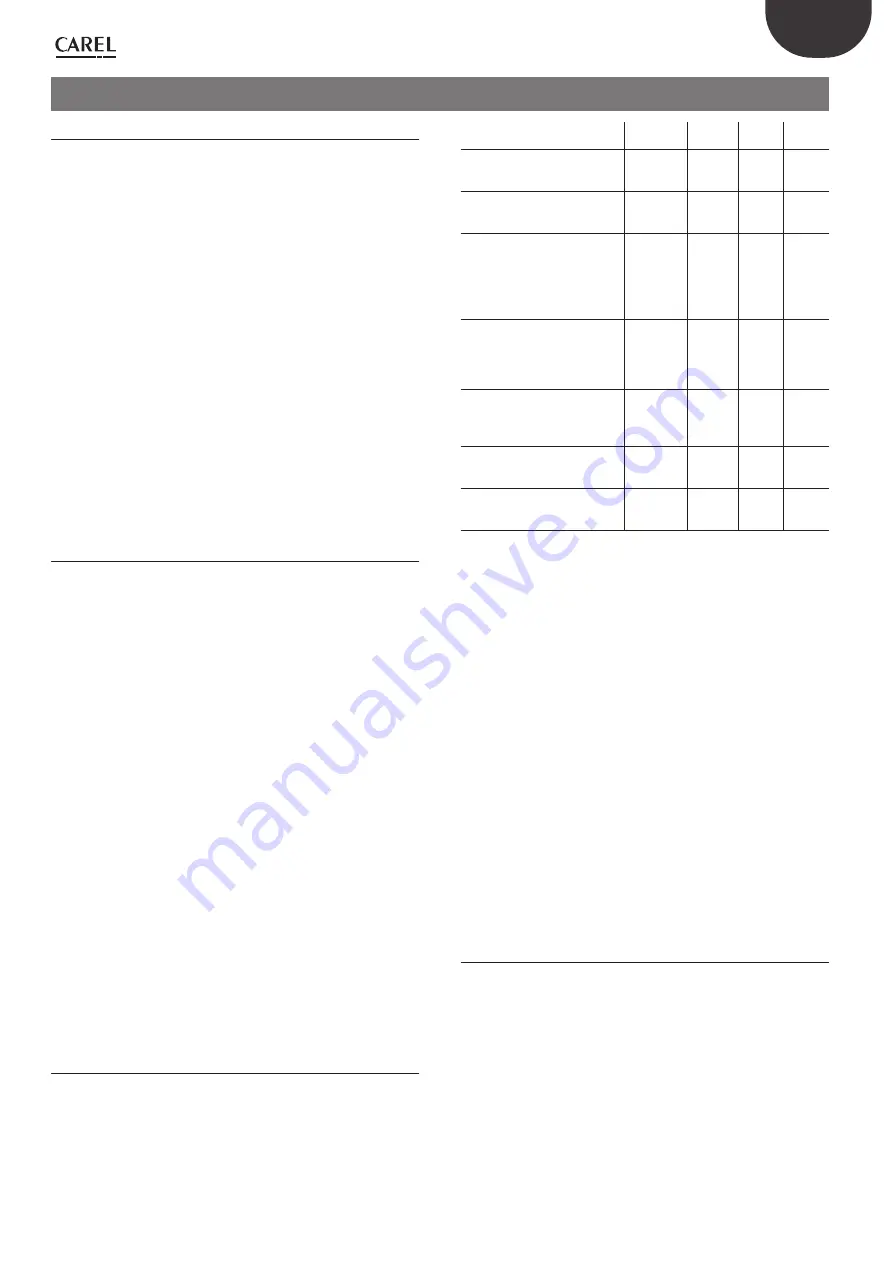
37
ENG
"humiFog direct" +0300073EN rel. 1.4 - 29.03.2022
13. MAINTENANCE
Activity
Action if
necessary
Weekly
3
months
6
months
Visual verifi cation of the absence
of biofi lm, algae, deposits, excess
of atomised water
Cleaning
and restora-
tion
X
Odour-free verifi cation
Cleaning
and restora-
tion
X
Screening test for the determi-
nation of the number of colonies
by dip slides according to VDI
6022-1, permissible threshold <
100 CFU/ml (incubation at 30°C
from 48 to 72 h)
Cleaning
and restora-
tion
X
Qualifi ed sample (Legionella <
100 CFU/100 ml; Pseudomonas
aeruginosa < 100 CFU/100
ml; total CFU at 20°C and 36°C
respectively < 150 CFU/ml)
Cleaning
and restora-
tion
X
Check for deposits around the
nozzle orifi ce
Nozzle
cleaning or
replace-
ment
X
Exhaust test
Cleaning
and restora-
tion
X
Humidity probe function test
and limit probe intervention test
if present
Restoration
X
Tab. 13.a
If the threshold values in the table are exceeded, the frequency of the
activity should be halved until stable results below the prescribed
threshold are obtained. Conversely, if the threshold values are met for at
least one year, the inspection intervals can be adapted gradually.
The detection of biofi
lm in equipment is always evidence of
microbiological contamination and consequent risk to human health.
This outcome is critical and necessarily requires the following immediate
actions:
1.
shutting down the system;
2.
removal of biofi lm by means of an appropriate cleaning technique;
3.
microbiological testing of the surface and disinfection, where the
result of the microbiological testing indicates contamination;
4.
determination of the cause of biofi lm formation;
5.
long-term elimination of the identifi ed cause;
6.
if the cause cannot be eliminated, the humidifi cation system must be
taken out of service.
It is possible to use the thermal disinfection technique in advance by
bringing the water to 70°C (158°F) and keeping it in the system for at
least 3 minutes. Only after proven microbiological contamination are
disinfection techniques and listed chemical disinfectants permitted (see
Robert Koch Institute website). The eff ectiveness of alternative techniques
must be verifi ed and demonstrable. The success of the disinfection
operation must be proven by appropriate microbiological tests.
13.2 Routine maintenance
Routine maintenance is recommended every three months, and mainly
involves visual inspection of correct operation of the main components.
The following is a list of recommended operations:
•
Check water inlet fi lter.
It is recommended to change the fi lter cartridge once every 6-12 months.
To change the cartridge, switch the unit off and close the feedwater
line. Empty the fi lter using the small tap at the bottom. Empty the fi lter
container through the small tap at the bottom. Remove the fi lter cartridge
inside and fi t a new one (P/N ECKFILT050). Tighten the holder, ensuring
that the O-ring is still in good condition to ensure tightness. Close the tap
under the holder and open the feedwater line.
13.1 Hygienic aspects
Hygiene measures are essential for the safe operation of the humidifi cation
system in order to protect the occupants of the building from health
risks. In principle, the requirements for air humidifi cation according
to VDI 6022-1 must be observed. All tests and measurements shall be
documented in a logbook available for inspection. The user is responsible
for compliance with local regulations and applicable guidelines. Any risk
must be identifi ed, including during installation and maintenance, by the
Health and Safety Manager, whose role it is to introduce appropriate and
eff ective control measures.
WARNING: If improperly maintained, the humidifi cation system and the
reverse osmosis system could develop the growth of microorganisms in
the pipes, including the bacteria responsible for Legionella, which would
then be spread into the environment through the aerosol produced by
the atomising nozzles of the blower units. Contaminants can settle on
surfaces, be inhaled by people or be distributed by ventilation systems.
Comply with the inspection schedules listed under "Hygiene measures".
WARNING: Do not keep the humidifi cation system and reverse osmosis
system disconnected for more than 48 hours. Without a power supply,
the system is unable to perform automatic fl ushes. Keep the factory-set
automatic fl ushes enabled on both the reverse osmosis unit and the
humiFog direct system. If it is necessary to shut down the system for
more than 48 hours by disconnecting the power supply, the procedure
described in the section "Shutting down the system" must be followed.
13.1.1 Shutting down the system
Whenever the humidifi cation system is shut down for more than 48
hours, the following steps are required:
emptying;
cleaning;
drying;
washing before service is restored.
Emptying is automatic thanks to the normally open solenoid valves
which, in the absence of power supply or after 48 hours with power
supply present, allow drainage by gravity. Make sure that the slopes of
the high-pressure pipes are such as to favour the discharge through
the appropriate solenoid valves. Disconnect the high-pressure hoses
connected to the pumping station and the blower units, check that there
is no residual water in them and empty them if necessary. The expansion
tank or the storage tank interposed between the reverse osmosis system
and the demineralised water inlet to the pumping station must be
emptied by opening the appropriate manual valve (#8 in the "Functional
diagram" chapter). Drain the water fi lter (#12 in the "Functional diagram"
chapter) at the pumping station inlet.
Cleaning shall be carried out manually or by physical means on surfaces
in contact with water, e.g. by hot water or compressed air, but not
chemically. Chemical disinfection is only permitted following proven
microbiological contamination and must be conducted by qualifi ed
personnel in accordance with VDI 6022-6:2018-01 Chapter 9 and any
subsequent additions. In such cases, disinfectants that do not pose a
health risk and do not promote the development of resistance must be
used. The tubes should be dried with compressed air. When the power
supply is restored for humidifi cation system start-up, humiFog direct will
run an automatic washing and fi lling cycle if enabled (see paragraph
"Washing"; factory default: enabled with duration 4 minutes).
13.1.2 Hygiene
measures
Below is the list of preventive hygiene checks and the frequency with
which they must be carried out, as provided by VDI 6022-6 guidelines and
applicable to the humiFog direct system.
Summary of Contents for DLAQ2DF100
Page 1: ...NO POWER SIGNAL CABLES TOGETHER READ CAREFULLY IN THE TEXT humiFog direct User manual...
Page 2: ......
Page 4: ...4 ENG humiFog direct 0300073EN rel 1 4 29 03 2022...
Page 42: ...42 ENG humiFog direct 0300073EN rel 1 4 29 03 2022 14 2 Two zone wiring diagram GA1 Fig 14 b...
Page 46: ......
Page 47: ......