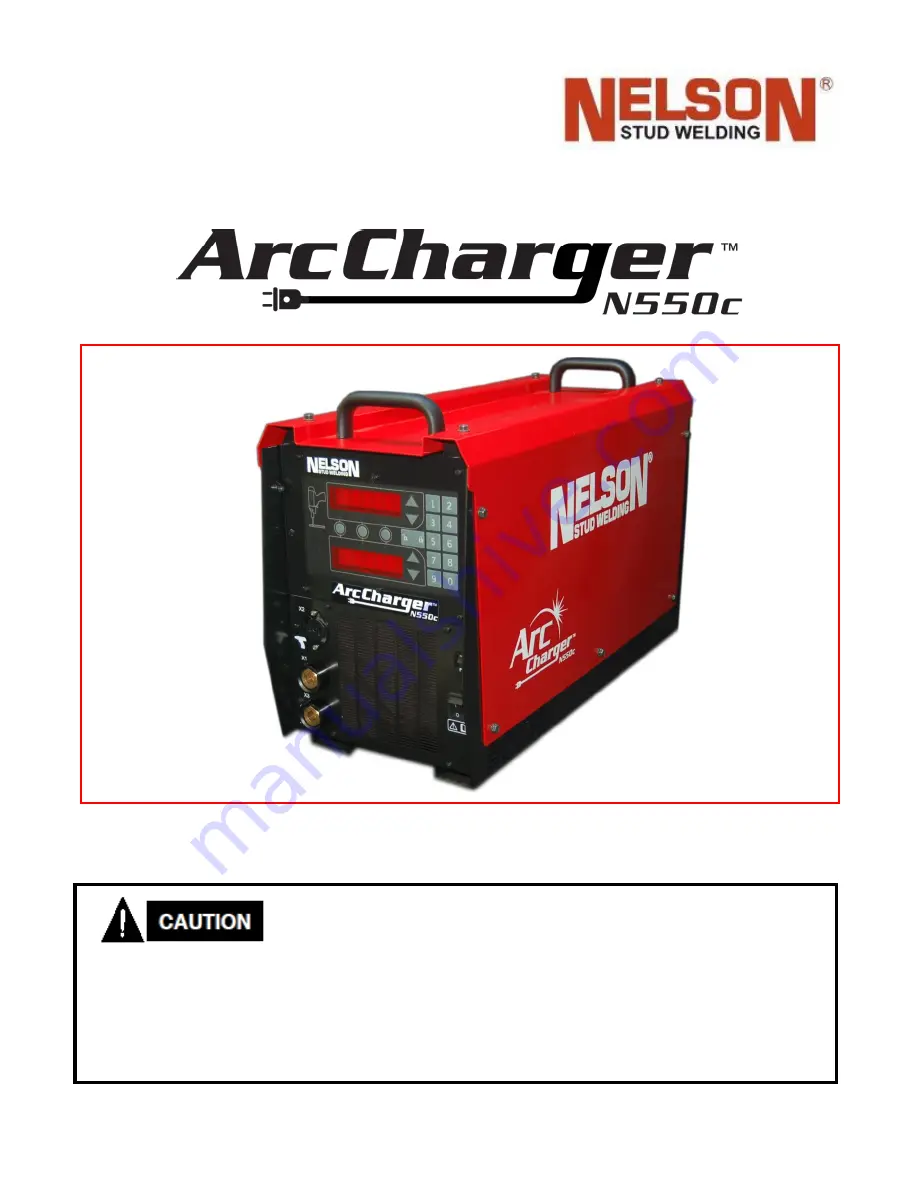
Part No. 729-110-040 Rev. 1.41 | June 2016
© 2016 Nelson Stud Welding, Inc. All Rights Reserved.
OPERATING THE
DOMESTIC & EXPORT
Operations Manual
For Software Version 1.03
These instructions are for experienced operators.
If you are not fully
familiar with the principles of operation and safe practices for arc welding
equipment, we urge you to read AWS SP -
“Safe Practices” available from the
American Welding Society.
Do not permit untrained persons to install,
operate or maintain this equipment. Do not attempt to install or
operate this equipment until you have read and fully understand
these instructions.
If you do not fully understand these instructions, contact
your supplier for further information. Be sure to read the Safety section before
utilizing this equipment.
Summary of Contents for ArcCharger N550C DOMESTIC
Page 18: ...Part No 729 110 040 Rev 1 41 June 2016 2016 Nelson Stud Welding Inc All Rights Reserved 17 ...
Page 60: ...Part No 729 110 040 Rev 1 41 June 2016 2016 Nelson Stud Welding Inc All Rights Reserved 59 ...
Page 62: ...Part No 729 110 040 Rev 1 41 June 2016 2016 Nelson Stud Welding Inc All Rights Reserved 61 ...
Page 64: ...Part No 729 110 040 Rev 1 41 June 2016 2016 Nelson Stud Welding Inc All Rights Reserved 63 ...