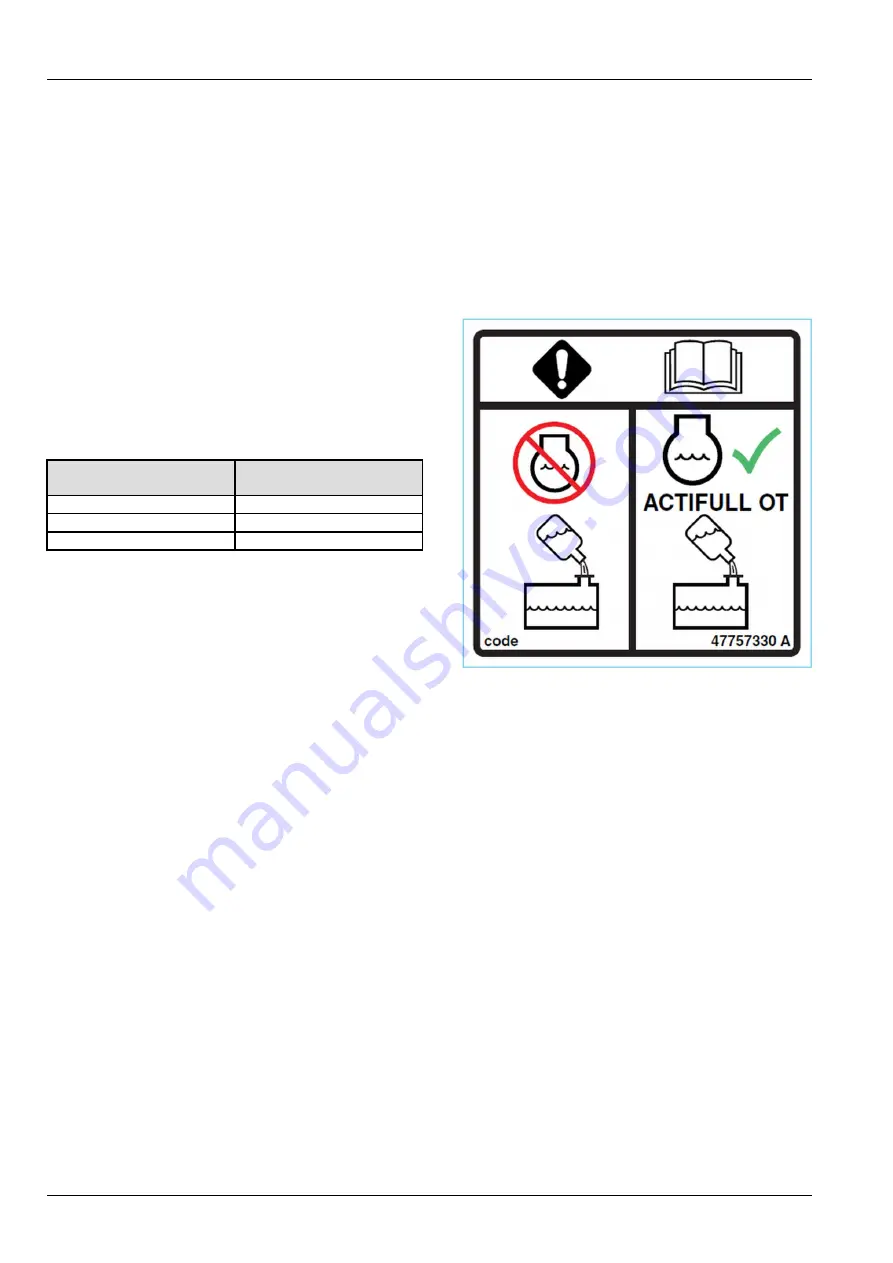
7 - MAINTENANCE
Washing of the cooling system
1. Empty the engine cooling system by draining the coolant into a suitable container.
2. Fill the system with clean water.
3. Start the engine and run the engine for at least
30 min
.
NOTE:
make sure that you activate the heating system (if equipped) to circulate fluid through the heater core.
4. Repeat Steps 1 to 3 for a total of two washes.
5. Fill the system with OAT coolant.
6. Operate the engine until it is warm. Inspect the machine for leaks.
You can identify OAT coolant by its yellow color. Also, the
decal shown is located near the fill point of the cooling
system whenever the factory fill is
CASE AKCELA ACT-
IFULL™ OT EXTENDED LIFE COOLANT
. This decal is
available in three different sizes. See the table below for
the associated part numbers.
CNH Industrial part
number
Size
47757330
50 mm
x
50 mm
47757331
75 mm
x
75 mm
47757332
100 mm
x
100 mm
47757330
1
Definitions
Conventional coolant:
A coolant that relies on inorganic inhibitors such as sil-
icates, nitrites, and phosphates for corrosion and cavi-
tation protection.
Organic Acid Technology (OAT) coolant:
A coolant that relies on inhibitors such as organic acid
salts (potassium and sodium salts) for corrosion and
cavitation protection. The organic salts produce a pro-
tective film on the cylinder lines, avoiding cavitation ero-
sion.
7-18
Summary of Contents for 721G Stage IV
Page 24: ...1 GENERAL INFORMATION Waste Handler WH configuration LEIL18WHL1118FB 3 721G 1 18 ...
Page 26: ...1 GENERAL INFORMATION LEIL17WHL2018FB 5 821G 1 20 ...
Page 29: ...1 GENERAL INFORMATION LEIL19WHL0584H 1 1 23 ...
Page 30: ...1 GENERAL INFORMATION 1 24 ...
Page 51: ...2 SAFETY INFORMATION Empty tool LEEN11T0024AA 20 2 21 ...
Page 84: ...2 SAFETY INFORMATION 2 54 ...
Page 162: ...3 CONTROLS AND INSTRUMENTS Inducement and validation re starts LEIL14WHL0394HA 2 3 78 ...
Page 163: ...3 CONTROLS AND INSTRUMENTS Validation re start procedure LEIL15WHL0608HA 3 3 79 ...
Page 189: ...4 OPERATING INSTRUCTIONS RCPH10WHL045BAH 7 4 15 ...
Page 191: ...4 OPERATING INSTRUCTIONS RCPH10WHL045BAH 9 4 17 ...
Page 193: ...4 OPERATING INSTRUCTIONS RCPH10WHL045BAH 12 4 19 ...
Page 208: ...4 OPERATING INSTRUCTIONS 4 34 ...
Page 222: ...5 TRANSPORT OPERATIONS 5 14 ...
Page 259: ...7 MAINTENANCE LEIL17WHL1665H 5 721G 7 21 ...
Page 260: ...7 MAINTENANCE LEIL17WHL1665H 6 821G 7 22 ...
Page 267: ...7 MAINTENANCE DEF AdBlue technical faults LEIL14WHL0392HA 4 7 29 ...
Page 291: ...7 MAINTENANCE LEIL18WHL1152AA 14 821G 7 53 ...
Page 300: ...7 MAINTENANCE LEIL15WHL1846AB 2 821G 7 62 ...
Page 313: ...7 MAINTENANCE LEIL18WHL1154FA 1 LEIL18WHL1155FA 2 7 75 ...
Page 360: ...7 MAINTENANCE 9 Re install all the covers guards and steps previously removed 7 122 ...
Page 417: ...7 MAINTENANCE Waste Handler WH models LEIL17WHL2020FA 2 7 179 ...
Page 436: ...8 SPECIFICATIONS 721G Loader Lift Arms Specifications LEIL16WHL0629FB 1 8 10 ...
Page 445: ...8 SPECIFICATIONS LEIL16WHL0629FB 4 8 19 ...
Page 461: ...8 SPECIFICATIONS LEIL16WHL0629FB 10 8 35 ...
Page 470: ...8 SPECIFICATIONS LEIL16WHL0629FB 13 8 44 ...
Page 480: ...8 SPECIFICATIONS 8 54 ...
Page 516: ...9 ACCESSORIES 9 36 ...
Page 520: ...Windows 3 86 Windshield washer fluid level Check 7 163 ...
Page 521: ......