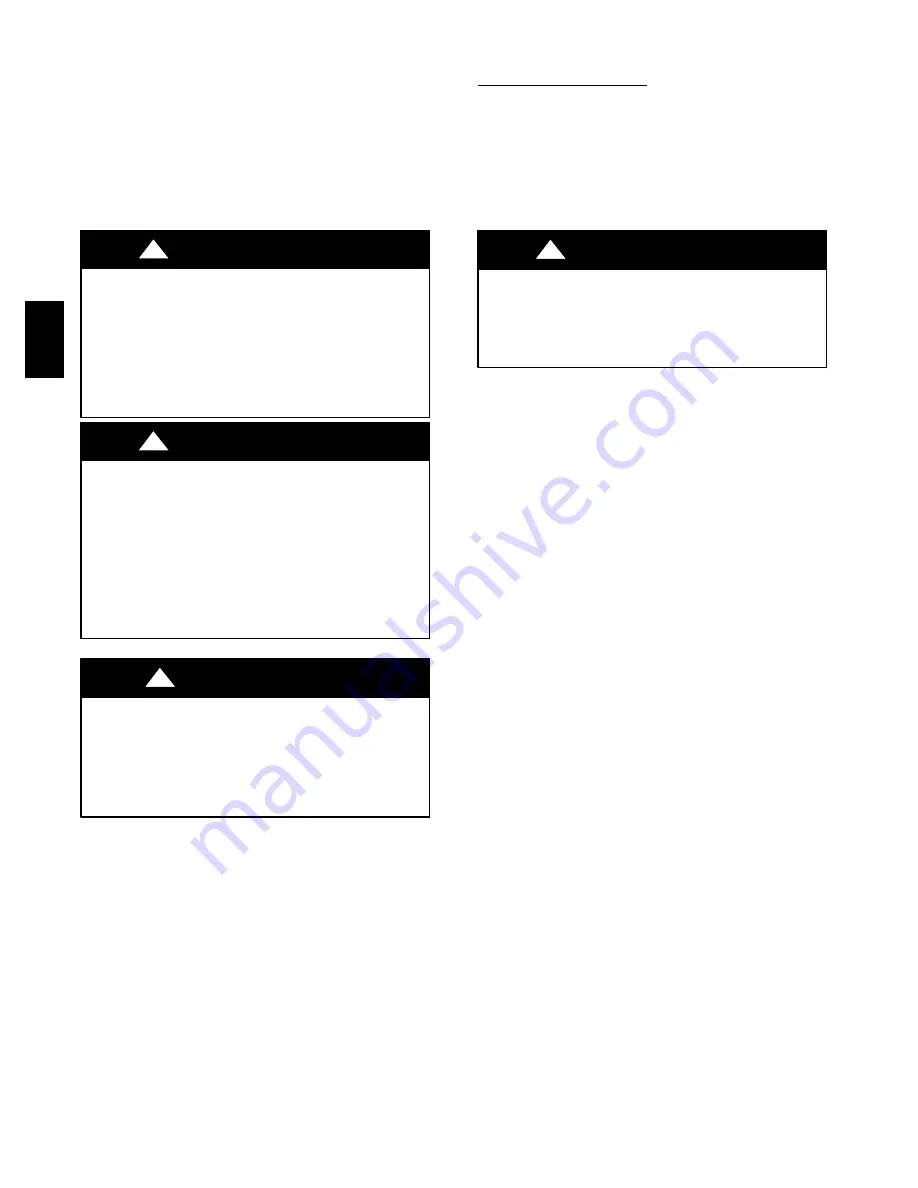
18
NOTE
:
Unit will remain in defrost until defrost thermostat
reopens at approximately 65
_
F (18
_
C) coil temperature at liquid
line or remainder of defrost cycle time.
MAINTENANCE
To ensure continuing high performance, and to minimize the
possibility of premature equipment failure, periodic maintenance
must be performed on this equipment. This heat pump unit should
be inspected at least once each year by a qualified service person.
To troubleshoot unit, refer to Table 8.
NOTE
: TO EQUIPMENT OWNER: Consult your local dealer
about the availability of a maintenance contract.
PERSONAL INJURY AND UNIT DAMAGE HAZARD
Failure to follow this warning could result in personal injury
or death and unit component damage.
The ability to properly perform maintenance on this
equipment requires certain expertise, mechanical skills, tools
and equipment. If you do not possess these, do not attempt to
perform any maintenance on this equipment, other than those
procedures recommended in the Owner’s Manual.
!
WARNING
ELECTRICAL SHOCK HAZARD
Failure to follow these warnings could result in personal
injury or death:
1. Turn off electrical power to the unit and install a lockout
tag before performing any maintenance or service on this
unit.
2. Use extreme caution when removing panels and parts.
3. Never place anything combustible either on or in contact
with the unit.
!
WARNING
UNIT OPERATION HAZARD
Failure to follow this caution may result in improper
operation.
Errors made when reconnecting wires may cause improper
and dangerous operation. Label all wires prior to
disconnecting when servicing.
CAUTION
!
The minimum maintenance requirements for this equipment are as
follows:
1. Inspect air filter(s) each month. Clean or replace when
necessary.
2. Inspect indoor coil, drain pan, and condensate drain each
cooling season for cleanliness. Clean when necessary.
3. Inspect blower motor and wheel for cleanliness each
cooling season. Clean when necessary.
4. Check electrical connections for tightness and controls for
proper operation each cooling season. Service when
necessary.
Step 1 — Air Filter
IMPORTANT
: Never operate the unit without a suitable air filter
in the return--air duct system. Always replace the filter with the
same dimensional size and type as originally installed. See Table 1
for recommended filter sizes.
Inspect air filter(s) at least once each month and replace
(throwaway--type) or clean (cleanable--type) at least twice during
each cooling season and twice during the heating season, or
whenever the filter becomes clogged with dust and lint.
Indoor Blower and Motor
NOTE
: All motors are pre--lubricated. Do not attempt to lubricate
these motors.
NOTE
: 460 volt units have a stepdown autotransformer that
supplies approximately 230 volts to a nominal 230 volt indoor
blower motor.
For longer life, operating economy, and continuing efficiency,
clean accumulated dirt and grease from the blower wheel and
motor annually.
ELECTRICAL SHOCK HAZARD
Failure to follow this warning could result in personal injury
or death.
Disconnect and tag electrical power to the unit before cleaning
the blower motor and wheel.
!
WARNING
To clean the blower motor and wheel:
1. Remove and disassemble blower assembly as follows:
a. Remove unit access panel.
b. Disconnect 5 pin plug and 4 pin plug from indoor
blower motor.
c. On all units remove blower assembly from unit.
Remove screws securing blower to blower partition and
slide assembly out. Be careful not to tear insulation in
blower compartment.
d. Ensure proper reassembly by marking blower wheel and
motor in relation to blower housing before disassembly.
e. Loosen setscrew(s) that secures wheel to motor shaft,
remove screws that secure motor mount brackets to
housing, and slide motor and motor mount out of
housing.
2. Remove and clean blower wheel as follows:
a. Ensure proper reassembly by marking wheel orientation.
b. Lift wheel from housing. When handling and/or
cleaning blower wheel, be sure not to disturb balance
weights (clips) on blower wheel vanes.
c. Remove caked--on dirt from wheel and housing with a
brush. Remove lint and/or dirt accumulations from
wheel and housing with vacuum cleaner, using soft
brush attachment. Remove grease and oil with mild
solvent.
d. Reassemble wheel into housing.
e. Reassemble motor into housing. Be sure setscrews are
tightened on motor shaft flats and not on round part of
shaft.
f. Connect 5 pin plug and 4 pin plug to indoor blower
motor.
g. Reinstall unit access panel.
3. Restore electrical power to unit. Start unit and check for
proper blower rotation and motor speeds during cooling
cycles.
607C
Summary of Contents for 607C024
Page 4: ...4 A08084 Fig 2 607C024 030 Unit Dimensions 607C...
Page 5: ...5 A08085 Fig 3 607C036 060 Unit Dimensions 607C...
Page 12: ...12 A08024 Fig 12 Wiring Schematics 208 230 1 60 607C...
Page 13: ...13 A08025 Fig 13 Wiring Schematics 208 230 3 60 607C...
Page 14: ...14 A08026 Fig 14 Wiring Diagram 460 3 60 607C...