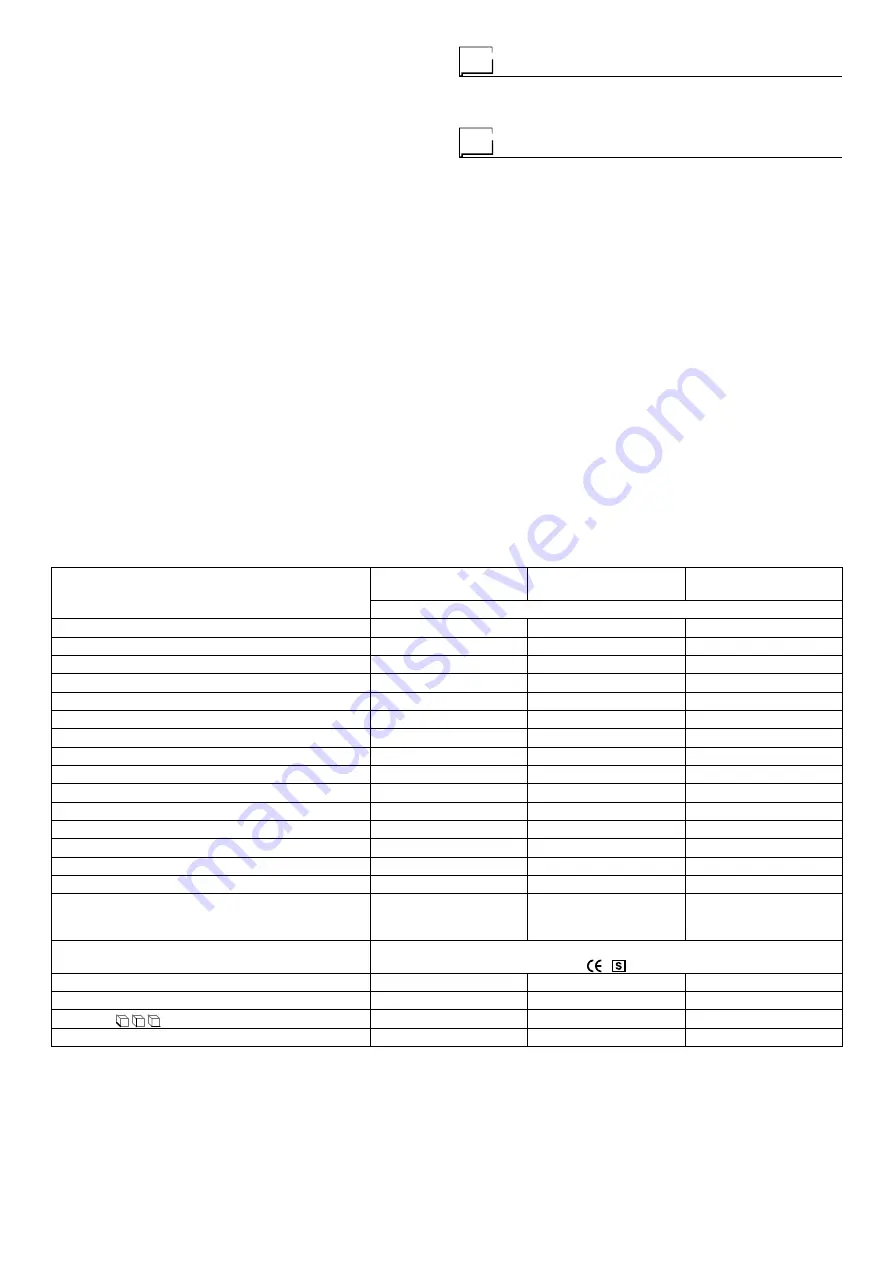
3
- WSC Wire start control. This arc striking control device pre-
vents wire from sticking to the workpiece or torch nozzle
and ensures precise and smooth arc striking, particularly
when welding aluminium.
- Welding parameters that are controlled digitally by a micro-
processor, are monitored and modified in just a few sec-
onds, maintaining a consistently precise and stable arc as
the welding conditions continue to vary due to the move-
ment of the torch and the irregularities of the parts to be
welded.
- Exclusive SWS “Smart Welding Stop” system at the end of
TIG welding. Lifting up the torch without switching off the
arc will introduce a slope down and it will switch off auto-
matically.
- “Energy Saving” function to operate the power source cool-
ing fan and the torch water cooling only when necessary.
- Auto-diagnostic feature for trouble shooting.
- Password-controlled total or partial equipment access.
• High electrical performance resulting in a reduction in ener-
gy consumption.
• Remote parameter adjustment directly from HT4 feeder.
Technical data
The general technical data of the system are summarized in
table 1.
Usage limits (IEC 60974-1)
The use of a welder is typically discontinuous, in that it is made
up of effective work periods (welding) and rest periods (for the
positioning of parts, the replacement of wire and underflush-
ing operations etc. This welder is dimensioned to supply a I
2
max nominal current in complete safety for a period of work of
40/50% of the total usage time. The regulations in force estab-
lish the total usage time to be 10 minutes. The work cycle is
considered to be 40/50% of this period of time. Exceeding the
work cycle allowed could cause a trip switch to trip (for further
information see the DH control panel manual), which protects
the components inside the welding machine against dangerous
overheating. After several minutes the overheat cut-off rearms
automatically and the welder is ready for use again.
Table 1
Model
DIGITECH vision PULSE
3300
DIGITECH vision PULSE
4000
DIGITECH vision PULSE
5000
MIG-MAG welding
Three-phase input 50/60 Hz
V
400 ± 20%
400 ± 20%
400 ± 20%
Mains supply: Z
max
Ω
0,037
0,028
0,017
Input power @ I
2
Max
kVA
18,8
25,5
32
Delayed fuse (I
2
@ 60%)
A
25
30
40
Power factor / cos
φ
0,64 / 0,99
0,66 / 0,99
0,66 / 0,99
Efficiency degree
η
0,83
0,86
0,89
Open circuit voltage
V
63
70
70
Current range
A
10 ÷ 330
10 ÷ 400
10÷500
Duty cycle @ 100% (40°C)
A
280
330
380
Duty cycle @ 60% (40°C)
A
300
370
460
Duty cycle @ X% (40°C)
A
330 (40%)
400 (50%)
500 (50%)
Wires diameter (*)
mm
0,6 ÷ 1,2 (*)
0,6 ÷ 1,6 (*)
0,6 ÷ 1,6 (*)
N° rollers (*)
4 (*)
4 (*)
4 (*)
Power output of feeder motor (*)
W
100 (*)
100 (*)
100 (*)
Rated wire feeding speed (*)
m/min
0,5 ÷ 25 (*)
0,5 ÷ 25 (*)
0,5 ÷ 25 (*)
Spool (*)
Diameter
Weight
mm
kg
Ø300 (*)
15 (*)
Ø300 (*)
15 (*)
Ø300 (*)
15 (*)
Standards
IEC 60974-1 - IEC 60974-5 (*) - IEC 60974-10
Protection class
IP 23 S
IP 23 S
IP 23 S
Insulation class
H
H
H
Dimensions
mm
660 - 515 - 290
660 - 515 - 290
660 - 515 - 290
Weight
kg
35
40
44
(*) On the HT4 feeder, fitted separately.
WARNING:
This equipment complies with
EN//IEC 61000-3-12
provided that the maximum permissible system impedance Z
max
is less than or
equal to 0,037
Ω
DIGITECH vision PULSE 3300 - 0,028
Ω
DIGITECH vision PULSE 4000 - 0,017
Ω
DIGITECH vision PULSE 5000 at the in-
terface point between the user’s supply and the public system. It is the responsibility of the installer or user of the equipment to ensure, by con-
sultation with the distribution network operator if necessary, that the equipment is connected only to a supply with maximum permissible system
impedance Z
max
less than or equal to 0,037
Ω
DIGITECH vision PULSE 3300 - 0,028
Ω
DIGITECH vision PULSE 4000 - 0,017
Ω
DIGITECH
vision PULSE 5000.
This system, tested according to
EN/IEC 61000-3-3
, meets the requirements of
EN/IEC 61000-3-11
.