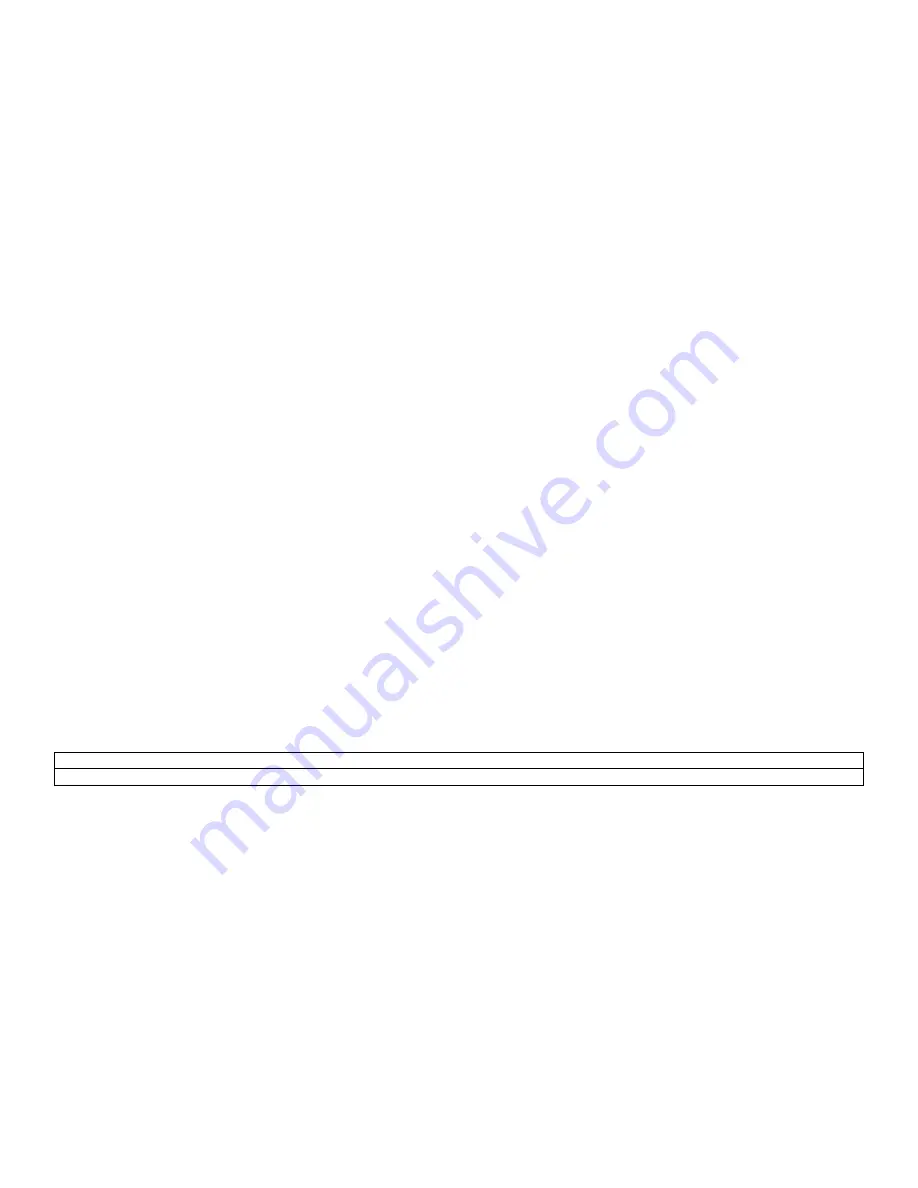
67
10.4
CONDENSATION TREATMENT
This high efficiency appliance may operate as a condensing appliance for extended periods of time based on return water temperatures.
Condensate occurs when the products of combustion are cooled below their dew point in the heat transfer process. The liquid condensate
formed from this high efficiency heat transfer process is mildly acidic. The condensate will typically have a pH ranging from 4.0 to 5.0 as
it is discharged from the condensate drain at the rear of the appliance. The neutralizer/condensate box, where condensate is collected,
is constructed from a corrosion resistant stainless steel and it contains neutralizer medium that must be replaced periodically. All materials
external to the appliance in contact with the condensate must be corrosion resistant. This is typically accomplished by using PVC or
CPVC plastic pipe and synthetic tubing. Condensate must be able to flow freely from the appliance. All condensate flow is accomplished
by gravity requiring a minimum downward slope of ¼” per foot (21 mm/m) to ensure proper flow to the condensate management system
and/or a suitable drain. The neutralizer condensate box
MUST
always be mounted lower than the bottom of the appliance cabinet. This
can be achieved by placing the boiler on a concrete pad and placing the neutralizer condensate box on the floor. All condensate piping
and connections must be easily accessible for routine maintenance and inspection.
10.4.1 CONDENSATE VOLUME
There are several factors affecting the amount of condensation created by the appliance however for rough approximation, the following
formula can be used: Condensation Volume, US Gallon/Hr = Input, MBH/1000 x 5.0.
Many codes will require the acidic condensate to be neutralized before it can be placed in a drain system. An additional supplementary
neutralizer to control the pH of the liquid discharged to a drain system is recommended with every appliance. The neutralizer consists of
an industrial grade, non-corrosive reservoir for additional treatment of the condensate. As the reservoir fills, it provides an extended
residency time to neutralize the condensate. The neutralized condensate exits from the reservoir outlet. The neutralizer/ condensate box
supplied with the Avenger provides a ‘P’ trap to prevent flue gas escape as well as initial neutralization of the condensate.
When the condensate level in the reservoir rises to the drain, it spills out into the condensate bin and from there exits to the external
neutralizer. As the pH number increases in numerical value, the relative acidity of the discharge decreases. The neutralized condensate
may then be discharged into a suitable drain system without fear of damaging the drain system. Always check with local codes for specific
pH requirements. Neutralizers may be used in series to raise pH.
10.5
BURNER MAINTENANCE
The burner should be removed for inspection and cleaning on an annual basis. An appliance installed in a dust or dirt contaminated
environment will require inspection and cleaning on a more frequent schedule. The fan assisted combustion process may force airborne
dust and dirt contaminants, contained in the combustion air, into the burner. With sustained operation, non-combustible contaminants
may reduce burner port area, reduce burner input or cause non-warrantable damage to the burner.
Airborne contaminants such as dust, dirt, concrete dust or dry wall dust can be drawn into the burner with the combustion air and block
the burner port area. An external combustion air filter is recommended to be used with the appliance. This filter should be checked and
cleaned at the time of appliance commissioning and on a six-month interval or more often in a contaminated environment.
10.5.1 BURNER REMOVAL
NOTE
Check torque on fan mounting nuts using a torque wrench. AR1000-AR4000: 25 lb-ft
Access to the burner will require the following steps:
•
Turn off main electrical power to the appliance.
•
Turn off main manual gas shutoff to the appliance.
•
Remove the top covers and top side panels.
•
Disconnect the gas supply connection to the fan inlet.
•
Disconnect the fan motor power wires at the harness.
•
Remove the Hot Surface Igniter and the UV Scanner.
•
Remove the sensing tubes from the air ratio gas valve to the combustion air fan.
•
Remove the nuts holding the fan assembly to the heat exchanger and remove the fan assembly. On occasion the red silicone gasket
may adhere to the underside of the fan’s flange. Carefully pry the flange away from the gasket prior to removing the fan assembly.
•
The burner can now be lifted vertically out of the heat exchanger cavity. A graphite backed ceramic paper gasket is located directly
under the burner flange. This gasket must be replaced if it is damaged. A solid black graphite gasket sits directly on the heat
exchanger top plate.
•
Use care to prevent damage to the knitted metal fiber of the burner surface.
•
Check all gaskets and replace as necessary. Gaskets affected by heat will not reseal properly and must be replaced.
•
Replace the burner in the reverse order that it was removed. Insert the igniter and UV Scanner before doing the final tightening on
the fan mounting nuts. Evenly tighten the nuts to 25 ft-lbs.
Summary of Contents for Avenger Series
Page 2: ......
Page 35: ...30 Figure 21 Recommended Piping with Reverse Return and Variable Primary Flow...
Page 84: ...79 Figure B BLOWER BURNER ASSEMBLY...
Page 87: ...82 Figure C TYPICAL GAS TRAIN AR1000 AR3000 Figure D TYPICAL GAS TRAIN AR3500 AR4000...
Page 89: ...84 Figure E CONTROL BOARD ASSEMBLY...
Page 92: ...87 PART 13 ELECTRICAL DIAGRAMS...
Page 93: ...88...
Page 94: ...89...
Page 95: ...90...
Page 96: ...91...
Page 97: ...92...
Page 98: ...93...
Page 99: ...94...
Page 100: ...95...
Page 101: ...96...
Page 102: ...97...
Page 103: ...98...
Page 104: ...99...
Page 105: ...100...
Page 106: ...101...