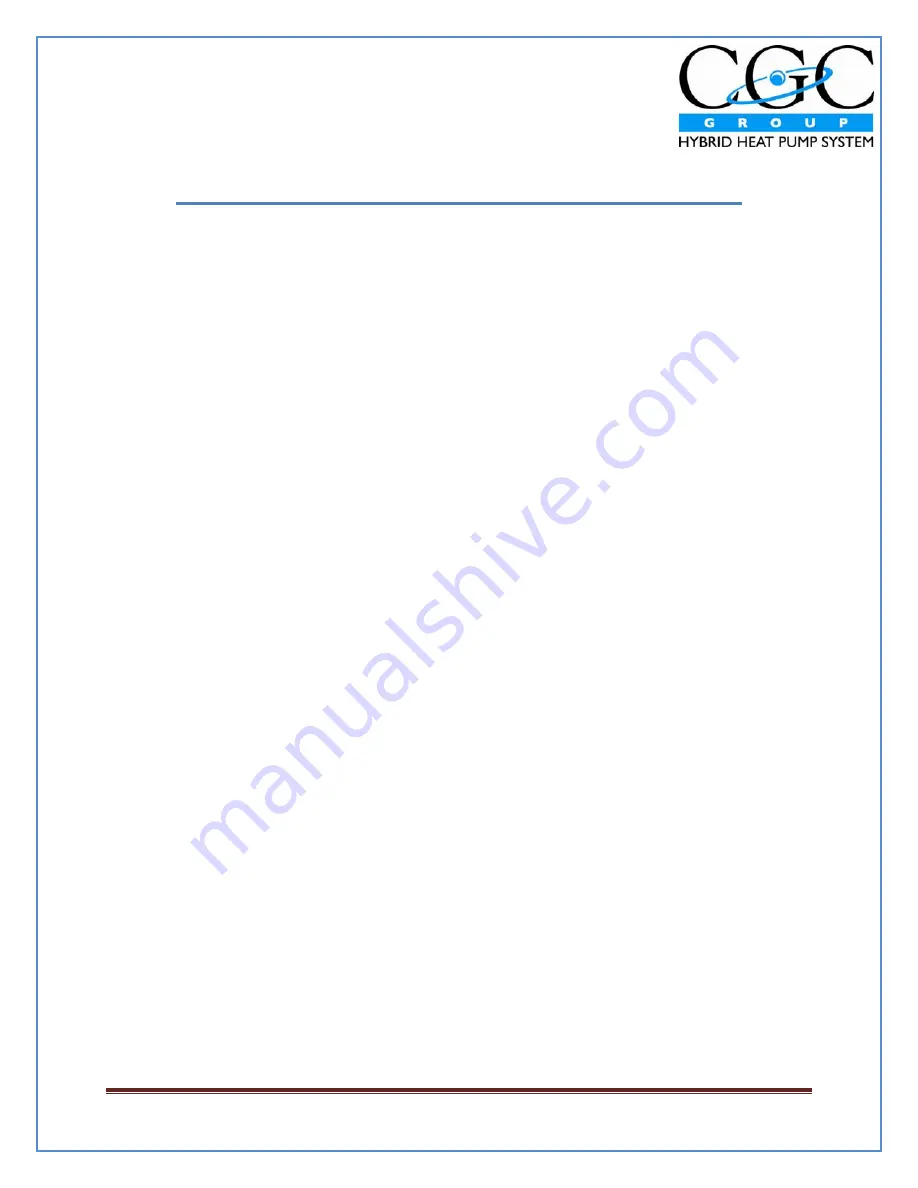
Hybrid
Vertical
Stack
–
Installation
Operation
Maintenance
Manual
COMMISSION
&
START
UP
R090303
Installation
Operation
Maintenance
Manual
is
subject
to
change
without
notice
Page
17
System
Flushing:
Proper
system
cleaning
and
flushing
is
an
important
aspect
of
the
commissioning
and
start
up
procedure
for
hybrid
units.
Ensure
the
system
has
been
flushed
properly.
This
prevents
fouling
of
the
unit’s
heat
exchangers.
NOTE:
Hydronic
coils
are
not
100%
drainable.
System
Fluid:
Ensure
that
system
water
temperature
is
within
an
acceptable
range
to
facilitate
start
‐
up
(80
‐
120°F)
for
cooling
and
(100
–
140°F)
for
heating.
System
Water
pH:
System
water
should
have
a
neutral
pH
balance
of
approximately
7.5
which
will
extend
the
life
of
the
hoses,
heat
exchangers,
and
other
water
side
accessories.
Water
Flow
Rate:
Open
all
isolation
valves
to
the
unit.
Ensure
that
the
entering
and
leaving
fluid
temperatures
of
the
hybrid
unit
in
operation
are
acceptable.
There
is
typically
an
8
to
12
degree
drop
or
rise
in
temperature,
depending
on
whether
the
unit
is
in
cooling
or
heating.
Under
extreme
conditions,
slight
variances
in
the
temperature
may
be
noted.
Freeze
Protection
from
Water
System:
Ensure
that
freeze
protection
is
provided
for
the
outdoor
portion
of
the
loop
water
system.
Inadequate
freeze
protection
can
lead
to
coil
damage.
NOTE:
A
potential
issue
may
arise
during
construction
where
the
system
fluid
loop
is
drained
after
being
cleaned,
flushed
and
tested.
Hybrid
vertical
stack
units
will
not
completely
drain
and
may
hold
fluid
in
the
condenser
or
heating
coil.
Extensive
damage
may
result
to
internal
components
if
the
system
fluid
freezes
unless
adequate
glycol
is
added.
Remove
Air
from
System
Fluid
Loop:
Air
in
the
system
impairs
unit
operation
and
can
cause
erosion
in
the
system
piping.