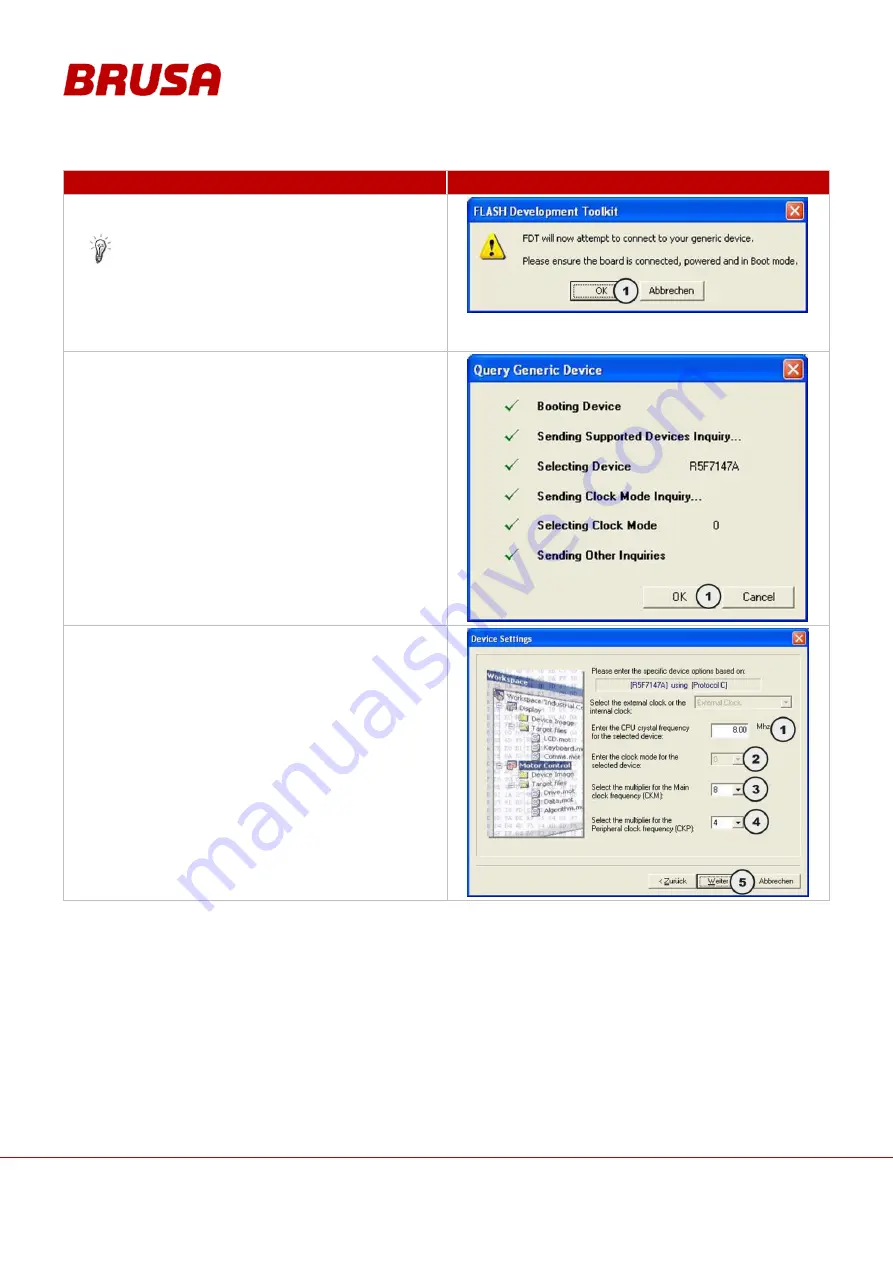
Technical data
and start-up
EVB1-350/400-40-HP
86
PROCEDURE STEP
ILLUSTRATION / OTHER INFORMATION
7.
Check the instructions in the dialogue box which
appears. Press the
OK
button (1).
The battery is now in
Boot Mode.
The querying
of the standard battery settings starts. After
Boot
Mode
is ended, the automatic reset of the
battery is activated. With this, the battery is
ready for operation immediately afterwards.
8.
Press the
OK
button (1).
9.
Set the
CPU Frequency
value (1) to 8.00 MHz.
Set the
Clock Mode
value (2) to 0.
Set the
CKM
value (3) to 8.
Set the
CKP
value (4) to 4.
Press the
Further
button (5).