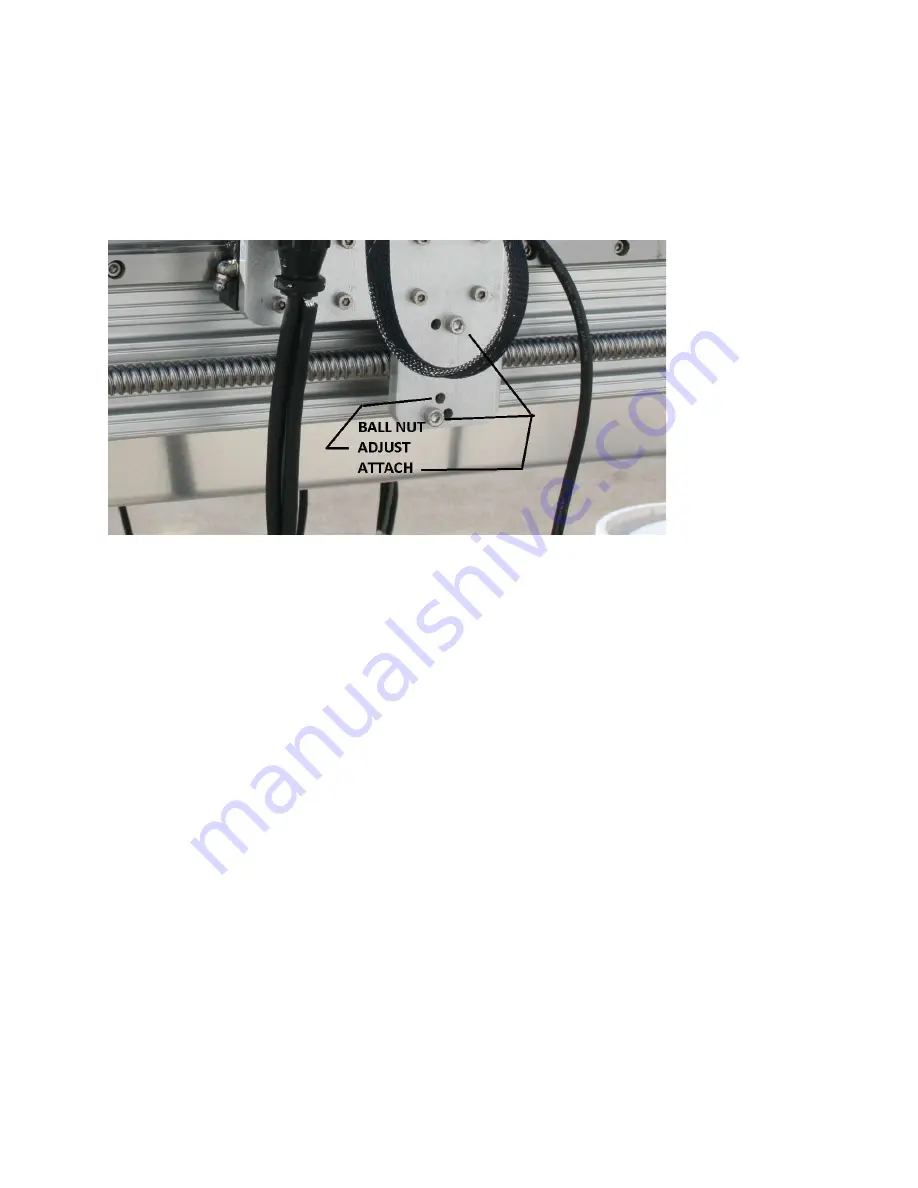
38
backlash, a clunking sound will be heard. Make sure the ball nut mount screws are
tight. The adjust screw is located between the mount screws and uses a 3mm Allen
wrench. Tighten slightly until clunking sound disappears. Traverse the axis end to end
and listen for any unusual sounds or binding. Some areas of the lead screw may be
slightly tighter than others. The ball nut needs to be adjusted for the tightest location.
The picture shows the X2 axis, but the X1 axis and Y axis have a similar arrangement.
Caution! Over tightening the ball nut adjusting screw will destroy the ball nut
ADJUST LEAD SCREW BACKLASH:
This adjustment preloads the lead screw bearings.
The Panel Pro 6126 X and Y axis are similar. They use a double bearing at the motor
end and a floating bearing at the knob end. The knob end has two Bellville washers
that the knob tightens against with the screw in the middle of the knob. This eliminates
backlash with constant preload on the bearings. The pointed end of the Bellville
washers should oppose each other, one end pointed to the flange bearing, and the
other to the knob.
Hold the lead screw (on the screw part, not the smooth machined part) with pliers near
nut end. Loosen the ¼ x 20 stop nut from the knob.
The knob is threaded. The knob should be tightened about ¼ to 3/8 of a turn beyond
the point where the knob contacts the belleville washers.
Tighten the jamnut make sure the knob to ballscrew position does not shift while
tightening the jam nut
STORAGE
Make a habit of covering the Panel Pro after use. Keep the ways clean and oiled with
LPS2. For long term storage coat the steel parts with a preservative oil like LPS3.