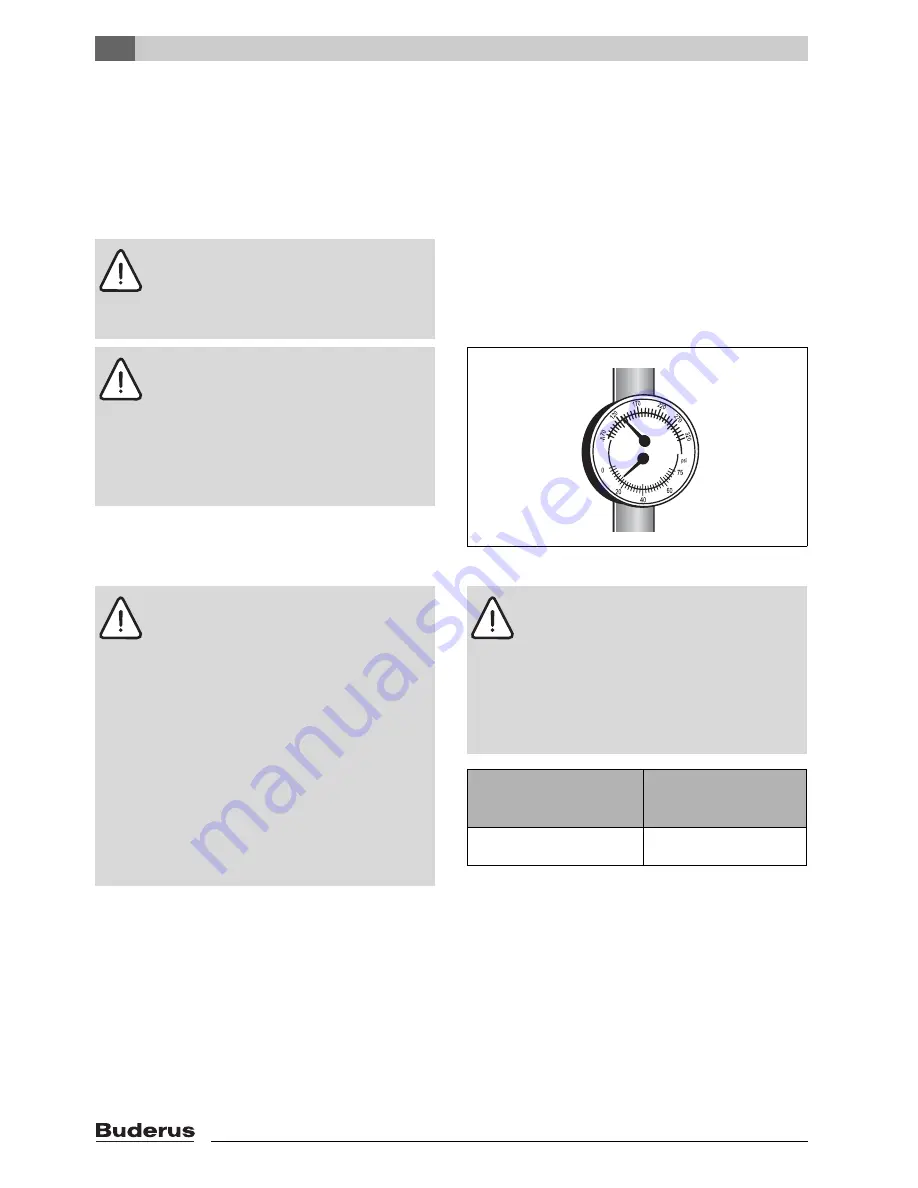
6
Installing the boiler
Logano plus GB312 - Technical specifications are subject to change without prior notice
34
6.10 Filling the heating system and
checking for leaks
To ensure that leaks do not occur when the system is in
operation, check for leaks before commissioning the heat-
ing system. Pressurize the heating system with a pressure
equal to the response pressure of the pressure relief
valve.
V
Carry out the leakage test according to the local regu-
lations.
Fig. 28 Pressure/temperature gauge
V
Open the mixing and shut-off valves on the heating
water (primary) side.
Caution:
Risk of system damage due to
scale formation in the boiler.
V
Refer to the information provided in the
"Water quality requirements for Logano
plus GB312" manual.
Caution:
Risk of system damage due to ex-
cess pressure when testing for leaks.
Pressure, control and safety equipment may
be damaged by excessive pressure.
V
When you carry out a leakage test, make
sure that no pressure, control or safety
equipment that cannot be isolated from
the boiler water chamber is fitted.
7 747 010 720-24.2RS
Caution:
Risk of damage to system
If you fill the heating system when it is hot, the
resulting temperature stresses can cause
stress cracks. The boiler will then leak.
V
Only fill the heating system when cold (the
flow temperature should be no more than
104 °F).
V
When the heating system is in operation,
do not fill it via the boiler fill & drain valve.
Instead, use the filler valve in the heating
system pipework (return).
V
Pay attention to the water quality as spec-
ified in the "Water quality requirements for
Logano plus GB312" manual, and record
the volume and quality of the water used
to fill the system.
Caution:
Risk of system damage due to un-
suitable heating system water.
V
Pay attention to the quality of the water
used to fill the heating system. Poor water
quality can damage heating systems due
to scale formation and corrosion. For fur-
ther details, please see the accompanying
"Water quality requirements for Logano
plus GB312" manual.
Maximum operating
pressure
Maximum testing pres-
sure
[psi]
[psi]
50
with the pressure
relief valve supplied
75