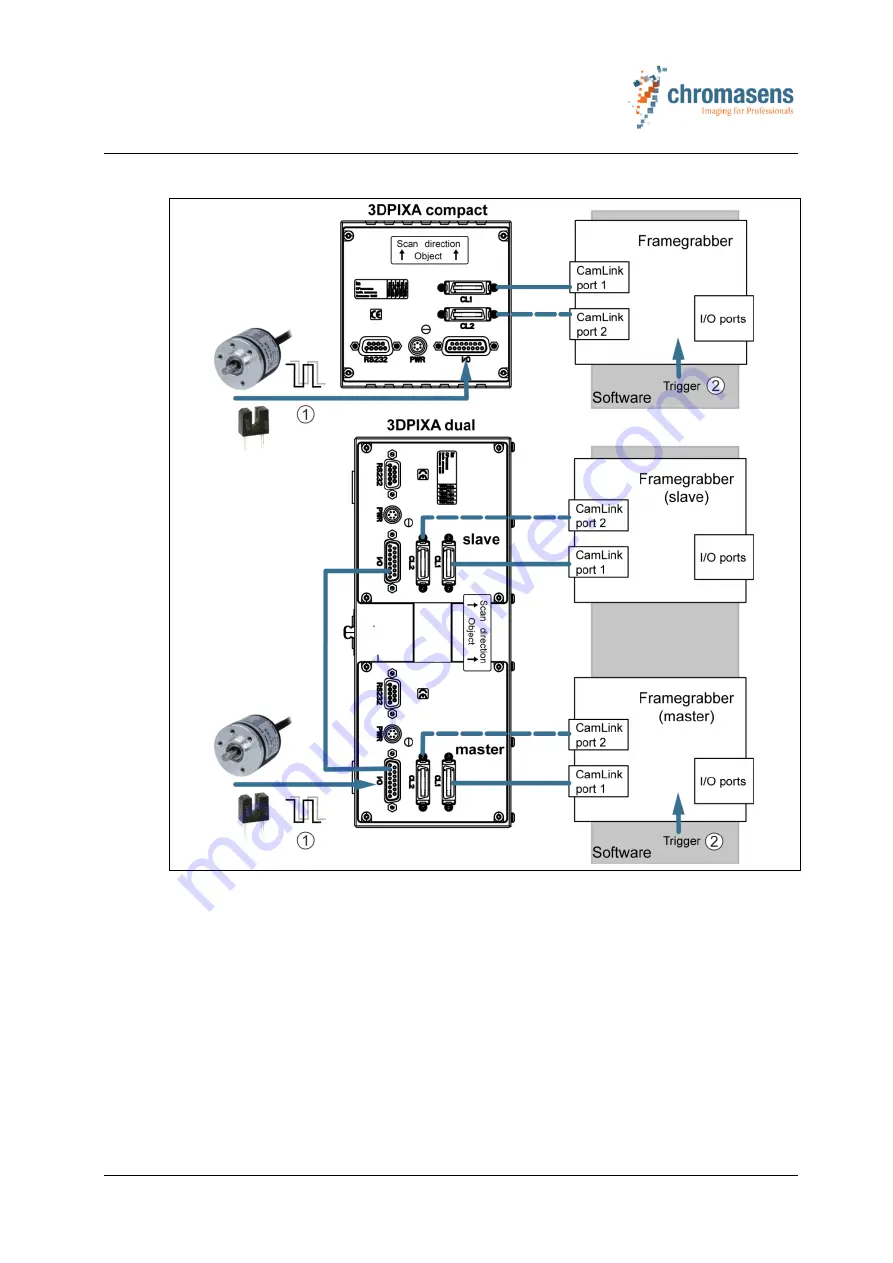
5 Installing the 3D scanner system
48 / 99
CD40131 Version 1
3DPIXA
Connecting the trigger devices via the I/O port of the camera
Fig. 24: Trigger device connections via I/O port of the camera
1
Trigger device connection (hardware trigger
)
2
Software trigger
The hardware trigger signals are transferred via the I/O connection to the camera.