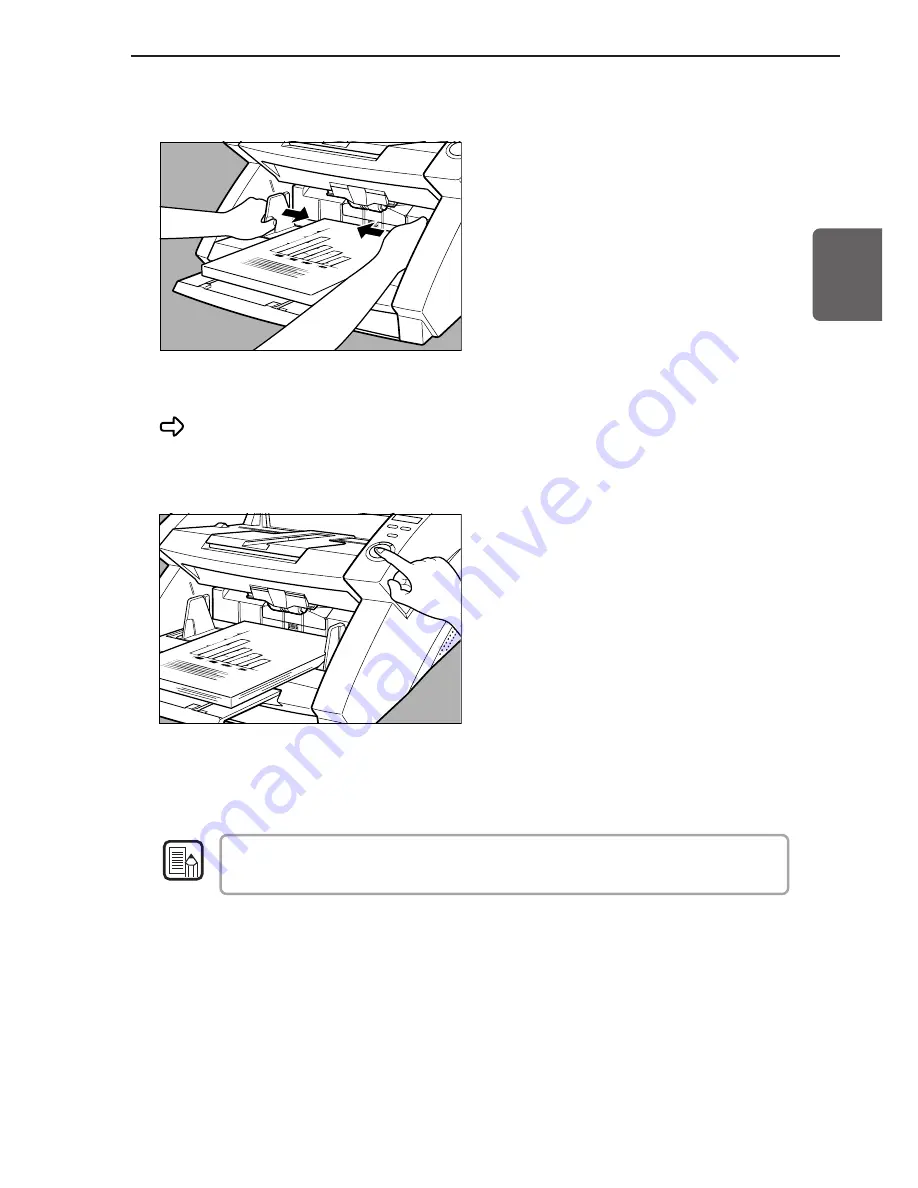
47
ENGLISH
4
Adjust the document guides to the width of the document.
5
Instruct scanning to start from the application.
The Start key changes color from red to green.
6
Press the [Start] key.
7
The document tray rises, and scanning begins. When scanning
ends, the document tray is lowered.
If paper feed stops during scanning due to a system error or paper jam, make sure
that the last page of the document was recorded properly before continuing to scan.
8
If there are more documents to scan, place the document and
press the [Start] key. To end scanning, press the [Stop] key.
Note
4.2 Document Feeding and Scanning
Summary of Contents for ImageFormula DR-9080C
Page 4: ......
Page 22: ......
Page 182: ......
Page 188: ...1003N0 0 1...
Page 195: ...COPYRIGHT 2003 CANON ELECTRONICS INC CANON DR 6080 9080C FIRST EDITION OCT 2003 vii...
Page 236: ......
Page 240: ......
Page 242: ...ix 1003N0 0 0...
Page 284: ...38 Chapter 3 Software Closing CapturePerfect 1 Select Exit from the File menu...
Page 308: ......
Page 352: ...1 Imprinter for DR 6080 9080C Installation Procedure IMS Product Planning Dept...
Page 355: ...4 3 Remove the left cover 4 screws Remove these screws x4...
Page 359: ...8 7 Insert it firmly to the back and fix it with 1 screw M3x6...
Page 366: ...15 14 Replace the cable to cable clamp and the document eject cover to the original position...