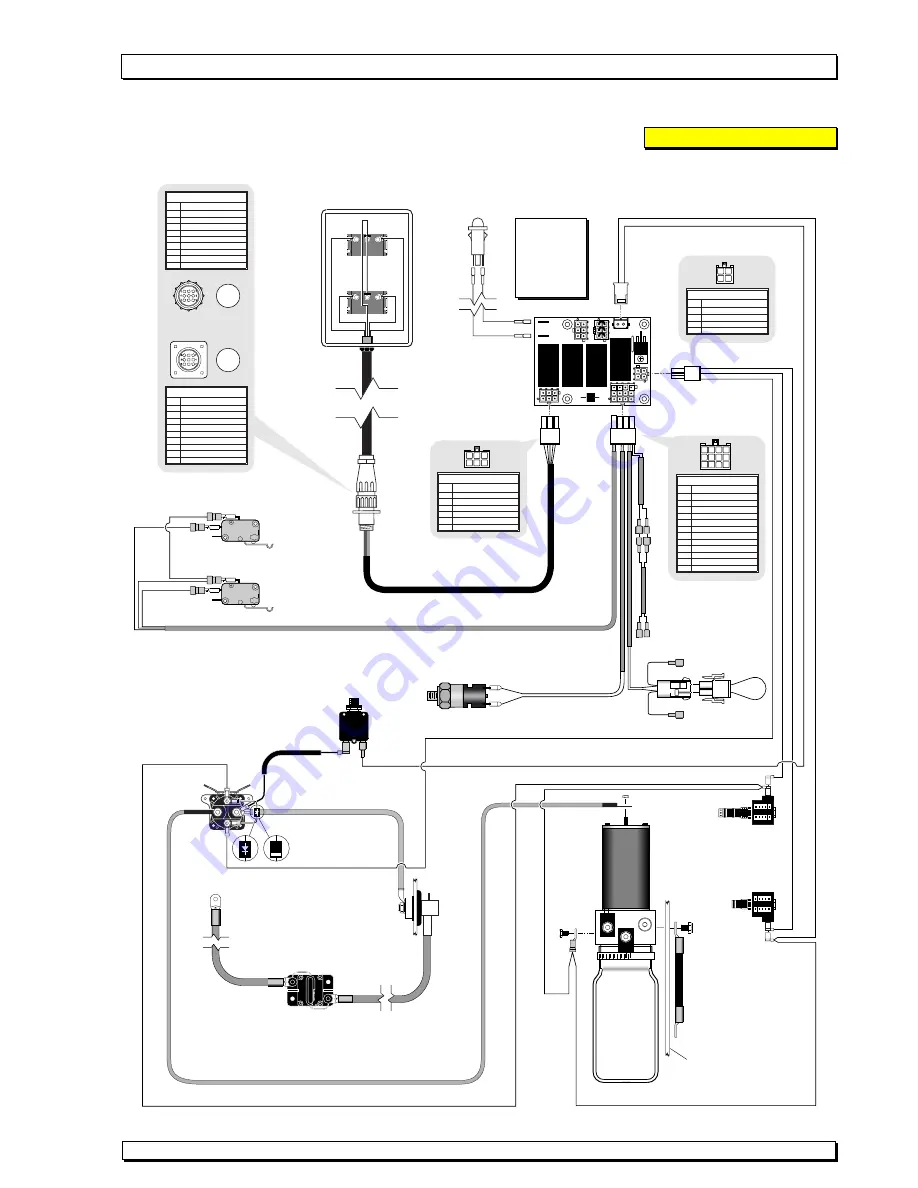
Page 3
Series
02
VL917IB
Supplement 29682
Series
02
VL917IB
Supplement 29682
Series
02
VL917IB
Wiring Diagram
Note:
Shown with lift in stowed position.
Circuit Sentry
(
Circuit Breaker)
Bat.
Aux.
J3
J5
J1
Lift
Power Cable
Pump Module
Power Feed
Connects to
Vehicle Battery
(+) Positive Post
#13362A
Lead Wire
GN
PIN #1
PIN #2
GN
BK
or
Note polarity of diode. It
must be oriented as shown.
Detail at left shows two different
styles of diode identification.
BK
BK
GN
GN
GN
GN
GN
GN
GN
R
R
R
R
Pump Ground
Ground
S
Unfold / Down
Microswitch
(Outboard)
C-H
COM
NO
NC
N.O.
N.C.
COM.
S
Up / Fold
Microswitch
(Inboard)
C-H
COM
NO
NC
N.O.
N.C.
COM.
R
R
Y
R
R
GN
Y
BK
R
R
R
W
W
GN
R
R
R
BK
R
Up/Fold
Solenoid
Motor Power Feed Wire
Circuit
Breaker
Control
Board
Power / Interlock
LED
Pump
Mounting
Plate
(Side view of solenoids
removed from pump.)
Hydraulic
Pump
Down
Unfold
BK
PIN #1
BK
BK
R
R
Interlock
Jumper
(-) Interlock
(+) Interlock
Down
Valve
Unfold
Valve
To Seat Belt
Front Pump Only
PIN #2
R
BK
Pump Mounted
Platform Sensor
Pressure Switch
J2
J6
J4
J13
Red
J14
White
Y
GN
Fold/Unfold
Switch
GN
BK
W
BN
Up/Down
Switch
Switch Box
(As Viewed From Terminal
Side of Switch)
BK
R
BK
W
NOT USED
GREEN - 6 COND.
WHITE - 6 COND.
BROWN - 6 COND.
YELLOW - 6 COND.
BLACK - 6 COND.
NOT USED
NOT USED
NOT USED
6
5
4
3
2
1
COLOR
NO.
9-COND WIRE CODE
7
8
9
BLACK (SEATBELT)
BLACK (MICROSWITCH)
GREEN (MICROSWITCH)
RED (MICROSWITCH)
RED (INTERLOCK)
BLACK (INTERLOCK)
RED (SEATBELT)
NOT USED
NOT USED
6
5
4
3
2
1
COLOR
NO.
12-COND WIRE CODE
7
8
9
BLACK (PRESSURE SW.)
10
RED (PRESSURE SW.)
11
NOT USED
12
RED
NOT USED
WHITE
BROWN
GREEN
BLACK
6
5
4
3
2
1
COLOR
NO.
6-COND WIRE CODE
NOT USED
YELLOW
BLACK
RED
4
3
2
1
COLOR
NO.
4-COND WIRE CODE
NOT USED
RED
GREEN
WHITE
BLACK
BROWN
NOT USED
NOT USED
NOT USED
6
5
4
3
2
1
COLOR
NO.
9-COND WIRE CODE
7
8
9
1 2 3
4 5 6
7 8 9
3 2 1
6 5 4
9 8 7
3
2
1
6
5
4
2
1
4
3
3
4
2
1
7
8
6
5
11
12
10
9
GND
12V
Negative
Positive
B
A
T
A U
X
GN
Y
GN
+
-
See
Lift Interlock
Instruction
section
for correct socket
position of 3-wire
jumper plug. The lift
is shipped with the
jumper installed in
Jack J6 (Negative
Logic Mode).
Revised: May 21, 2003