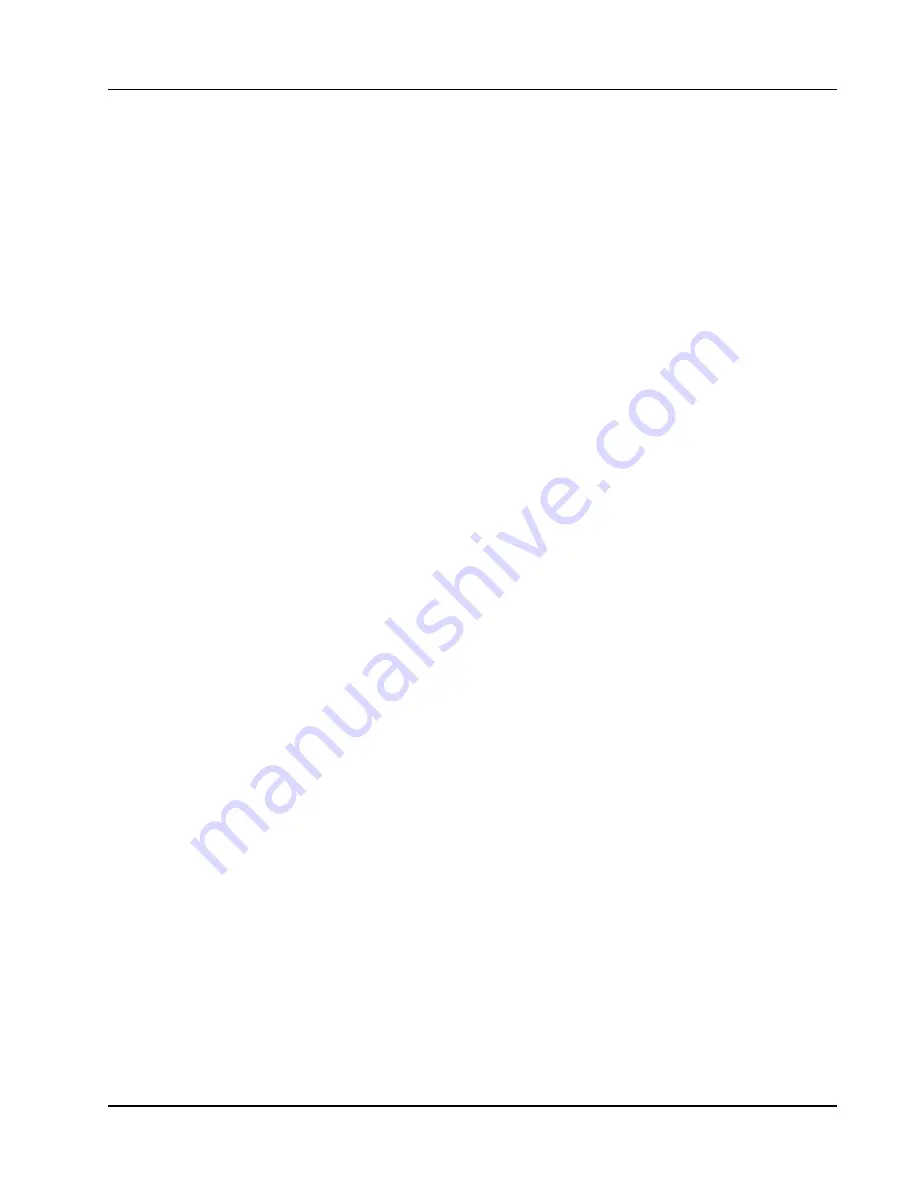
C-11
Scanner
®
2000 microEFM
Appendix C
The Resource State parameter shows the status of the hardware. If the hardware is working as designed, the
status is displayed as “online.” If the resource block is placed in OOS mode, the status will be “Standby.” If a
hardware failure occurs, the resource state will be “Failure.”
By selecting the Restart parameter, a user can restart the control strategy. Additional selections allow a restart
without changing the configuration, a restart after resetting parameters to default values, or a reset of the CPU.
During normal operation, this parameter is displayed as “Run.”
Transducer Block
The transducer block is an interface between the Scanner 2000 sensor and the device’s analog input function
blocks. It is responsible for reading the measurements of process variables such as pressure, temperature,
or flow rate from Modbus
®
registers and making the varaiables available for selection as analog inputs in a
fieldbus network.
Like the resource block, the transducer block has no input or output parameters and cannot be linked to
another block. However the transducer block does interface with function blocks over input/output hardware
channels to enable the use of process variable values in process control strategies. Additionally, the transducer
block contains parameters that can be used to provide various Modbus
®
data such as input measurements,
flow volumes, and other Modbus
®
calculations to a fieldbus host.
Automatic is the normal operating mode of the transducer block. In some cases, the transducer block must be
placed in OOS mode to allow a configuration change to be made without affecting ongoing processes.
Analog Input (AI) Function Blocks
The analog input (AI) function blocks access a process variable measurement through a hardware channel
from a transducer block. Various types of function blocks may be linked together to create control strategies.
The input block may process the input value before it makes it available to other function blocks for output.
At a minimum, the user must enter the following parameter settings when configuring an AI block:
• mode parameter (target)
• assignment of AI block to a channel (defines the process variable measurement that will be used as input
to the AI block)
•
linearization method
•
value range for input and output values
•
engineering unit for output values, if required
An AI function block is typically set in Auto mode and never changed.
The output value from the AI block is in engineering units and contains a status parameter indicating the
quality of the measurement.
Device Identification
When the Scanner 2000 is connected to a fieldbus network, it is typically detected automatically by the host
system. The host can use any of the following methods to identify the Scanner 2000:
•
Device ID
• Physical Device (PD) tag
•
Node address
Summary of Contents for Scanner 2000 microEFM
Page 1: ...NUFLO Scanner 2000 microEFM Hardware User Manual Manual No 9A 30165023 Rev 10 ...
Page 26: ...26 Section 1 Scanner 2000 microEFM ...
Page 104: ...A 18 Appendix A Scanner 2000 microEFM ...
Page 106: ...B 2 Appendix B Scanner 2000 microEFM ...