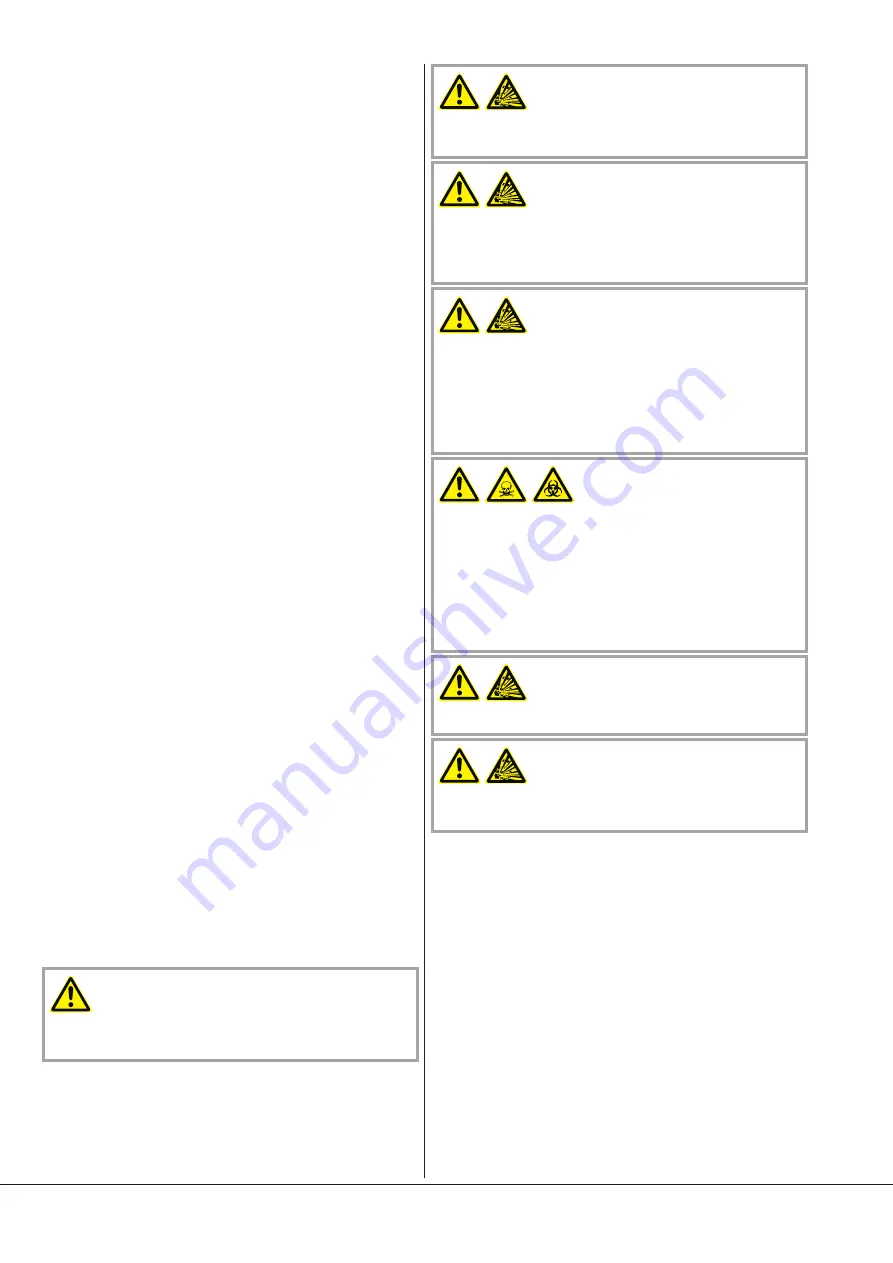
Maintenance
Procedure for calibration of monitoring
devices
Procedure A
Dismount the PT100 probe and check it with a calibrated oven or send
the probe to an approved laboratory for inspection.
Reassemble the probe on the pump after checking.
Procedure B
Dismount the pressure sensor and check it by comparing it with a cali-
brated pressure sensor or send the sensor to an approved laboratory for
inspection. Reassemble the probe on the pump after checking.
Procedure C
Dismount the pressure switch and check it by comparing it with a cali-
brated pressure sensor or send the sensor to an approved laboratory for
inspection. The pressure switch must trip at the prescribed alarm value
when the pressure increases. Reassemble the probe on the pump after
checking.
Procedure D
Remove the vibration sensor from the pump and get it calibrated by a lo-
cal calibration service.
Alternatively you can return the sensor for calibration to:
Monitran Ltd
Monitran House
33 Hazlemere Road
Penn
HP10 8AD
UK
[email protected]
Use an Analog Current Loop Simulator and Tester 4-20mA to test the re-
maining control loop.
Compare and record the trip value, see table alarm values.
After test of the control loop and calibration of the transmitter, mount
the transmitter back on the pump.
Procedure E
Check that the inductive contact changes state when the ball of the
flowmeter is passing without disassembling the flowmeter or its switch.
Procedure F
Check that the solenoid valve changes state by electrical supply. Visual
inspection of the solenoid valve sealing by means of the flow meter.
Procedure G
Check that the solenoid valve changes state by electrical supply. Visual
check of the sealing at the outlet of the solenoid valve (no liquid
passing).
Maintenance
General information
CAUTION
Information on the maintenance of the pump can be found in the en-
closed installation and operating manual of the COBRA NC 0100 ...
0300 B.
Please also refer to the following remarks and maintenance
prescriptions :
WARNING
After the start-up, the vacuum pump has to be controlled everyday
regarding any noise appearance. In such a case, immediately stop the
pump, see “Troubles shooting”.
WARNING
The barrier gas supply of the seal has to be checked every week, if
this is not automatically controlled by a flow meter. The barrier gas
quantity for the sealing systems 1 and 2 should be 2.5 to 3 l/min,
see the Instruction and Operating manual COBRA NC 0100 ... 0300
B.
WARNING
The inside of the vacuum pump should be regularly controlled regar-
ding the deposit formation and if so to suppress, e.g. by the pump
flushing. The formation of deposit can provoke some friction and
spark formation in the pump, which has to be imperatively avoided.
Explosion danger !
Control possibility exists at the vacuum pump inlet and outlet. The
use of an endoscope for better control is recommended.
DANGER
Any servicing on the pumps must only be done by specially trained
servicing staff under strict adherence of current and valid safety re-
gulations. In the event of possible risks from dangerous substances
of any kind, the user of the pump must duly inform and instruct
maintenance staff before any work is carried out.
Before any maintenance work is carried out, any risk to the health of
maintenance personnel that could come from pumped substances (or
any other substances) from both within the pump or outside, must
be removed.
WARNING
The opening of the vacuum pump is only authorized after it’s come
to a full stop and in the total absence of any explosive atmosphere.
WARNING
Bearing exchange - The bearings have to be exchanged every 16’000
running hours, because a bearing breakdown will increase the explo-
sion danger.
The
coupling
has to be maintained according to the manufacturer ser-
vice prescriptions.
In accordance with the Instructions and Operating Manual of the
COBRA NC 0100 ... 0300 B, the following servicing may be carried out:
l
Checking and cleaning of the water cooling pipe-work
l
Changing lubrication and cooling oils
l
Changing or fill up the cooling liquid (evaporation cooling)
l
Checking, cleaning or changing the air filter of the flushing device
l
Cleaning the external parts such as fan cover and cooler
Other work such as dismantling or rebuilding jobs as well as repair and
maintenance work may only be carried out by BUSCH customer service
engineers.
All
cleaning works
have to be executed with a humid rag in order to
avoid any electrostatic charge and sparks discharge.
The
electrical installation
is to check every 4’000 running hours regar-
ding the function and the damage. This also includes the vacuum pump
control and the potential compensation.
Maintenance
Seite/ Page/ Page 20