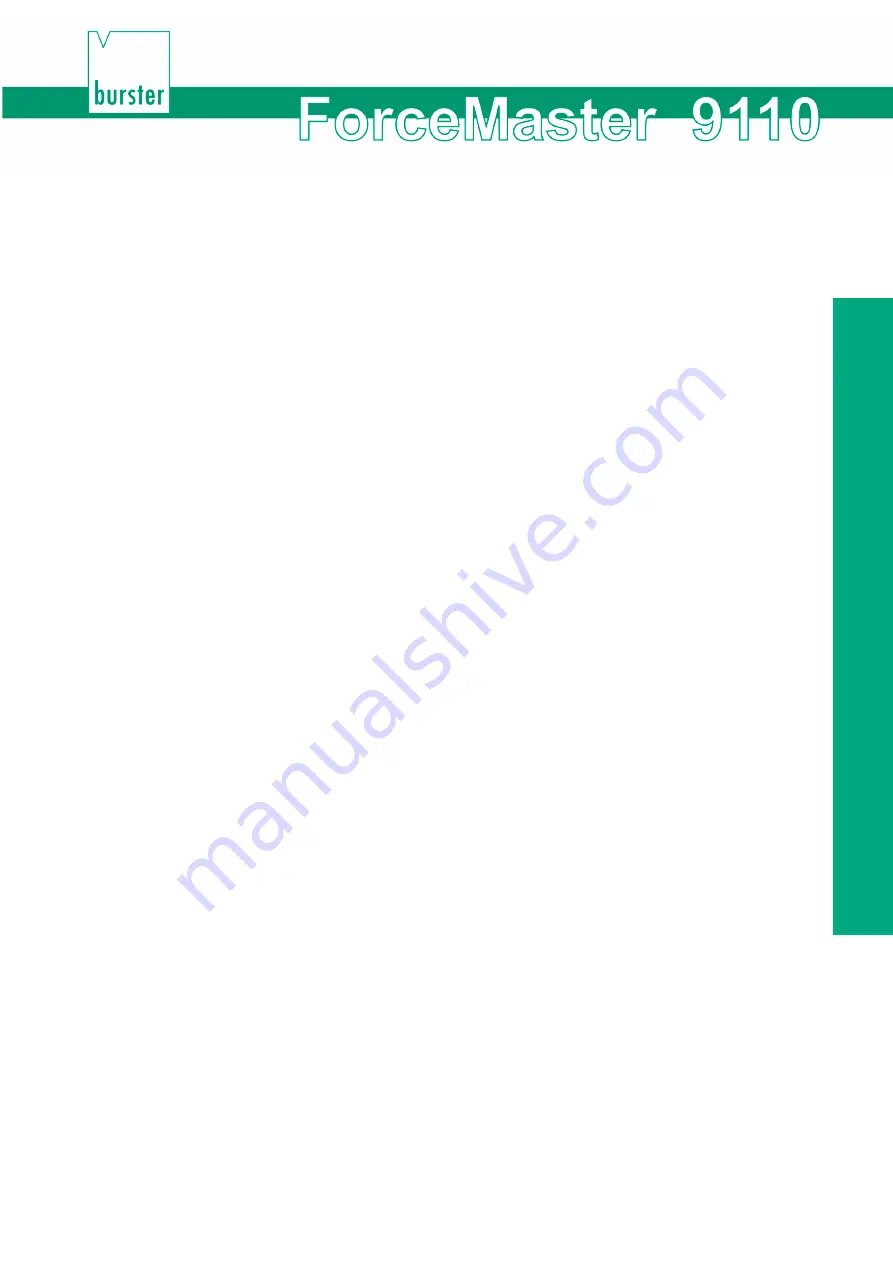
45
of 95
In
iti
al
c
om
m
is
si
on
in
g
It may be necessary to correct the values learnt through the autoconfiguration. If necessary, these
can be manually adjusted – see Section 3.11.3.
Summary of Contents for ForceMaster 9110
Page 3: ......
Page 4: ...4of 95...
Page 8: ...8of 95...
Page 16: ...16of 95 Menu structure of the ForceMaster 9110 3 10 Menu structure of the ForceMaster 9110...
Page 17: ...17of 95 Device concept...
Page 18: ...18of 95 Menu structure of the ForceMaster 9110...