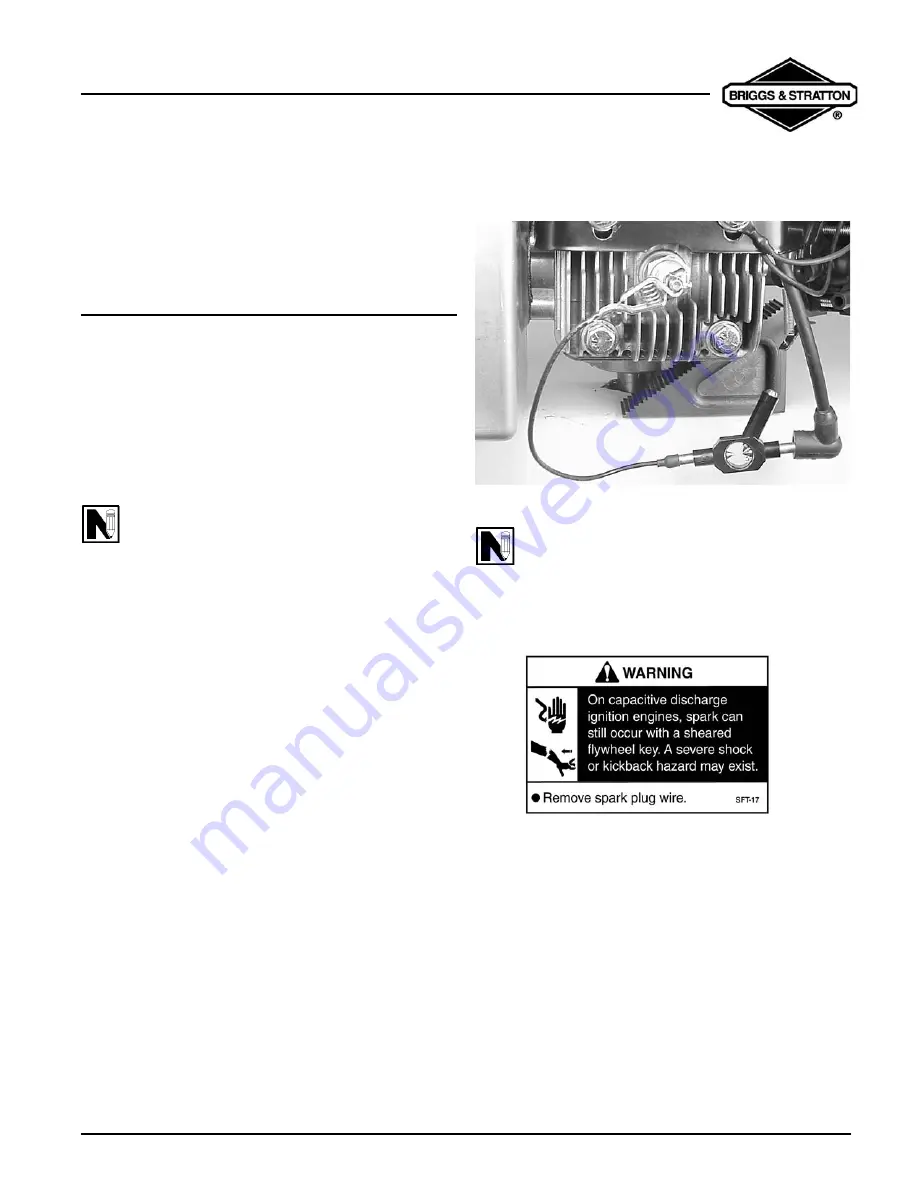
2-Cycle Snow Engine
Section 2 - Troubleshooting
Page 5
SECTION 2
TROUBLESHOOTING
GENERAL TROUBLESHOOTING
INFORMATION
Most complaints concerning engine operation can be
classified as one or a combination of the following:
• Will not start
• Hard starting
• Lack of power
• Runs rough
• Vibration
NOTE
: What appears to be an engine
malfunction may be a fault of the powered
equipment rather than the engine. If equipment is
suspect, see Equipment Affecting Engine
Operation.
Systematic Check
If the engine is hard starting or will not start and the
cause of malfunction is not readily apparent, perform a
systematic check in the following order:
• Ignition
• Carburetion
• Compression
This check-up, performed in a systematic manner, can
usually be done in a matter of minutes. It is the quickest
and surest method of determining the cause of failure.
Check Ignition
With stop switch in
ON/RUN
position and spark plug
installed, attach a
#19368
ignition tester to the spark plug
lead and ground the other end of the tester as shown in
figure 14. Operate the starter. If a strong, steady spark is
observed at the tester gap, you may assume the ignition
system is functioning satisfactorily.
Fig. 14
NOTE
: Engines equipped with capacitive
discharge ignition system will still display spark
at tester with a partially or fully sheared flywheel
key. A partially sheared flywheel key will affect
ignition timing and engine performance.
If spark does not occur look for:
• Shorted stop switch
• Shorted ground wire
• Incorrect armature air gap
• Armature failure
Engine Misfires
If engine runs but misses during operation, a quick check
to determine if ignition is or is not at fault can be made by
installing Tool
#19368
tester between the spark plug lead
and spark plug (Figure 15). A spark miss will be obvious
Summary of Contents for 276535
Page 1: ...2 Cycle Snow Engine 0 2 CYCLE SNOW ENGINE REPAIR MANUAL MANUAL NUMBER 276535...
Page 3: ...2 Cycle Snow Engine ii...
Page 4: ...2 Cycle Snow Engine iii...
Page 14: ...2 Cycle Snow Engine Section 2 Troubleshooting Page 8...
Page 38: ...2 Cycle Snow Engine Section 6 Final Adjustments Specifications Page 32...