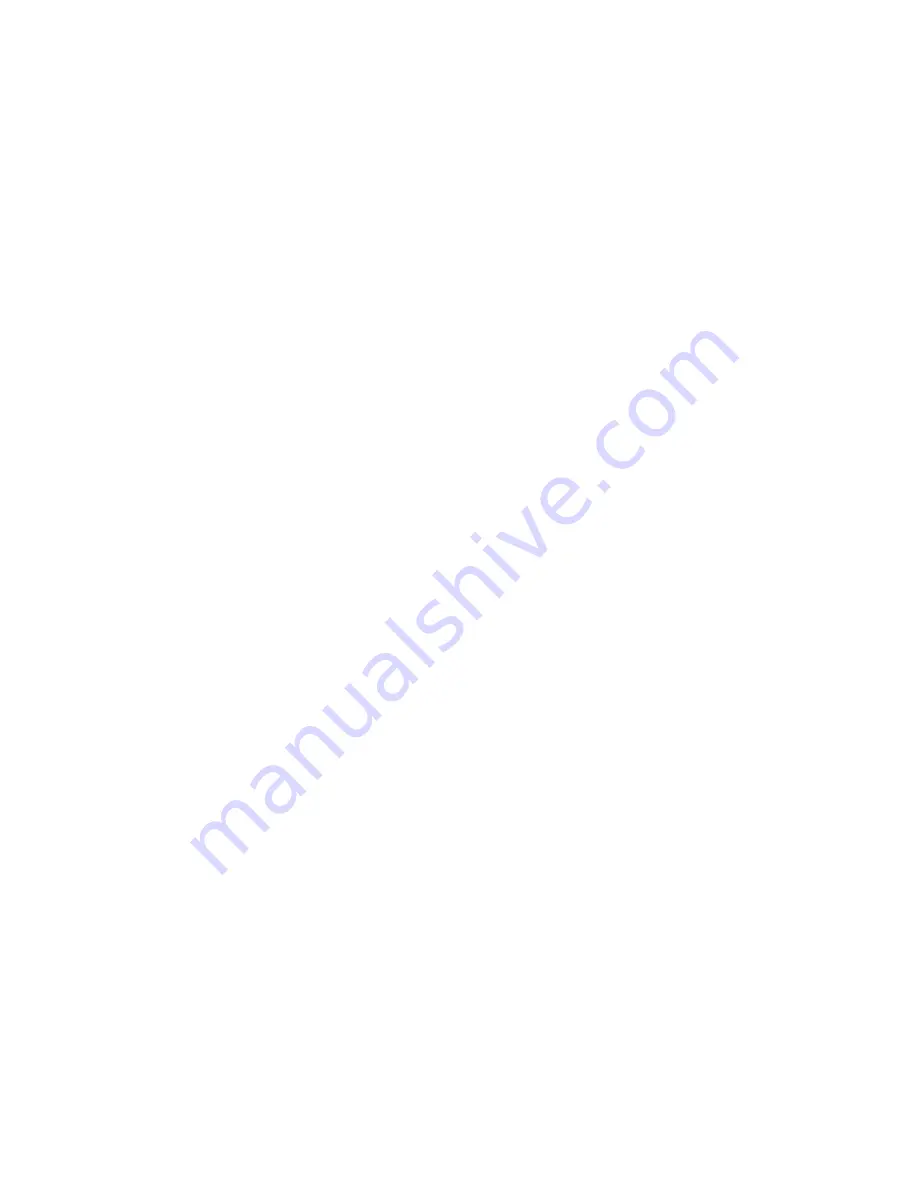
44
5. Using a suitable pump, add 2 litres of Polyolester oil to the
system (CARRIER SPEC: PP47-32). Make sure that the oil
level safety switch is NOT jumpered, and allow the unit to
re-start and run normally.
6. If low oil level problems persist, add another 1 or 2 litres of
oil. If it is necessary to add more than 4 litres of oil to the
system, then contact your Carrier distributor service
department.
CAUTION: When transferring the refrigerant charge to a
storage unit, oil may be carried along when the unit is not
operating. Reuse first of all the amount of refrigerant transferred.
After draining the oil, only recharge the amount drained (an
excess oil charge may impair correct unit operation).
If an oil draining or recovery operation becomes necessary, the
fluid transfer must be made using mobile containers.
12.8 - Integral oil filter change
An integral oil filter in the 06N screw compressor is specified to
provide a high level of filtration (3 µ) required for long bearing
life. As system cleanliness is critical to reliable system operation,
there is also a prefilter (7 µ) in the oil line at the oil separator outlet.
The replacement integral oil filter element part number is:
Carrier part number (including filter and O-ring): 06NA 660016S.
12.9 - Filter change-out schedule
The filter should be checked after the first 1000 hours of operation,
and every subsequent 4000 hours. The filter should be replaced at
any time when the pressure differential across the filter exceeds
2.1 bar.
The pressure drop across the filter can be determined by measuring
the pressure at the filter service port and the oil pressure port. The
difference in these two pressures will be the pressure drop across
the filter, check valve, and solenoid valve. The pressure drop across
the check valve and solenoid valve is approximately 0.4 bar, which
should be subtracted from the two oil pressure measurements to
give the oil filter pressure drop. The oil filter pressure drop should
be checked after any occasion that the compressor is shut down
on a low oil pressure safety.
12.10 - Filter change-out procedure
The following steps outline the proper method of changing the
integral oil filter.
1. Shutdown and lockout the compressor.
2. Manually force the operation of the oil solenoid valve, in order
to press the internal valve shutter onto its seat.
3. Close the oil filter service valve. Bleed pressure from the
filter cavity through the filter service port.
4. Remove the oil filter plug. Remove the old oil filter.
5. Prior to installing the new oil filter, “grease” the o-ring with
oil. Install the filter and replace the plug.
Before closing up the lube oil system, take the opportunity
to replace the prefilter, as well.
6. When complete, evacuate the filter cavity through the filter
service port. Open the filter service valve. Remove any
compressor lockout devices, the compressor is ready to return
to operation.
12.11 - Compressor replacement
12
.11.1 - Compressor rotation control
Correct compressor rotation is one of the most critical application
considerations. Reverse rotation, even for a very short duration,
damages the compressor.
The reverse rotation protection scheme must be capable of
determining the direction of rotation and stopping the compressor
within 300 milliseconds. Reverse rotation is most likely to occur
whenever the wiring to the compressor terminals is disturbed.
To minimize the opportunity for reverse rotation, the following
procedure must be applied. Rewire the power cables to the
compressor terminal pin as originally wired.
For replacement of the compressor, a low pressure switch is
included with the compressor. This low pressure switch should
be temporarily installed as a hard safety on the high pressure part
of the compressor. The purpose of this switch is to protect the
compressor against any wiring errors at the compressor terminal
pin. The electrical contact of the switch would be wired in series
with the high pressure switch. The switch will remain in place
until the compressor has been started and direction of rotation
has been verified; at this point, the switch will be removed.
The switch that has been selected for detecting reverse rotation
is Carrier part number HK01CB001. It is available as part of the
“Compressor installation package” (part No. 06NA 660 013).
This switch opens the contacts when the pressure falls below 6.8
kPa absolute. The switch is a manual reset type that can be reset
after the pressure has once again risen above 69 kPa relative. It is
critical that the switch be a manual reset type to preclude the
compressor from short cycling in the reverse direction.
Summary of Contents for 30HXC Series
Page 49: ......