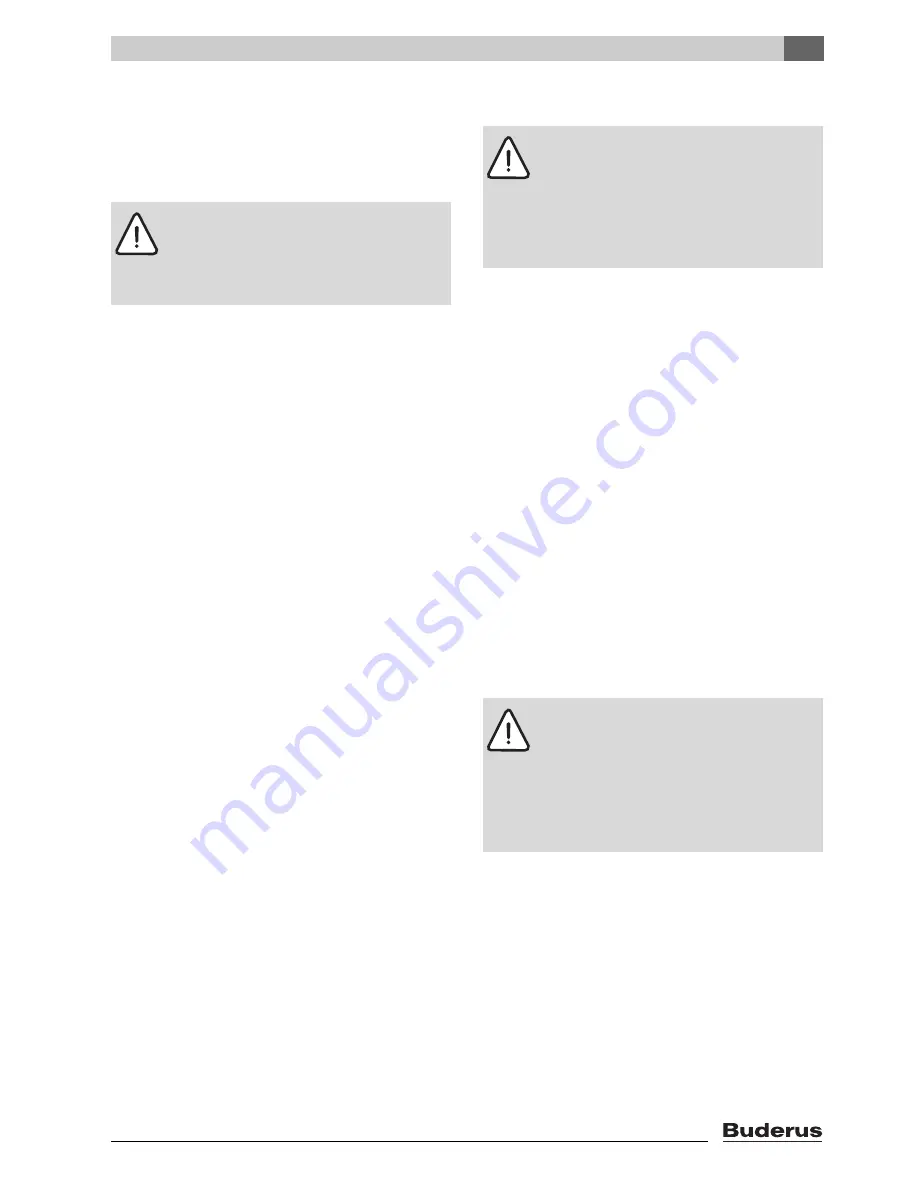
9
Heating system servicing
Logano plus GB312 - Technical specifications are subject to change without prior notice
67
9.7
Checking gas valve for leaks
The purpose of this procedure is to check the solenoid
valves in the gas valve for leaks. The test should only be
carried out by trained and experienced service techni-
cians when servicing or replacing the gas valve.
V
Disconnect the boiler from the electrical power supply
and unplug the power plug from the gas valve.
V
Turn off the gas isolating valve A on the back of the
boiler.
V
Make sure that the manual isolating valve E on the test-
ing apparatus (
Æ
Fig. 67, page 68) is turned off.
V
To test the 1st solenoid valve (B), remove the blanking
plug P from the gas valve and fit a testing nipple.
V
Turn on the isolating valve A to pressurize the 1st sole-
noid valve (B).
V
Hold the end of a testing tube with a 1/4 inch internal
diameter 1/2 inch below the surface in a glass of water.
V
Slowly turn on the manual isolating valve E on the test-
ing apparatus.
V
Once a stable flow of bubbles is escaping from the
testing tube, the number of bubbles in the space of 10
seconds must be counted. The permissible number of
bubbles is 6 (equates to 0.008 ft
3
/h) for boiler sizes
90-4 to 240-7, and 7 (equates to 0.01 ft
3
/h) for boiler
size 280-8.
V
Turn off the gas isolating valve A on the back of the
boiler again.
V
Remove the testing nipple from testing point P and
carefully refit and seal the blanking plug using an
appropriate sealant.
V
To test the 2nd solenoid valve (C), remove the blanking
plug from testing point 4 on the gas valve outlet flange
and fit a testing nipple.
V
Turn off the gas isolating valve D downstream of the
gas valve.
V
Remove the blanking plug from testing point 3 on the
gas valve and fit a testing nipple. Connect the hand
pump G, which is part of the testing apparatus, and
connect a pressure tester H (
Æ
Fig. 67, page 68).
Carefully build up a testing pressure of 7 inches W.C.
using the hand pump H and then turn off the isolating
valve F on the testing apparatus.
V
Hold the end of a testing tube with a 1/4 inch internal
diameter 1/2 inch below the surface in a glass of water.
V
Slowly turn on the manual isolating valve E on the test-
ing apparatus.
V
Once a stable flow of bubbles is escaping from the
testing tube, the number of bubbles in the space of 10
seconds must be counted. The permissible number of
bubbles is 6 (equates to 0.008 ft
3
/h) for boiler sizes
90-4 to 240-7, and 7 (equates to 0.01 ft
3
/h) for boiler
size 280-8.
V
Remove the testing nipples from testing points 3 and 4
and carefully refit and seal the blanking plugs using an
appropriate sealant.
After completing the test, proceed as follows.
V
Ensure that the gas isolating valve D on the outlet side
of the gas valve is closed.
V
Reconnect the power plug to the gas valve and switch
on the power supply to the boiler again.
V
Turn on the gas isolating valve A on the back of the
boiler again.
V
Switch on the boiler and run the burner 1 start
sequence.
V
Check all joints on the gas valve for leaks using a suit-
able leak detecting agent. Turn on the gas isolating
valve D on the outlet side of the gas valve again. Reset
the boiler to normal operating mode.
Danger:
Risk of fatal injury from electric cur-
rent.
V
Disconnect boiler from the mains electric-
ity supply.
V
Unplug the power plug for the gas valve.
Caution:
Risk of burner damage due to ex-
cessive pressure when testing for leaks.
The gas pressure regulator and other gas
valve components can be damaged if the
testing pressure is too high.
V
On no account use a higher testing pres-
sure than 7 inches W.C.
Caution:
Risk of system damage due to
short-circuits.
V
Cover the fan and other at-risk areas be-
fore searching for leaks.
V
Do not spray leak detector onto cable
conduits, plugs or electrical connecting
leads. Do not allow it to drip onto them ei-
ther.